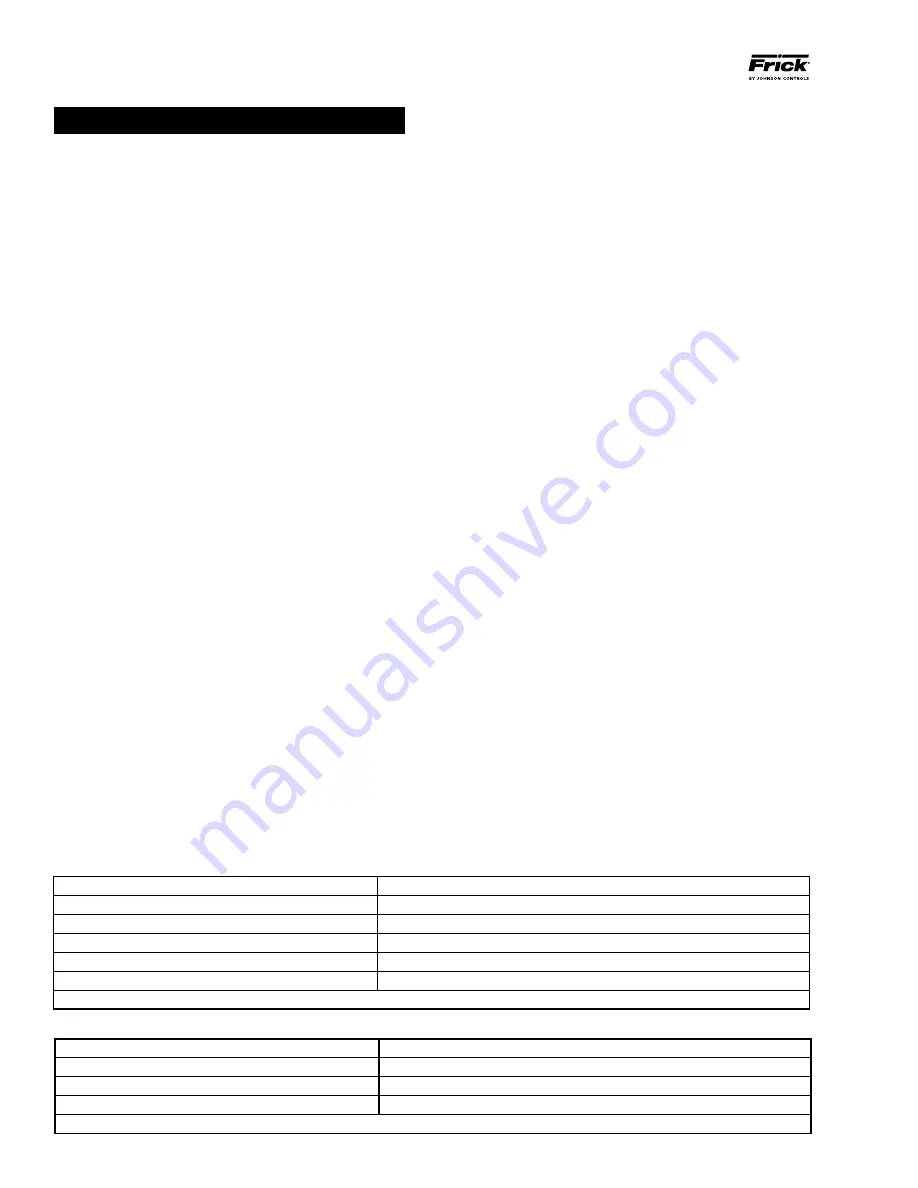
FRICK
®
POWERPAC
™
MAINTENANCE
170.600-IOM (JUN 11)
Page 14
TABLE 1 - EXCESSIVE CONDENSING PRESSURE
Cause
Remedies
Insufficient water flow through the condenser
Adjust water supply or clean the strainer
Fouling in the condenser
Clean the condenser
Overheated cooling water
Obtain colder cooling water or reduce compressor capacity
The plant is overcharged
Drain refrigerant into an empty vessel
Air or noncondensable gases in the system
Remove air from the condenser
A condensing temperature 2°F lower results in 1% additional cooling capacity.
TABLE 2 - EVAPORATING TEMPERATURE TOO LOW
Causes
Remedies
Fouling in the evaporator
Clean the evaporator
Oil in the evaporator
Inspect the oil return system
Insufficient refrigerant charge
Add more refrigerant to the plant.
An evaporating temperature 2°F higher results in 4% additional cooling capacity.
MAINTENANCE
The operator must be familiar with the unit and this instruc-
tion manual in order to service and maintain the PowerPac
™
unit properly.
Before dismantling any portion of the unit, it is important to
make sure that the pressure in the unit or its components
has been equalized to atmospheric pressure. Parts to be
dismantled must not contain refrigerant.
Operator safety is improved by using gloves and face pro-
tection. It is suggested that a suitable gas mask be at hand.
It is useful to have spare gaskets available for replacement
use.
Only use
the recommended Frick oil specified
for your
PowerPac
™
unit. When handling refrigerants, oils, brines etc.,
personal safety and protection of the environment should
have a very high priority.
Use only the refrigerant for which the unit was originally
designed.
Before starting the dismantling/servicing process, remove
all main fuses, switch off all electric components on the
compressor/unit, and
LOCK THE MAIN SWITCH
.
Make sure that the motor cannot start up inadvertently.
Make sure that there is no over-pressure and no refrigerant
in the part to be dismantled.
Close all necessary stop valves.
Use the prescribed tools and check that they are properly
maintained and in good working condition. In explosion-proof
areas, use tools suited for this specific purpose. Also use
electrical protection equipment and tools suited for electrical
operation purposes.
Use only Johnson Controls original spare parts; other parts
may impair the safety of the compressor/unit.
TROUBLESHOOTING AND
CAPACITY MEASUREMENT
OPERATING CONDITIONS
Variations in pressures and temperatures within the cooling
cycle can provide information about the operating state of
the chiller package.
Suction and condensing pressures, as well as the tempera-
tures of suction and discharge gas, can provide important
information.
Small changes in the variable pressures and temperatures
are sufficient to create considerable changes in the operat-
ing conditions.
These issues highlight the importance of using the Operat-
ing Log.
TROUBLESHOOTING
An error in the system often leads to changes in operating
conditions, but not to a total shutdown. For that reason,
check the operating state of your PowerPac
™
at regular
intervals.
Refer to compressor manuals for further detail.
CAPACITY MEASUREMENT
If the system does not produce the capacity indicated, check
for possible sources of error. Before taking any action, check
the possible causes indicated in Tables 1 and 2 below.
INCORRECT CAPACITY MEASURING
The PowerPac
™
chiller is equipped with a Frick
®
Quantum
™
LX
control system for control and regulation of the package
capacity according to leaving brine/water temperature. The
Quantum
™
LX has a display to read the operating conditions.
The pressures and temperatures indicated are not exact.
They can only be used to perform approximate capacity
calculations. Exact measurements should be calculated in
accordance with ASHRAE procedures.