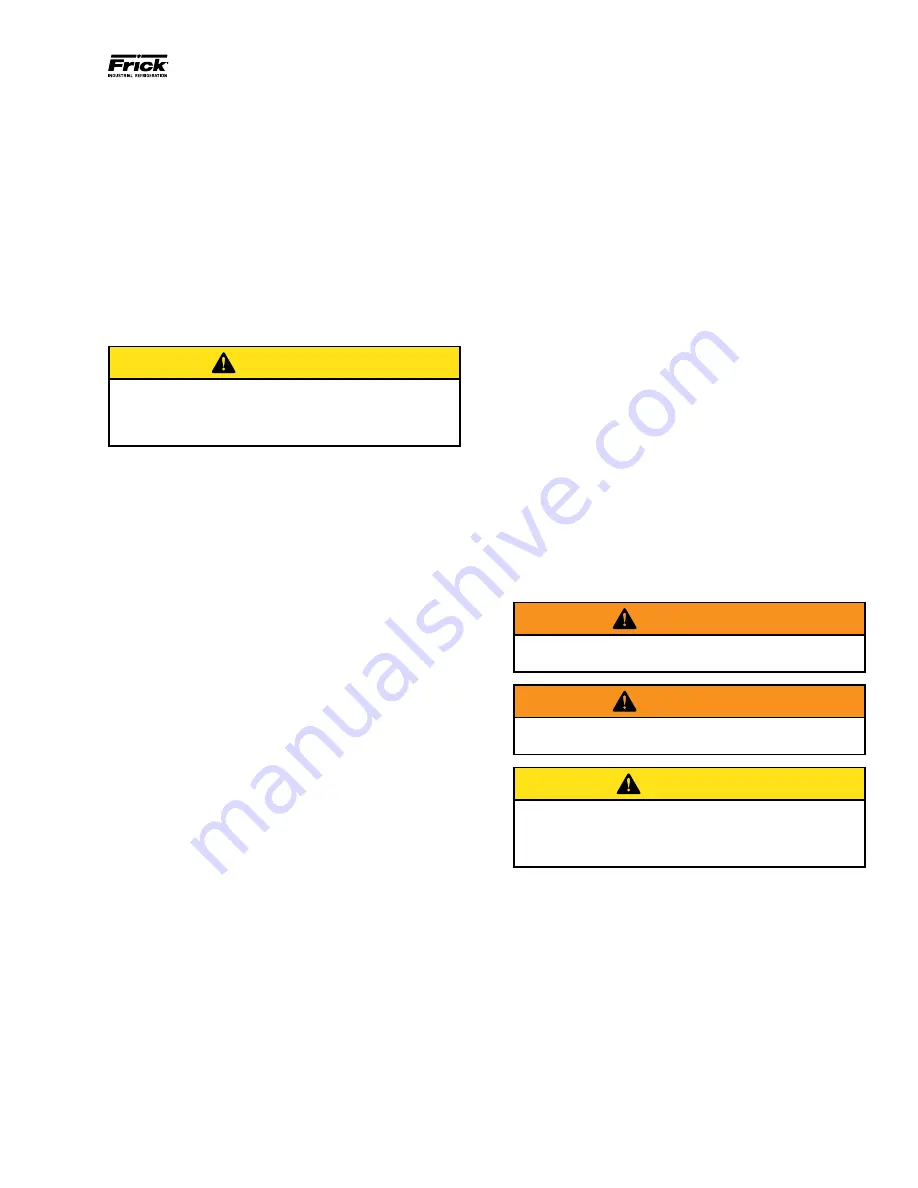
070.550-IOM (JUN 2016)
Page 13
NGC GAS ROTARY SCREW COMPRESSOR
INSTALLATION
OIL PUMP
NGC models that are supplied with an oil pump use an
integral seal–less type. You must connect to the inlet and
outlet of the pump. It is recommended that a strainer be
mounted upstream to protect the pump. The pump is a
positive displacement gear type that must have a safety
relief valve to ensure the oil pressure will not be more than
50 psi above compressor discharge pressure for all models
except NGC 400/450. For some applications, NGC 400 and
450 models require the pump pressure boost to reduce
axial load on the male rotor. This is done to increase the life
of the male axial bearing (see CoolWare). These models use
pressure boost up to 50 psi above compressor discharge
and require an appropriate safety relief valve.
CAUTION
If oil pressure exceeds 55 PSI above compressor dis-
charge it could cause catastrophic compressor failure
due to male axial bearing failure. See CoolWare for
your application’s requirements.
The fixed volume flow of the pump will require a parallel
bypass-line for some applications. Please see CoolWare
™
for the specific oil flow for your application.
Nominal oil pump flow at 1800 rpm inlet drive speed is:
NGC 100 and 150
32 GPM
NGC 200, 250 and 450
56 GPM
NGC 300 and 400
75 GPM
OIL HEATER(S)
Your package must be equipped with oil heaters that provide
sufficient heat to prevent
condensation from occurring
during shutdown cycles.
OIL COOLING REQUIREMENTS
Oil cooling is required to keep the temperature of the
discharge gas from exceeding 300°F. The discharge
temperature must be high enough to prevent moisture from
condensing in the compressor and oil separator. The use of
a three-way mixing valve is recommended to keep the oil
temperature in the proper range.
COUPLING
COMPRESSOR ROTATION IS CLOCKWISE WHEN FACING
THE END OF THE COMPRESSOR SHAFT
Confirm engine will rotate the compressor clockwise before
installing the coupling.
COMPRESSOR/MOTOR COUPLING REQUIREMENTS
Coupling weight is an important consideration to avoid any
issues with lateral critical speeds. Coupling weight should
not be excessive. Use a clamp type hub for ease of seal
access, and to maintain link precision. Using a shrink-type
hub is not required or recommended.
NGC compressors are arranged for direct engine drive and
require a flexible drive coupling to connect the compressor
to the motor.
Coupling must be selected and installed so that it doesn’t
transmit any axial load to the compressor shaft.
Set up the minimum distance between compressor shaft
and engine shaft to allow for seal removal and gear cover
removal (see Outline drawings).
1. Coupling must be able to take up any misalignment be-
tween motor and compressor. It is critical to the life of
the shaft seal that misalignment is kept to the minimum
possible value. Be sure to follow the coupling manufac-
turer’s guidelines for checking and correcting any mis-
alignment.
2. For all engine applications, a torsional vibration analysis
of the complete system must be performed including:
engine - coupling - compressor (including gearing). This
is to ensure that the system will run well away from any
natural frequencies. See page 19 for driveline and gear
dimensions for torsional vibration analysis. Data for tor-
sional stiffness, rotating mass and inertia of the com-
pressor components is available.
COUPLING ALIGNMENT REQUIREMENTS
The life of the compressor shaft seal and bearings is depen-
dent upon proper coupling alignment. Coupling alignment
must be performed prior to start-up. After the package has
been installed on the job site, alignment must be checked
again and if necessary corrected prior to start-up. After a
few hours operation, the alignment must be checked while
the package is still hot. Correct hot alignment is critical to
ensure the life of the shaft seal and compressor bearings.
Dial indicators or another appropriate measuring device are
to be used to determine the Total Indicator Runout.
WARNING
TOTAL INDICATOR AXIAL RUNOUT MUST NOT EXCEED
.004” (TIR).
WARNING
TOTAL INDICATOR RADIAL RUNOUT MUST NOT
EXCEED .004” (TIR).
CAUTION
CARE MUST BE USED WHEN CORRECTING FOR PARAL-
LEL MISALIGNMENT TO ENSURE THAT THE AXIAL
SPACING AND ANGULAR MISALIGNMENT IS NOT SIG-
NIFICANTLY DISTURBED.
Indicator bracket sag must be checked as all brackets have
some flexibility. The best way to measure this is to attach
the dial indicator and bracket on a pipe at the coupling span
distance. Zero the indicator in the 12:00 position, and rotate
the pipe so the indicator is in the 6:00 position. The reading
on the indicator in the 6:00 position is the bracket sag. This
value must be included in the dial indicator readings when
affixed to the coupling for an accurate alignment. See Fig. 8.