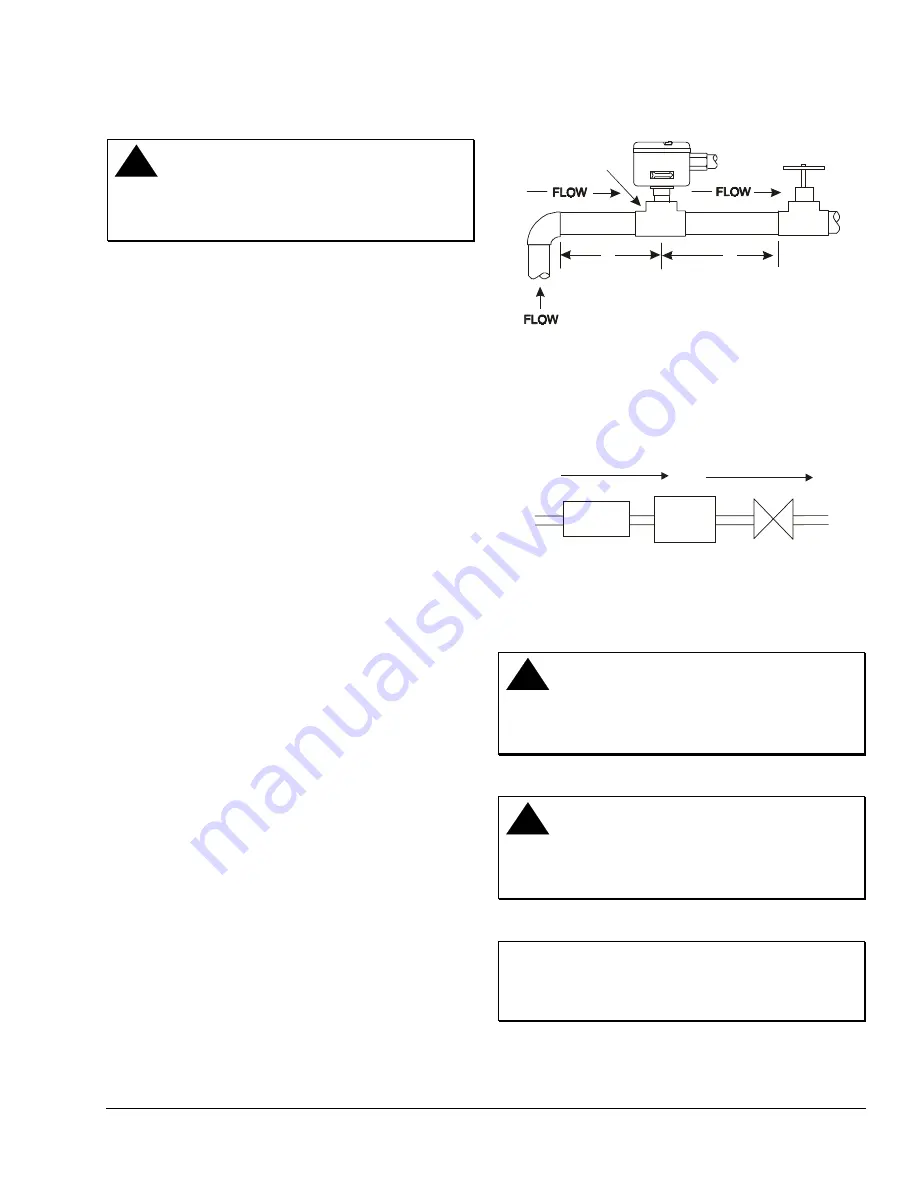
F61 Series Standard Flow Switches Installation Instructions
3
Mounting
!
CAUTION: Risk of Equipment Damage.
To avoid damaging the switch, do not tighten the
switch to the tee by grasping the switch enclosure.
Use only the wrench flats provided.
Mount the F61 Series Flow Switch, using the following
guidelines:
•
Install the switch so that the cover and interior are
accessible.
•
Mount the switch so that the flow of fluid is in the
direction of the arrow on the switch casing.
•
Use a pipe union on each side of the flow switch to
allow easy removal or replacement.
•
Mount the switch so that the pipe does not extend
too far into the flow switch casing.
•
Use pipe thread sealer on male threads only.
•
Do not remove the cover gasket or the wire
grommet from the conduit opening.
For 1 in. pipe installation, mount the F61 flow switch in
a standard 1 in. x 1 in. x 1 in. tee. For larger sizes of
pipe, use a reducing tee to keep the flow switch close
to the pipe and provide adequate paddle length in the
flow stream.
Example: Use a 2 in. x 2 in. x 1 in. tee for a
2 in. pipe. If a standard 2 in. x 2 in. x 2 in. tee is
used, install a face or hex bushing in the top
opening to reduce it to 1 in.
Mount the flow switch so the terminals or wire leads
are easily accessible for wiring. Screw the flow switch
in position so the flat of the paddle is at a right angle to
the flow. The arrow on the side of the case must point
in the direction of the flow.
Location Considerations
Mount the F61 flow switch in a horizontal pipeline or a
vertical pipeline with upward fluid flow. Do not use in a
vertical pipeline with downward flow. When mounted in
a vertical pipe with upward flow, the switch trips at a
slightly higher flow than shown in Table 3 through
Table 6
,
due to the effect of gravity on the switch
mechanism.
Mount the F61 flow switch in a section of pipe where
there is a straight run of at least five pipe diameters on
each side of the flow switch from the nearest elbow,
valve, or other pipe restriction. See Figure 5.
Dimension must be at least
five pipe diameters from the nearest
elbow, valve, or other pipe restriction.
A
A
A
Tee or Welded
Half-coupling
Figure 5: Required Piping Distance
Do not subject the flow switches to water hammer.
Use a suitable water hammer arrester if a fast-closing
valve is located downstream of the flow switch. See
Figure 6.
Flow
Switch
Water
Hammer
Arrester
Valve
Flow
Figure 6: Water Hammer Arrester Location
Schematic
Wiring
!
WARNING: Risk of Electrical Shock.
Disconnect power supply before making electrical
connections. Failure to follow this precaution may
result in electrical shock or death.
!
CAUTION: Risk of Equipment Damage.
Using terminal screws other than those provided will
void the warranty and may damage the switch. Use
only the terminal screws furnished.
IMPORTANT:
To prevent moisture from entering
and condensate from forming inside the NEMA 3R
enclosure, do not remove the cover gasket or the
wire grommet from the conduit opening.