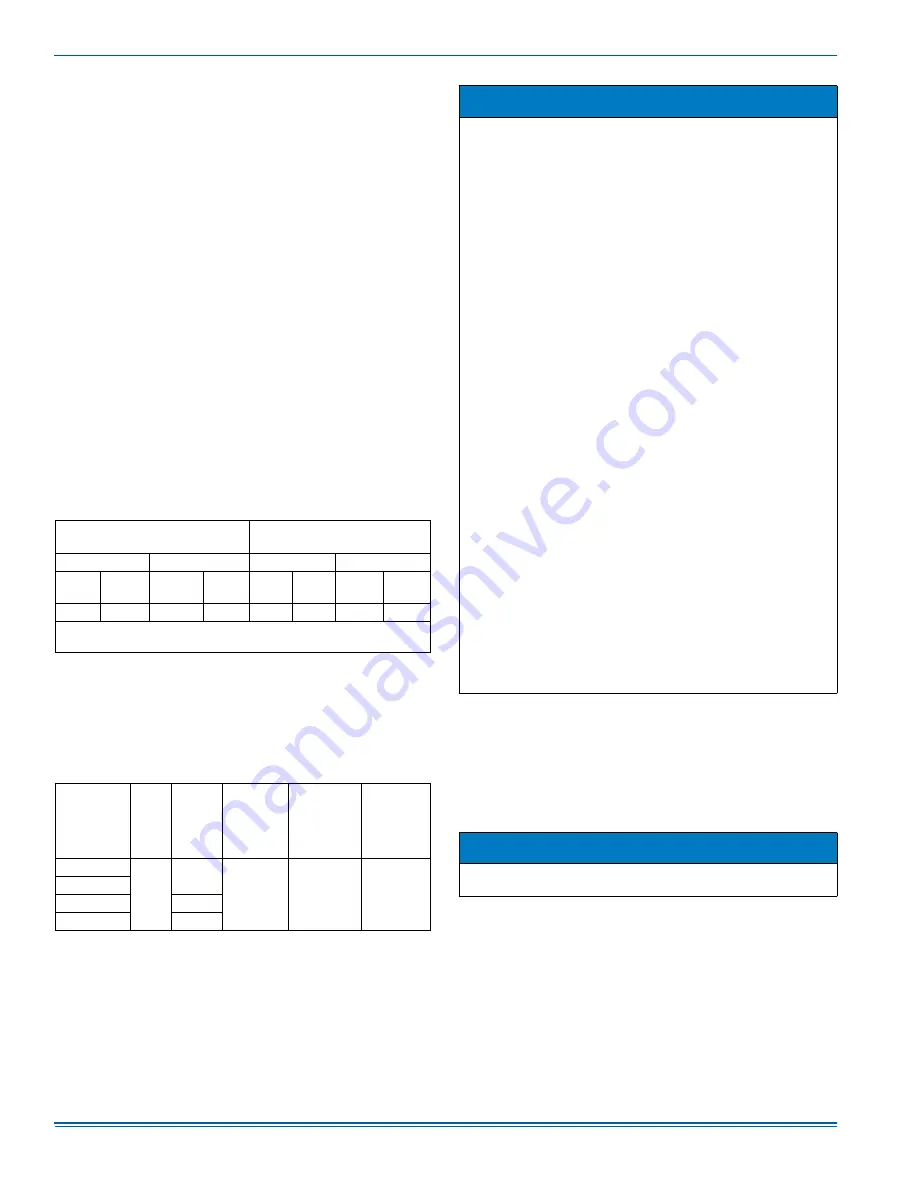
5156631-UIM-G-0417
2
Johnson Controls Unitary Products
INSPECTION
As soon as a unit is received, it should be inspected for possible dam-
age during transit. If damage is evident, the extent of the damage
should be noted on the carrier’s delivery receipt. A separate request for
inspection by the carrier’s agent should be made in writing. See Local
Distributor for more information.
Requirements For Installing/Servicing R-410A Equipment
•
Gauge sets, hoses, refrigerant containers, and recovery system
must be designed to handle the POE type oils, and the higher
pressures of R-410A.
•
Manifold sets should be high side and low side with low side
retard.
•
All hoses must have a 700 psig service pressure rating.
•
Leak detectors should be designed to detect HFC refrigerant.
•
Recovery equipment (including refrigerant recovery containers)
must be specifically designed to handle R-410A.
•
Do not use an R-22 TXV.
LIMITATIONS
The unit should be installed in accordance with all National, State and
Local Safety Codes and the limitations listed below:
1.
Limitations for the indoor unit, coil, and appropriate accessories
must also be observed.
2.
The outdoor unit must not be installed with any duct work in the air
stream. The outdoor fan is the propeller type and is not designed
to operate against any additional external static pressure.
3.
The maximum and minimum conditions for operation must be
observed to ensure a system that will give maximum performance
with minimal service.
4.
The maximum allowable equivalent line length for this product is
80 feet.
Standard Lineset Applications
Maximum allowable lineset varies depending on the vertical separation
between the evaporator and condenser. See Table 2 for allowable line
set lengths and sizing.
Unit Reduced Capacity Conditions
SECTION III: UNIT INSTALLATION
LOCATION
Before starting the installation, select and check the suitability of the
location for both the indoor and outdoor unit. Observe all limitations and
clearance requirements.
The outdoor unit must have sufficient clearance for air entrance to the
condenser coil, air discharge, and service access. See Figures 1 & 2.
If the unit is to be installed on a hot sun exposed roof or a paved ground
area that is seasonally hot, the unit should be raised sufficiently above
the roof or ground to avoid taking the accumulated layer of hot air into
the outdoor unit (which can cause the unit to derate prematurely).
If the system is being installed during seasonally cold weather of 55°
F
or below, the preferred method is to weigh in the charge. For charging
or checking the system charge at 55
°
F or below, refer to the “Optional
Cold Weather Charging” procedures near the end of SECTION VI:
SYSTEM CHARGE. There is an “Optional Cold Weather Charging”
accessory kit to prevent the outdoor unit from taking in cold air below
55
°
F. The kit part number can be found in the list of accessory kits on
the UPGNET web site.
Provide adequate structural support for the unit.
TABLE 1:
Minimum / Maximum Operating Limit Conditions
AIR TEMPERATURE AT
OUTDOOR COIL, ° F (° C)
AIR TEMPERATURE AT
INDOOR COIL, ° F (° C)
Min.
Max.
Min.
Max.
DB
Cool
DB
Heat
DB Cool
DB
Heat
WB
Cool
DB
Heat
WB
Cool
DB
Heat
35(2)* -20(-29) 125(52)* 75(24) 57(14) 50(10) 72(22)
80(27)
*
Reference the NOTICE under the “Unit Reduced Capacity Conditions”
section.
TABLE 2:
Allowable Vertical Linesets.
Model
Liquid
Line
Suction
Line
Max Line
Length -
Units on
Equal
Level
Max Suction
Line Riser -
If OD Unit is
Above ID
Unit
Max Liquid
Line Riser -
If OD Unit
is Below ID
Unit
24
3/8”
3/4”
80 feet
25 feet
25 feet
36
48
7/8”
60
1-1/8”
NOTICE
Intelligence Power Module (IPM) Temperature Protection:
If excessive (IPM) inverter temperatures are sensed, the compressor
speed / capacity is reduced every 60 seconds until an acceptable
condition is reached.
When the inverter temperature returns to an acceptable level, the
system returns to normal operation.
Over / Under Current Protection: If a low or high Current Condition
is sensed, the compressor speed / capacity is reduced every 30 sec-
onds until an acceptable current level is reached.
When the system reaches an acceptable current level, the compres-
sor and fan return to normal operating conditions.
Over / Under Voltage Protection: If a low or high supply Voltage
Condition is experienced (below 197 VAC or above 252 VAC), the
compressor speed / capacity is automatically reduced every 15 sec-
onds until an acceptable voltage level is sensed.
When an acceptable voltage level is sensed, the system automati-
cally returns to a normal state of operation.
High Outdoor Ambient Temperature Protection: During high out-
door ambient temperature conditions above 109°F (43°C), the com-
pressor speed reduces to protect the system. If the outdoor ambient
temperature goes above 125 °F (52°C), the system goes into a soft-
lockout condition halting operation for system protection. Consider
these limitations when installing any of the heat pumps included in
this document.
When the system reaches acceptable operating conditions, the sys-
tem returns to normal operation.
High Altitude Protection: If the unit is installed in Altitudes of 6,500
ft / 2,000 m above sea level or higher, the compressor and outdoor
fan reduce speeds to protect the system. It is not recommended
these units be installed at altitudes greater than 6,500 ft / 2,000 m
above sea level.
Low Ambient Protection:
Cooling mode: The unit automatically adjusts to maintain cooling
operation in outdoor ambient conditions down to 35° F (2° C). The
unit reduces capacity and or cycles off if asked to provide cooling
when the outdoor temperature is at or below these conditions.
Heating Mode: The unit provides compressor heat down to an out-
door ambient temperature of -20° F (-29° C). As the outdoor ambient
temperature reduces, available heat reduces for all air source heat
pumps. Make sure the balance point and auxiliary heat are appropri-
ately set and sized for the application of the heat pump.
NOTICE
For multiple unit installations, units must be spaced a minimum of 24”
(61 cm) apart (coil face to coil face).