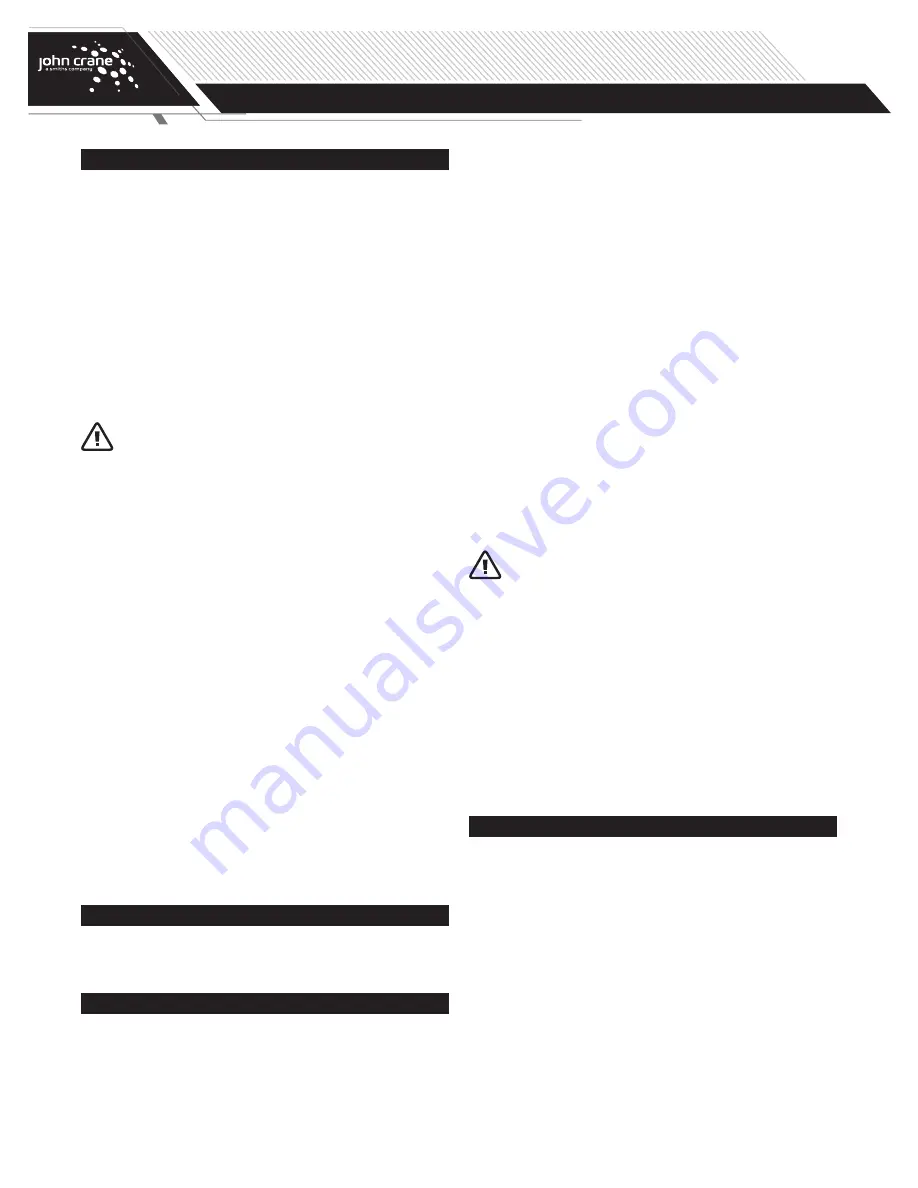
ROPAC COMPONENT SEALS
Installation, Operation & Maintenance Instructions
2
TYPE R33/34/50
5. Transportation and Storage
Transport and store the seal in its original packaging. To ensure
seals remain in good condition they should be stored in the following
environment:
1. Dry and dust-free
2. Ventilated at room temperature
3. Protected from direct effects of heat and ultraviolet light
4. All the elastomers used in the mechanical seal have a minimum shelf
life of 5 years except for butyl rubber which has a minimum shelf life
of 2 years. We recommend that the elastomers be replaced at these
intervals. It is also recommended that the elastomer replacement be
carried out by John Crane personnel.
If used seal parts are to be shipped they must be
cleaned and decontaminated before shipping. It is
the responsibility of the machine user to ensure
that any parts being shipped have appropriate
safe-handling instructions externally attached
to the package. Without this information there
will be a refusal to handle the goods. If required
a decontamination/transportation certificate is
available from John Crane. Refer to document
EDS1001.
For additional information on transportation and storage, contact your
local John Crane facility and request a copy of document I-Storage.
If any machine with an installed component seal has been stored with
preservatives, before putting it back into operation the seal must be
removed, cleaned and dried. Particular attention must be applied to the
cleanliness of the faces and condition of the elastomers. For an installed
cartridge seal we recommend returning the complete cartridge to John
Crane for cleaning.
ATTENTION
Ensure preservatives and cleaning agents do not affect
the elastomers.
ATTENTION
Once the seal is fitted on the machine and the position
is set using setting devices do not re-engage them for
transportation and storage.
6. Seal Installation
Refer to the appropriate seal family installation instructions. Do not
excessively compress the seal before or during installation.
7. Before Starting the Equipment
1. Check the machine at the coupling for proper alignment of the driver
or motor.
2. Ensure that the gland plate nuts/bolts are securely tightened
according to the pump manual instructions, and all screws are
securely fastened.
3. Complete the assembly of the pump and turn the shaft (by hand if
possible) to ensure free rotation.
4. Consult all available equipment operating instructions to check for
correctness of all piping and connections, particularly regarding seal
recirculation/flush, heating or cooling requirements, and services
external to the seal.
ATTENTION
This mechanical seal is designed to operate in a liquid,
so the heat energy it creates is adequately removed.
The following check should be carried out not only after
seal installation, but also after any period of equipment
inactivity.
5. Check that the seal chamber fluid lines are open and free of any
obstruction, and ensure that the seal chamber is properly vented and
filled with liquid — refer to the pump instruction manual.
ATTENTION
Except for dry running or gas lubricated seals which are
designed to operate without liquid, wet seals that are
operated without adequate liquid lubrication will often
give rise to a squealing noise from the seal area and
result in overheating and scoring or other damage to
the sealing surfaces, causing excessive emissions and a
reduced seal life.
Before start-up, ensure that all personnel and
assembly equipment have been moved to a safe
distance so there is no contact with rotating parts
on the pump, seal, coupling or motor.
ATTENTION
Seal installation should be handled only by
qualified personnel. If questions arise, contact
the local John Crane representative. Improper use
and/or installation of this product could result
in injury to the person and/or harmful emissions
to the environment, and may affect any warranty
on the product. Please contact the company for
information as to exclusive product warranty and
limitations of liability.
8. Maintenance
During operation, periodic visual external inspection of the seal should
be carried out. A measure of seal condition is the level of emission of the
process or barrier fluid and as no maintenance is possible while installed,
the seal should be replaced when emissions become unacceptable. It is
recommended that a spare seal be held in inventory to allow immediate
replacement of a removed seal.
ATTENTION
Machine adjustments that involve axial movement of the
shaft may cause damage to the seal while installed.
Before attempting impeller clearance adjustment with a cartridge seal,
refit the spacers then loosen all the drive collar socket set screws. With
the shaft in its new working position, tighten with new socket set screws
and remove the spacers. Keep the spacers for future use.
For a component seal (non-cartridge), remove the seal, adjust the
impeller clearance then re-fit the seal at its correct working length.