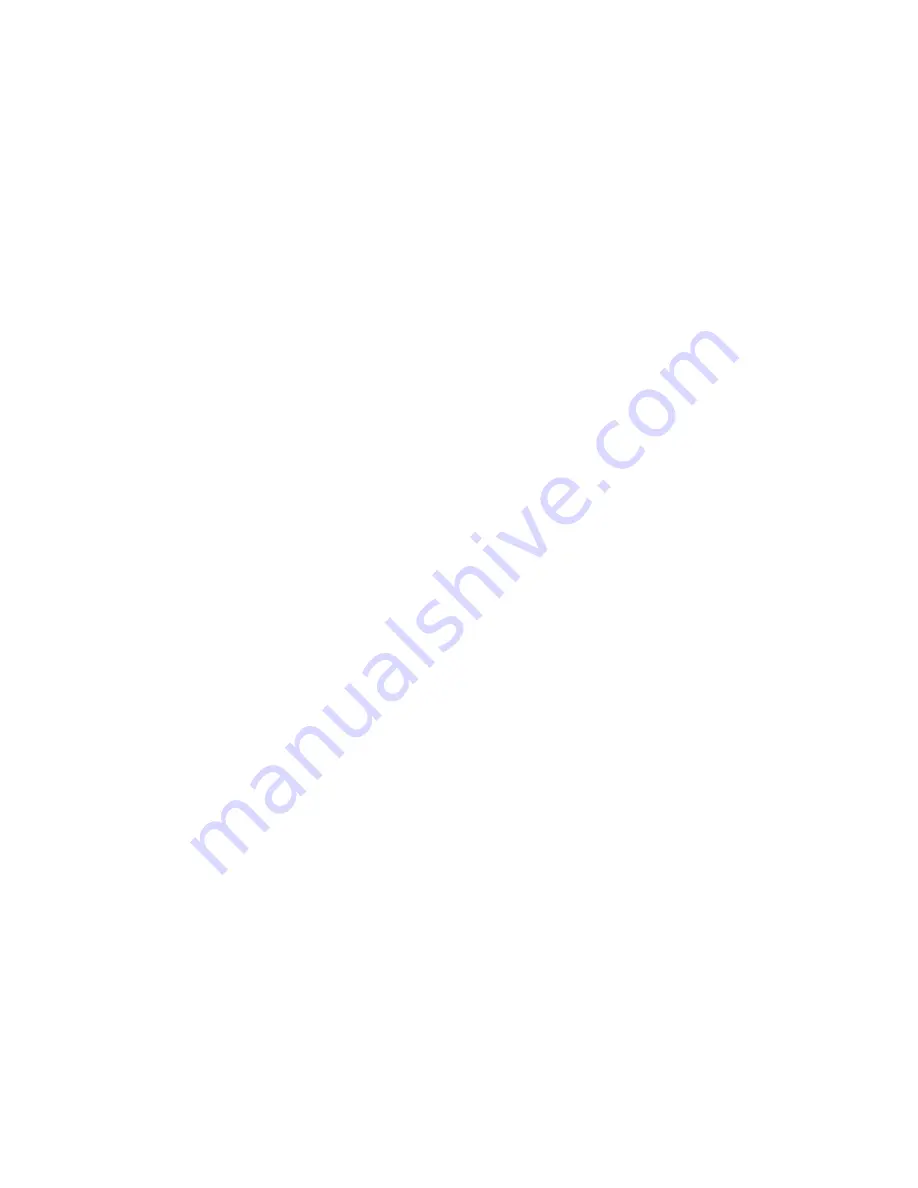
20 of 31
10 RECOMMENDED MAINTENANCE:
1.
Adjust level of lift daily.
2.
The lift should be greased at least once every two months. There are six (6) points on
each lift that will take grease: four (4) on the scissors hinges and one on each of the
two (2) hydraulic cylinder rod eyelet’s.
3.
The fluid level in the reservoir should be checked periodically. Be sure that the lift is
fully lowered when checking. The hydraulic fluids should be changed once every five
years. Use only ISO 32 hydraulic fluid.
4.
The roller tracks should always be kept clean and free of debris. This area should be
checked before any raising or lowering of the lift.
5. Inspect the operation of the lift daily. Raise and lower fully.
6. Inspect electrical and mechanical operations of all switches, electrical and mechanical.
7.
Lifts equipped with full floating rear slip plates and front radius turning plates, require to
be disassembled and cleaned once every 3 months. More frequently with lifts that are in
areas with more exposure to sand and salt.
NOTE: Locking pins should always be installed on front and rear plates before attempting
to drive a vehicle on or off the lift.
8.
If uneven lifting occurs as described in section 5.1.3 the crossmember(s) will need to be
re-adjusted.
Quarterly Slip Plate Maintenance
1.
Remove top Slip Plate covers by first removing the four (4) shoulder bolts on each cover.
2.
Remove polyethylene bearing cages insuring that all the delrin bearings remain in the
cages. Additional delrin bearings may be purchased if required.
3.
Clean runway surface and touch up any paint wear with a rust resistant paint. Allow
paint to dry thoroughly.
4.
To obtain optimum performance, the position of the slip plate bearing cage should be
rotated every quarter to change the wear pattern. With the first quarter maintenance, flip
the bearing cage over to the opposite side. With the second quarter maintenance, rotate
the bearing cage end-to-end. With the third quarter maintenance, flip bearing cage over
to the opposite side. Fourth quarter maintenance should see the bearing cage rotated
back to the position it started in.
5.
Quarterly maintenance will optimize performance and contribute to longer slip plate life.