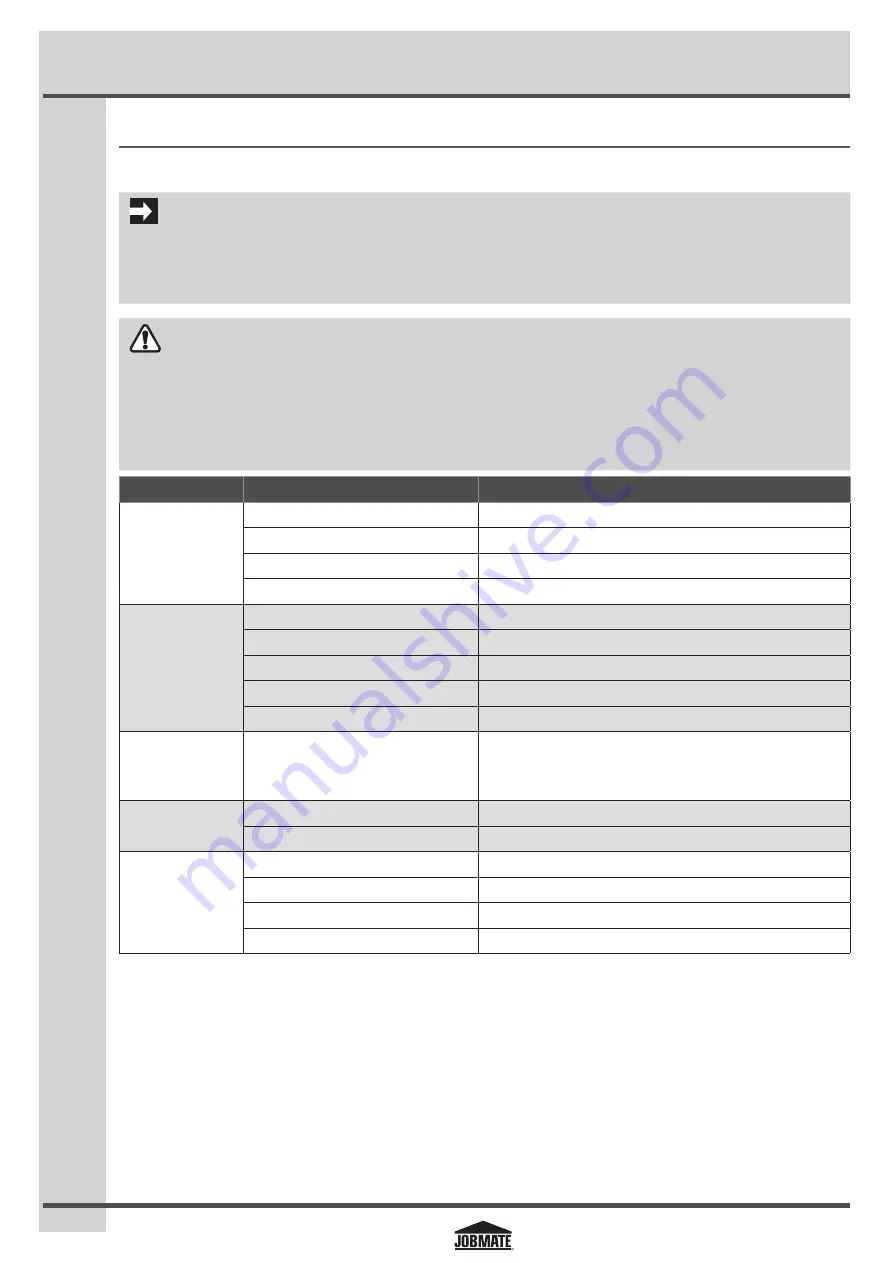
22
Troubleshooting
10. t
roubleShooting
The following chart lists common issues and solutions. Please read it carefully and follow all instructions closely.
IMPORTANT
If your unit still is not functioning properly once you have used this guide, please call the JOBMATE toll-free service number at
1-866-JOBMATE
(1-866-562-6283). Please do NOT bring the unit back to the store until you have called this number.
WARNING
•
IF ANY OF THE FOLLOWING SYMPTOMS APPEARS WHILE THE WELDER IS IN USE, TURN IT OFF AND DISCONNECT THE WELDER FROM
THE POWER SUPPLY IMMEDIATELY. FAILURE TO HEED THIS WARNING WILL RESULT IN SERIOUS PERSONAL INJURY OR DEATH.
•
REPAIRS MUST BE PERFORMED BY A QUALIFIED SERVICE TECHNICIAN ONLY.
PROBLEM
POSSIBLE CAUSE
SOLUTION
The welder does
not work when
the main switch is
turned on.
No power input.
Check the circuit or fuse of the power supply.
Power cord or power plug is broken.
Replace the power cord.
Main switch is broken.
Replace the main switch.
Transformer is broken
Replace the transformer.
The welder does not
weld.
Incorrect power input.
Check the power source.
Inadequate current at the output.
Check for proper grounding to the workpiece.
Poor connection of output cable.
Check the output connection.
Dirty surfaces.
Clean the surfaces.
Wrong welding wire.
Use the correct wire.
Blown fuse or
tripped circuit
breaker.
Inadequate fuse or circuit breaker.
Check whether the fuse in power supply is 20 A.
Arc is hard to start.
Wrong welding wire.
Use the correct wire.
Base metal not grounded properly.
Make sure the connection is good.
Inconsistent arc or
wire feed.
Not enough drive roller pressure.
Tighten the drive tension adjustor on wire feeder.
Spool hub tension too tight or loose.
Adjust the wing nut on the spool holder.
Contact tip worn or wrong size.
Replace the contact tip.
Rusty or corroded wire.
Replace the wire.