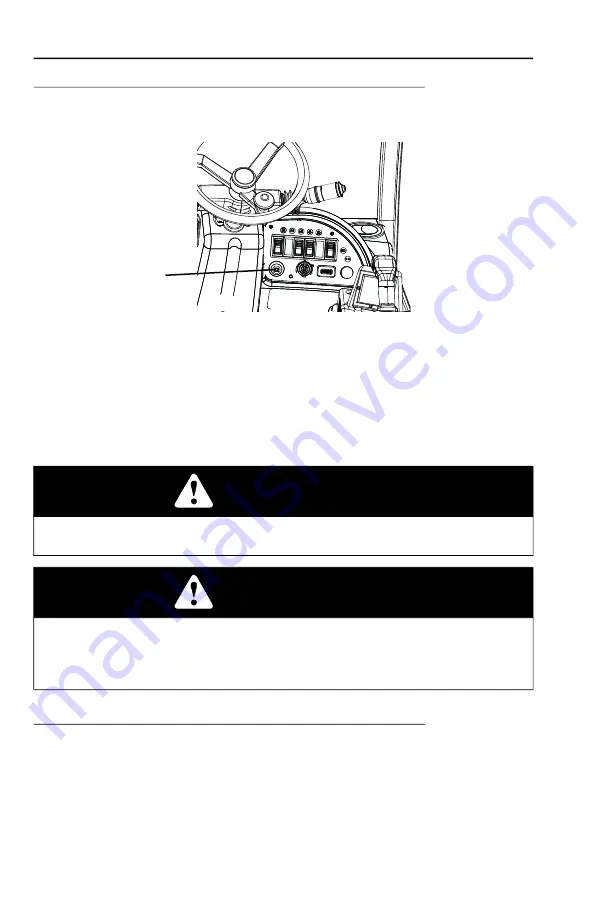
Section 3
-
Controls and Indicators
3
-
4
31211476
Park Brake
Park Brake Switch
Park brake switch (
1
) controls the application and release of the park brake. Indicator light
in switch illuminates to indicate brake is applied.
• Depress switch to engage park brake. With park brake applied, transmission will not
engage forward or reverse.
• Depress switch to disengage park brake.
Parking Procedure
1. Using service brake, stop telehandler in an appropriate parking area.
2. Follow
4.
WARNING
MACHINE ROLL-AWAY HAZARD.
Always depress park brake switch to "ON" position,
lower boom to ground and stop engine before leaving cab.
WARNING
CRUSH HAZARD.
Turning engine off applies the park brake. Applying park brake or
turning engine off while traveling will cause unit to stop abruptly and could cause load
loss. To stop the machine in an emergency, push down the Power/Emergency Stop
Switch to shut off power and stop engine.
ON0120
1
Summary of Contents for Skytrak 3013
Page 3: ...Revision Log a 31211476 Re v is ion L og REVISION LOG March 27 2020 A Original Issue of Manual...
Page 40: ...Section 2 Pre Operation and Inspection 2 14 31211476 This Page Intentionally Left Blank...
Page 60: ...Section 3 Controls and Indicators 3 20 31211476 This Page Intentionally Left Blank...
Page 98: ...Section 5 Attachments and Hitches 5 26 31211476 This Page Intentionally Left Blank...
Page 102: ...Section 6 Emergency Procedures 6 4 31211476 This Page Intentionally Left Blank...
Page 111: ...Section 7 Lubrication and Maintenance 7 9 31211476 This Page Intentionally Left Blank...
Page 122: ...Section 7 Lubrication and Maintenance 7 20 31211476 This Page Intentionally Left Blank...
Page 124: ...Section 8 Additional Checks 8 2 31211476 This Page Intentionally Left Blank...
Page 134: ...Inspection Maintenance and Repair Log Date Comments...