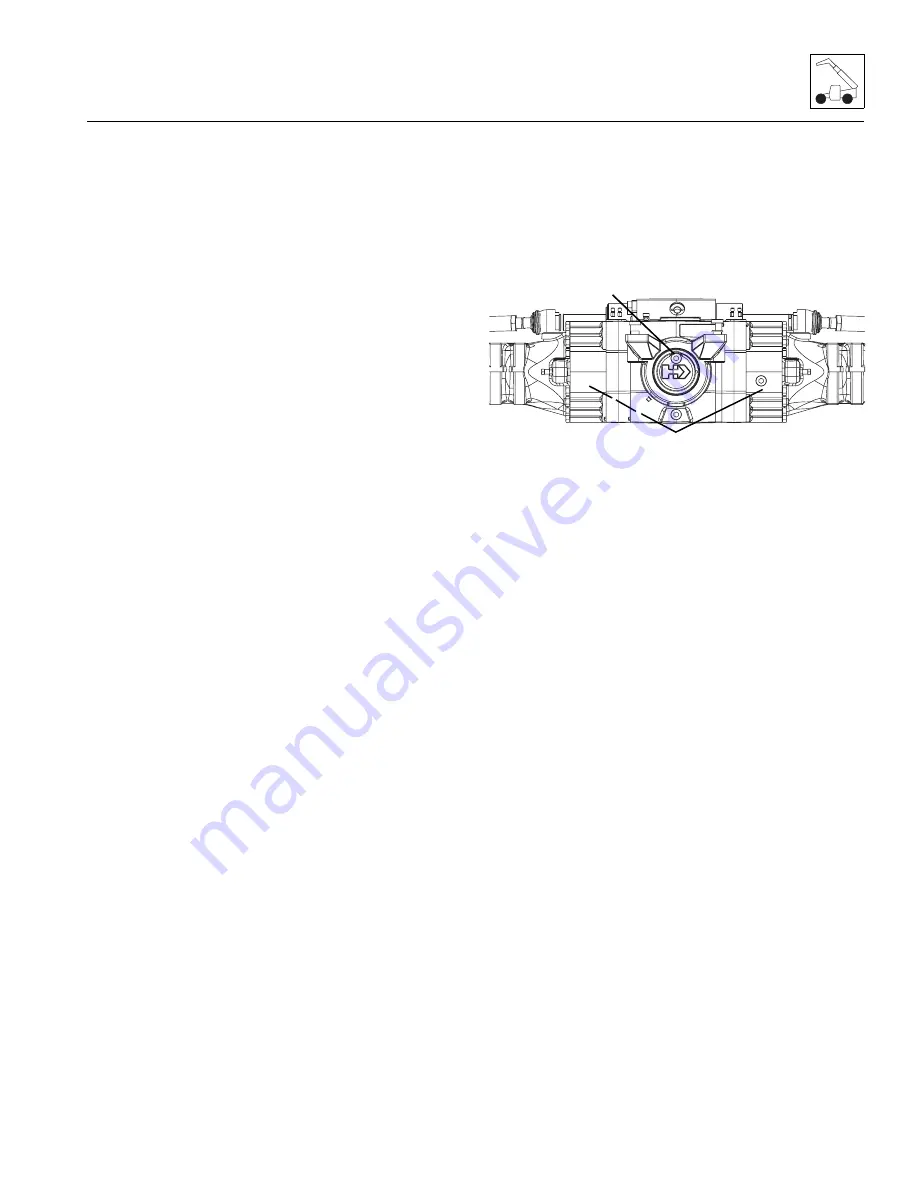
5.5
3507, 3508, 3509, 3512, 3513, 4007, 4008, 4009, 4012, 4013
Axles, Drive Shafts, Wheels and Tires
c. Axle Installation
The front and rear axle assemblies differ in that the front
axle assembly is equipped with a parking brake
mechanism and limited-slip feature; the rear axle has
neither. The steps below outline a typical axle installation
procedure, suitable for either the front or the rear axle
assembly.
1. Before proceeding, ensure that the machine will
remain in place during axle installation. Block the
front and rear of both tires on the axle that is already
installed on the machine.
2. If applicable, raise the machine using a suitable jack
or hoist. Place suitable supports beneath the frame
and lower the machine onto the supports, allowing
enough room for axle installation. Ensure that the
machine will remain in place during axle installation.
3. Using a suitable jack, hoist or overhead crane and
sling, remove the axle from its support or holding
stand. Balance the axle and prevent it from tipping,
turning or falling while positioning it beneath the
machine.
DO NOT
raise or otherwise disturb the
machine while installing the axle. Keep the axle
supported and balanced on the jack, hoist or
overhead crane and sling throughout the installation
procedure.
4. Position the axle under the frame, and align the axle
housing with the holes in the frame.
5. Install the axle bolts and nuts. Tighten and torque
the axle nuts near the pivoting bearings to 650 Nm
(479 lb-ft) and the bolts in the front axle cylinder
anchor plate to 550 Nm (405 lb-ft). On fixed axle
machines before S/N 1160000798, tighten and
torque the axle front axle nuts to 650 Nm (479 lb-ft)
and the rear nuts to 550 Nm (405 lb-ft).
6. Move the cylinder into position on the axle cylinder
anchor. Insert a cylinder-mount pin through the
cylinder and cylinder anchor (not necessary on fixed
axle machines before S/N 1160000798). Secure the
cylinder-mount pin.
7. Apply a multi-purpose grease through the self-
tapping lube fitting to lubricate the self-align bearing
and the cylinder-mount pin.
8. Install the drive shaft assemblies. (Refer to Section
5.4.5, “Drive Shaft Installation.”)
9. If reinstalling an axle previously removed from the
machine, position the driveshaft yoke on the axle
according to the alignment marks made earlier. If
installing a new axle, note the position of the
driveshaft yoke at the transmission. Align the
driveshaft yoke on the axle in the same plane as the
yoke on the transmission.
10. Tighten the axle oil drain plug, loosen and remove
the axle oil fill plug (
3
). Fill the axle through the axle
fill plug until the oil level is even with the oil check
level plugs (
4
). Refer to Section 2.4, “Fluids,
Lubricants and Capacities,” for proper oil and
capacities.
11. Rotate wheel hubs 90 degrees so the drain plug
becomes the fill plug. Refer to Section 2.4, “Fluids,
Lubricants and Capacities,” for proper oil and
capacities.
12. Install the wheel and tire assemblies. Refer to
Section 5.5.2, “Installing Wheel and Tire Assembly
onto Machine.”
Note:
Be sure the directional tread pattern "arrows" of
the tires are facing in the direction of forward travel.
13. Carefully remove the jack, hoist or overhead crane
and sling supporting the axle.
14. Carefully raise the machine using a suitable jack or
hoist. Remove the supports from beneath the frame
and lower the machine to the ground.
Note:
ALWAYS use new o-rings when servicing the
machine.
15. Install new o-rings into the fittings. Lubricate the
o-rings with clean hydraulic oil.
16. Uncap and connect the steering and brake lines at
their axle fittings.
17. Install the park brake on the front axle.
18. Bleed brakes as necessary. Refer to Section 8.8.3,
“Brake Test.”
19. Check the hydraulic reservoir oil level.
20. Unblock the wheels.
21. Start the engine. Turn the steering wheel several
times lock to lock, operate the frame tilt function
several times in both directions and check the
function of the brakes. Check for hydraulic leaks, and
tighten or repair as necessary.
22. Close and secure the engine cover.
MZ1030
4
3