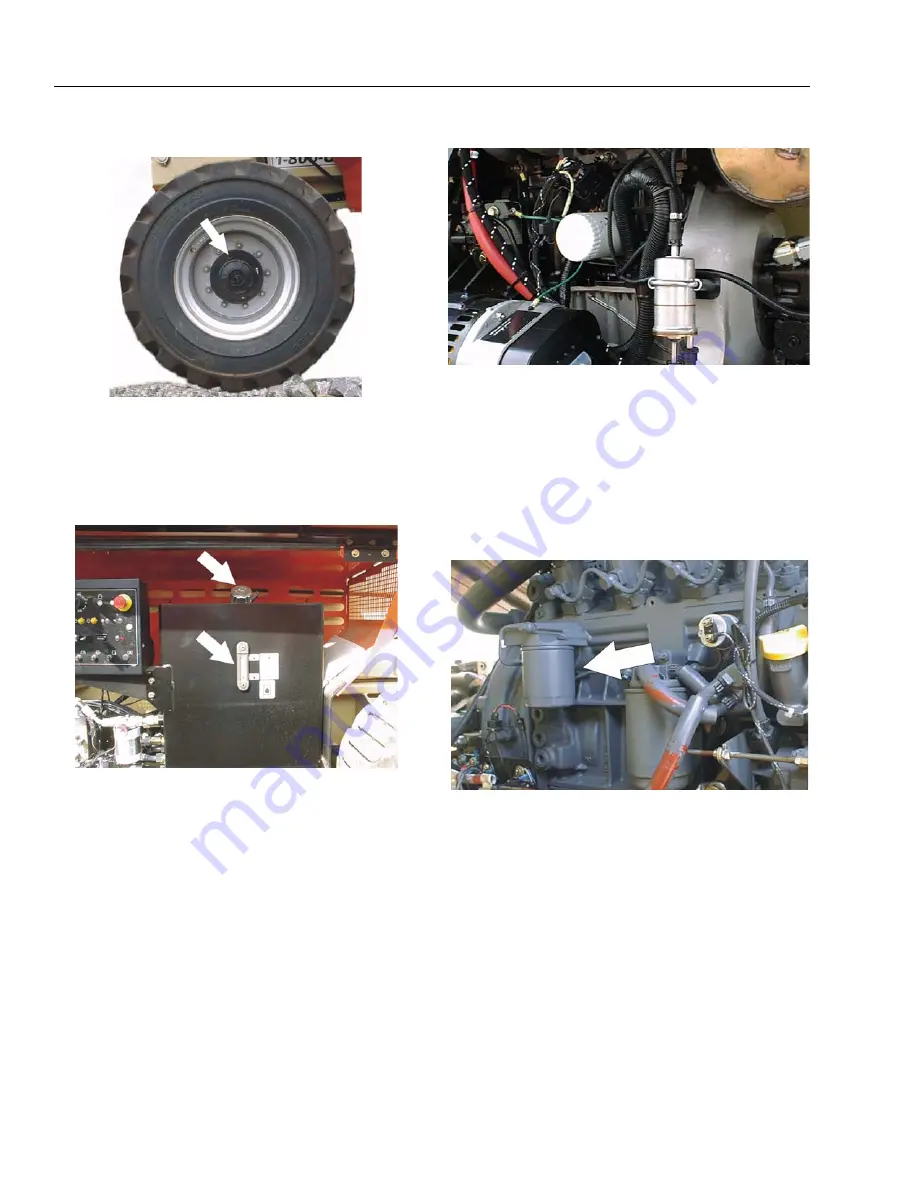
SECTION 1 - SPECIFICATIONS
1-6
– JLG Sizzor –
3121133
2.
Drive Hub
• Lube Points - Fill Plugs (4)
• Lube - EPGL
• Interval - Every 2 years or 1200 hours
3.
Hydraulic Oil
• Lube Point - Fill Cap/Fill Level
• Lube - HO
• Interval - Check oil every 10 hours of operation;
change oil every 2 years or 1200 hours of operation.
4.
Sliding Wear Pads
• Lube Points - 8 Sliding Wear Pads
• Lube - MPG
• Interval - Every month or 50 hours.
5.
Oil Change w/Filter - Ford
• Lube Point(s) - Fill Cap/Spin-on Element
(JLG P/N 7014501)
• Capacity - 4.5 qt. (4.25 L)
• Lube - EO
• Interval - 3 Months or 150 hours of operation
• Comments - Check level daily/Change in accordance
with engine manual.
6.
Oil Change w/Filter - Deutz
• Lube Point(s) - Fill Cap/Spin-on Element
(JLG P/N 7016331)
• Capacity - 6.3 qt. (5.9 L) engine only
• Lube - EO
• Interval - Every Year or 600 hours of operation
• Comments - Check level daily/Change in accordance
with engine manual.
Property of American Airlines