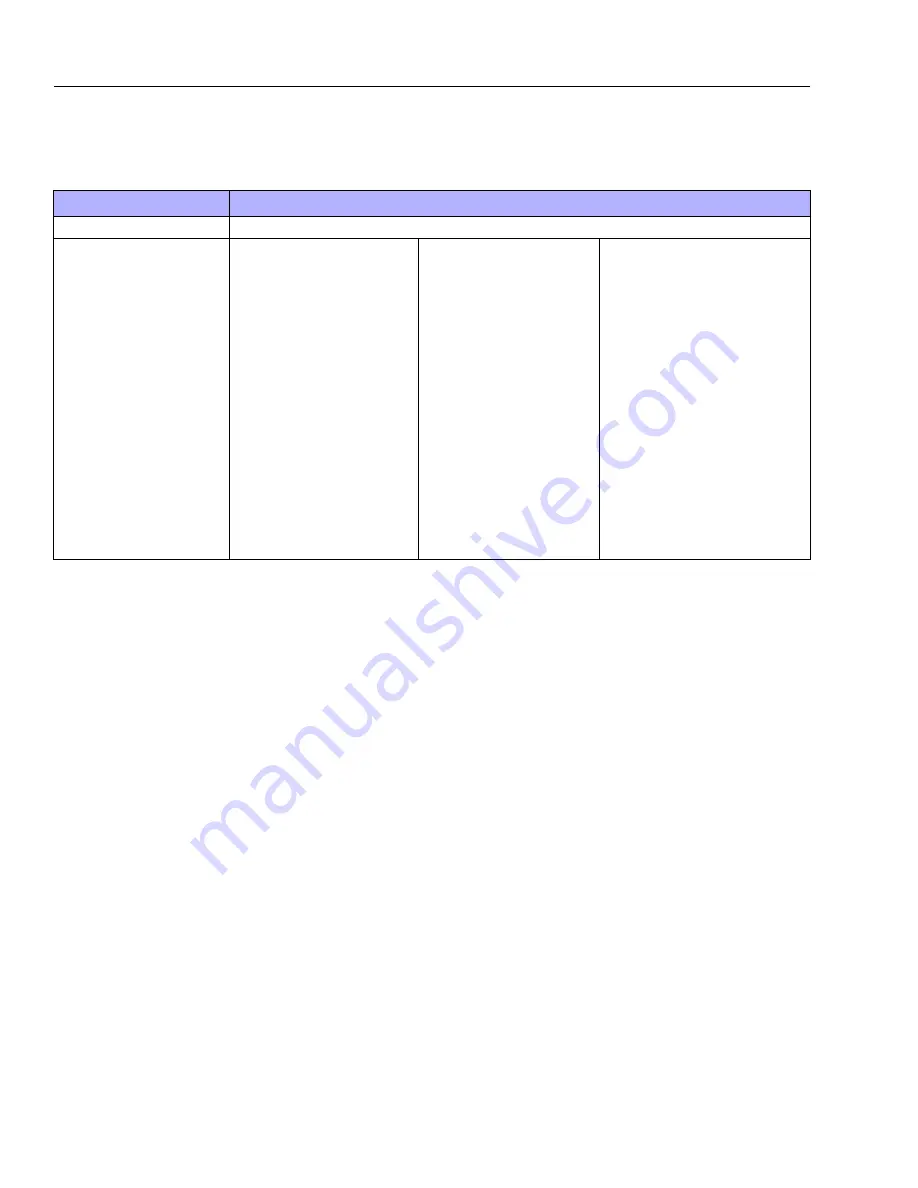
SECTION 1 - SPECIFICATIONS
1-4
3121788
Electrical System
Table 1-5. Battery Charger Specifications
DESCRIPTION
2632R/3246R
Electrical System Voltage (DC)
24V
Battery Charger:
Input:
AC Input Voltage:
Nominal AC Input Voltage:
Input Frequency:
Max. AC Input Current:
Ingress Protection:
Operating Temperature:
Output:
Nominal DC Output Voltage:
Max. DC Output Voltage:
Max DC Output Current:
Max. Interlock Current:
Protection:
Output Reverse Polarity:
Output Short Circuit:
AC Overload:
DC Overload:
Delta-Q
85-270V AC
100VAC / 240VAC RMS
50 - 60Hz
7.5A
IP66 NEMA4 Type 4
-40°F (-40°C) to 149°F (+65°C)
24V
36V
27.1A
1A @ 24V
Electronic Protection - Auto Reset
Current Limited
Current Limited
Current Limited
PRO - Eagle Performance Series
108-132V AC
120VAC RMS
45 - 65Hz
12A
IP35
-22°F (-30°C) to 122°F (+50°C)
24V
31.92V
25A
1A @ 24V
Electronic Protection-Auto Reset
Electronic Protection-Auto Reset
Branch Circuit Protection
Current Limited
Green Power - Pylon International
100 -240V AC
— —
45 - 65Hz
8.5A
IP66
-4°F (-20°C) to 122°F (+50°C)
24V
34V
30A
1A @ 24V
Electronic Protection-Auto Reset
Electronic Protection-Auto Reset
Current Limited
Current Limited
Go to
Discount-Equipment.com
to
order your
parts