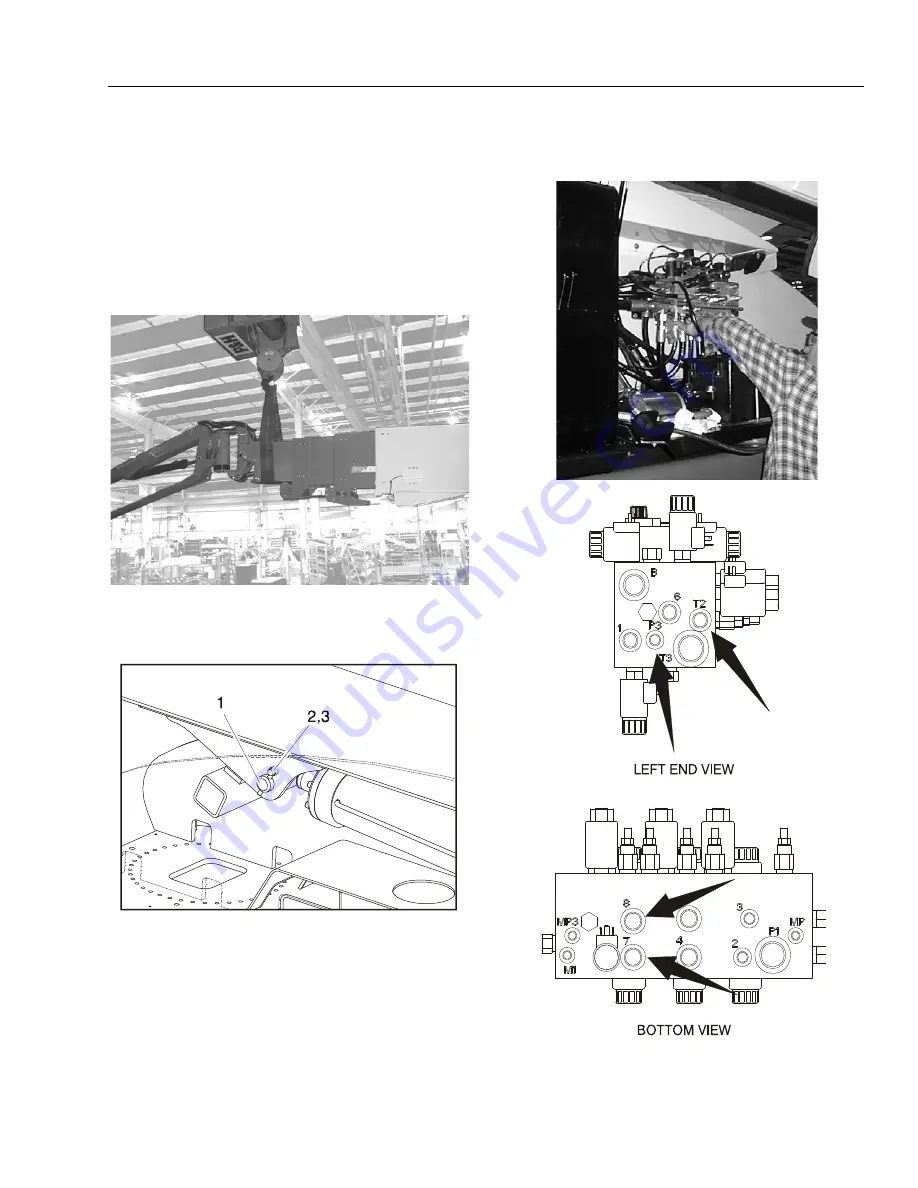
SECTION 4 - BOOM & PLATFORM
3121142
– JLG Lift –
4-7
4.2
BOOM REMOVAL, DISASSEMBLY/ASSEMBLY, &
CABLE REPLACEMENT
Removal
1.
Place machine on firm, level ground.
2.
Slightly elevate the boom and support the fly boom
with a crane or an adequate lifting device capable of
handling 6 - 7 tons.
3.
Place blocking under lift cylinder to hold it in place.
4.
Remove lift cylinder pin securing the lift cylinder rod to
the boom.
5.
Remove the boom end cover.
6.
Tag and disconnect the telescope, tank, and pressure
hoses as indicated below from the main valve and cap
ends.
1.
Pivot Pin
2.
Bolt
3.
Keeper Pin
Summary of Contents for 1200SJP
Page 1: ...Service and Maintenance Manual Models 1200SJP 1350SJP P N 3121142 November 8 2016 AS NZS...
Page 2: ......
Page 20: ...xiv JLG Lift 3121142 LIST OF TABLES TABLE NO TITLE PAGE NO This page left blank intentionally...
Page 51: ...SECTION 3 CHASSIS TURNTABLE 3121142 JLG Lift 3 5 This page left blank intentionally...
Page 58: ...SECTION 3 CHASSIS TURNTABLE 3 12 JLG Lift 3121142 Figure 3 11 Axle Loctite Application...
Page 64: ...SECTION 3 CHASSIS TURNTABLE 3 18 JLG Lift 3121142 Figure 3 13 Drive Hub Sheet 1 of 2...
Page 173: ...SECTION 3 CHASSIS TURNTABLE 3121142 JLG Lift 3 127 Figure 3 75 EMR2 Fault Codes Sheet 1 of 5...
Page 174: ...SECTION 3 CHASSIS TURNTABLE 3 128 JLG Lift 3121142 Figure 3 76 EMR2 Fault Codes Sheet 2 of 5...
Page 175: ...SECTION 3 CHASSIS TURNTABLE 3121142 JLG Lift 3 129 Figure 3 77 EMR2 Fault Codes Sheet 3 of 5...
Page 176: ...SECTION 3 CHASSIS TURNTABLE 3 130 JLG Lift 3121142 Figure 3 78 EMR2 Fault Codes Sheet 4 of 5...
Page 177: ...SECTION 3 CHASSIS TURNTABLE 3121142 JLG Lift 3 131 Figure 3 79 EMR2 Fault Codes Sheet 5 of 5...
Page 189: ...SECTION 3 CHASSIS TURNTABLE 3121142 JLG Lift 3 143...
Page 191: ...SECTION 3 CHASSIS TURNTABLE 3121142 JLG Lift 3 145...
Page 193: ...SECTION 3 CHASSIS TURNTABLE 3121142 JLG Lift 3 147...
Page 203: ...SECTION 3 CHASSIS TURNTABLE 3121142 JLG Lift 3 157...
Page 205: ...SECTION 3 CHASSIS TURNTABLE 3121142 JLG Lift 3 159...
Page 207: ...SECTION 3 CHASSIS TURNTABLE 3121142 JLG Lift 3 161...
Page 209: ...SECTION 3 CHASSIS TURNTABLE 3121142 JLG Lift 3 163...
Page 211: ...SECTION 3 CHASSIS TURNTABLE 3121142 JLG Lift 3 165...
Page 227: ...SECTION 3 CHASSIS TURNTABLE 3121142 JLG Lift 3 181...
Page 231: ...SECTION 3 CHASSIS TURNTABLE 3121142 JLG Lift 3 185...
Page 248: ...SECTION 4 BOOM PLATFORM 4 14 JLG Lift 3121142 Figure 4 7 Boom Assembly Sheet 7 of 7...
Page 305: ...SECTION 4 BOOM PLATFORM 3121142 JLG Lift 4 71 Figure 4 31 Outer Mid Boom Extend Retract Cables...
Page 306: ...SECTION 4 BOOM PLATFORM 4 72 JLG Lift 3121142 Figure 4 32 Fly Boom Extend Retract Cables...
Page 323: ...SECTION 4 BOOM PLATFORM 3121142 JLG Lift 4 89 Figure 4 37 Rotator Counterbalance Valve...
Page 352: ...SECTION 5 HYDRAULICS 5 28 JLG Lift 3121142 Figure 5 28 Steer Pressure Adjustments...
Page 379: ...SECTION 6 JLG CONTROL SYSTEM 3121142 JLG Lift 6 3 Figure 6 2 Control System Block Diagram...
Page 388: ...SECTION 6 JLG CONTROL SYSTEM 6 12 JLG Lift 3121142 Figure 6 10 Control Module Location...
Page 457: ...SECTION 6 JLG CONTROL SYSTEM 3121142 JLG Lift 6 81 Figure 6 24 Fault Code Light Location...
Page 490: ...SECTION 6 JLG CONTROL SYSTEM 6 114 JLG Lift 3121142 Figure 6 31 CANbus Circuit...
Page 508: ...SECTION 6 JLG CONTROL SYSTEM 6 132 JLG Lift 3121142 Figure 6 32 Moment Chart...
Page 553: ......