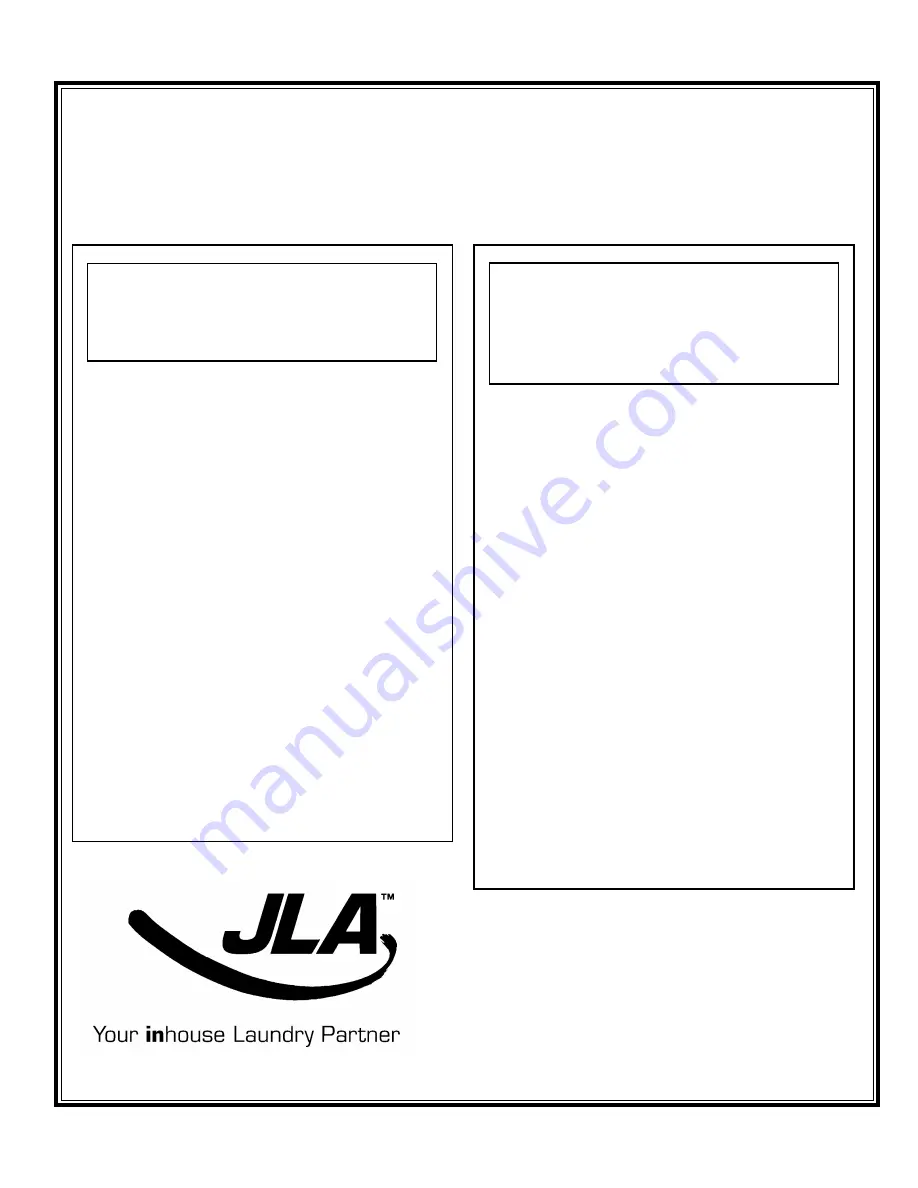
D90 Installation Manual
Phase 7 Gas (DSI / HSI) Non-Coin
Part No. 113374-4
WARNING: For your safety the information in
this manual must be followed to minimize the risk
of fire or explosion or to prevent property
damage, personal injury or death.
— Do not store or use gasoline or other flammable
vapors and liquids in the vicinity of this or any
other appliance.
— WHAT TO DO IF YOU SMELL GAS:
•
Do not try to light any appliance.
•
Do not touch any electrical switch; do not
use any phone in your building.
•
Clear the room, building or area of all
occupants.
•
Immediately call your gas supplier from a
neighbor’s phone. Follow the gas supplier’s
instructions.
•
If you cannot reach your gas supplier, call
the fire department.
— Installation and service must be performed by a
qualified installer, service agency or the gas
supplier.
AVERTISSEMENT: Assurez-vous de bien
suivre les instructions données dans cette notice
pour réduire au minimum le risque d’incendie
ou d’explosion ou pour éviter tout dommage
matériel, toute blessure ou la mort.
— Ne pas entreposer ni utiliser d’essence ni
d’autres vapeurs ou liquides inflammables à
proximité de cet appareil ou de tout autre
appareil.
— QUE FAIRE SI VOUS SENTEZ UNE ODEUR
DE GAZ:
•
Ne pas tenter d’allumer d’appareils.
•
Ne touchez à aucun interrupteur. Ne pas
vous servir des téléphones se trouvant dans
le bâtiment.
•
Évacuez la pièce, le bâtiment ou la zone.
•
Appelez immédiatement votre fournisseur
de gaz depuis un voisin. Suivez les
instructions du fournisseur.
•
Si vous ne pouvez rejoindre le fournisseur
de gaz, appelez le service des incendies.
— L’installation et l’entretien doivent être assurés
par un installateur ou un service d’entretien qualifié
ou par le fournisseur de gaz.
JLA Limited
Meadowcroft Lane, Halifax Road
Ripponden
West Yorkshire, England
HX6 4AJ
Telephone: 01422 822282 / Fax: 01422 824390
Summary of Contents for D90
Page 40: ...JLA113374 4 10 02 07 5 ...