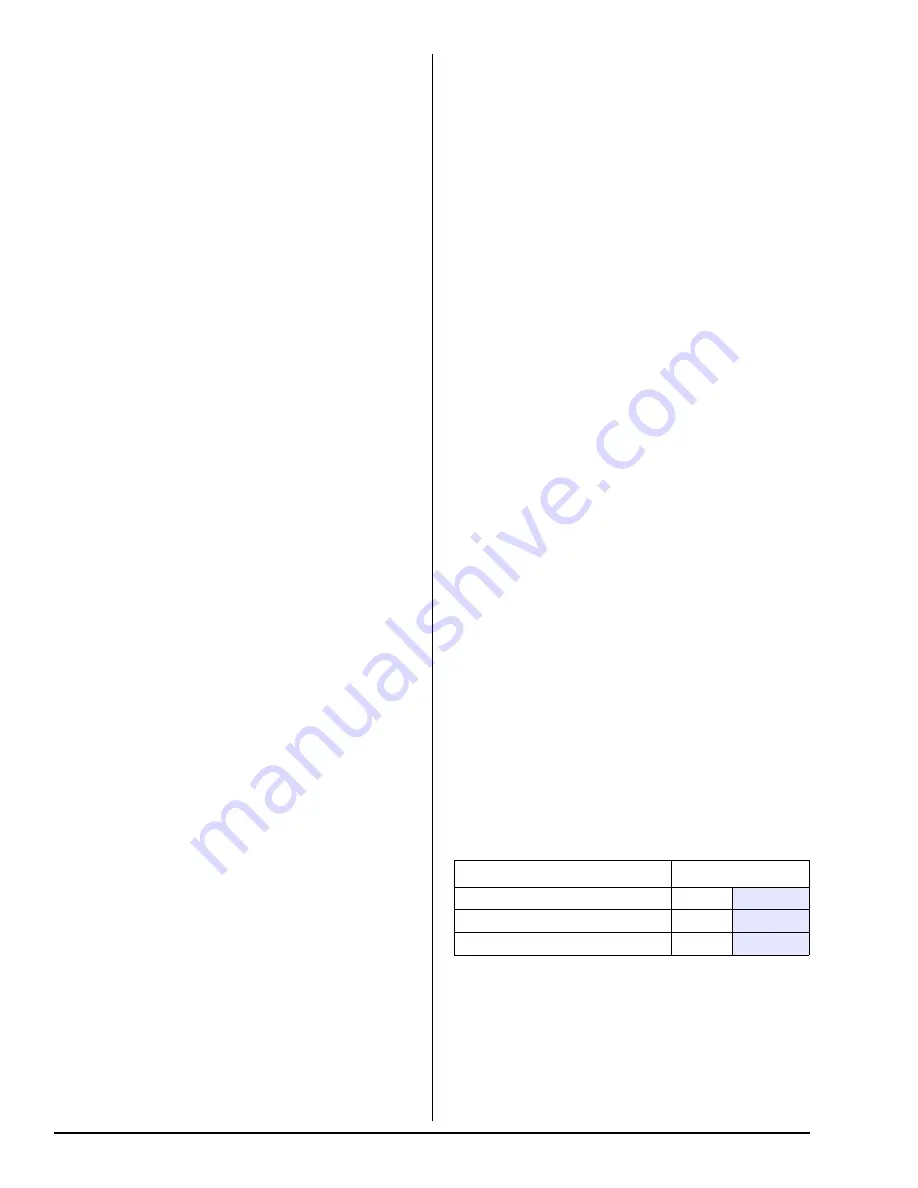
18
JLA Limited
113375 - 16
Compressed Air Supply
Air Pressure
Normal
80 psi
5.51 bar
Minimum Supply
70 psi
4.82 bar
Maximum Supply
90 psi
6.21 bar
Check to ensure that the tumbler starts in the clockwise
direction. Additionally, check the direction of the motorized
impellor to ensure that the motorized impellor rotates in the
clockwise direction as viewed from the front. If it is, the
phasing is correct. If the phasing is incorrect, reverse two
of the leads at L1, L2, or L3 of the power supply connections
made to the dryer.
IMPORTANT: Motorized impellor as viewed from the front
must turn in the clockwise direction, otherwise the dryer
efficiency will be drastically reduced and premature
component failure can result.
Heat Circuit Operational Test
Gas Models
When the dryer is first started (during initial start-up), the
burner has a tendency not to ignite on the first attempt. This
is because the gas supply piping is filled with air, so it may
take a few minutes for this air to be purged from the lines.
The dryer is equipped with a DSI system, which has internal
diagnostics. If ignition is not established after three attempts,
the heat circuit DSI module will LOCKOUT until it is manually
reset. To reset the DSI system, open and close the main
door and restart the dryer (press the “START” key).
NOTE: During the purging period, check to be sure that
all gas shutoff valves are open.
Once ignition is established, a gas pressure test should be
taken at the gas valve pressure tap of each dryer to assure
that the water column pressure is correct and consistent.
NOTE: The water column pressure requirements
(measured at the gas valve pressure tap)…
Natural Gas ............. 3.5 in WC (8.7 mb)
L.P. Gas .................. 10.5 in WC (26.1 mb)
IMPORTANT: There is no regulator provided in an L.P.
dryer. The water column pressure must be regulated at
the source (L.P. tank) or an external regulator must be
added to each dryer.
Steam Models
Check to ensure that the (standard) steam damper or
(optional) steam solenoid valve is functioning properly
The steam damper should not “slam” (open or closed) when
it reaches the end of (piston) travel. Additionally, the steam
damper should not bind and/or stop during travel. If either
of these conditions occur, the flow control must be adjusted.
Refer to the bottom illustration on the previous page for air
adjustment instructions.
Make a complete operational check of all safety-related
circuits (i.e., lint drawer switch and sail switch on gas
models).
NOTE: To check for proper sail switch operation, open the
main door and while holding main door switch plunger in,
start the dryer. The dryer should start but the heat circuit
should not be activated (on). If the heat (burner) does
activate, shut the dryer off and make the necessary
adjustments.
Reversing tumbler dryers should never be operated with less
than a 79 lb (35.83 kg) load (dry weight), since the load’s
weight affects tumbler coast time during a direction reversal
command. It is important that the tumbler come to a
complete stop prior to starting in opposite direction.
Microprocessor Controller (Computer)
Dryer Models
Spin and stop times are not adjustable in the Automatic Mode
and have been preprogrammed into the microprocessor
controller (computer) for 150-seconds spin time in the
forward direction and 120-seconds in the reverse direction
with a 5-second dwell (stop) time.
Spin and stop times are adjustable in the Manual (timed)
Mode.
Tumbler Coating
The tumbler is treated with a protective coating. We suggest
dampening old garments or cloth material with a solution of
water and nonflammable mild detergent and tumbling them
in the tumbler to remove this coating.
Each dryer should be operated through one complete cycle
to assure that no further adjustments are necessary and
that all components are functioning properly.
Make a complete operational check of all operating
controls…
Microprocessor controller (computer)
programs / selections…
Each computer has been preprogrammed by the factory with
the most commonly used parameter (program) selections.
If computer program changes are required, refer to the
computer programming manual, which was shipped with the
dryer.
Compressed Air Requirements _______
The dryer requires an external supply of compressed air
(2.50 cfh at 80 psi [0.07 cmh at 5.51 bar] for gas models
and 3.25 cfh at 80 psi [0.09 cmh at 5.51 bar] for steam
models). For steam models, compressed air is necessary
for the standard air operated steam damper. On both the
steam models as well as the gas models, compressed air is
necessary/required for blower air jet operation to clean lint
from the impellor/fan (squirrel cage).
Air Requirements
Microprocessor Controller (Computer) Dryers…
Shaded areas are stated in metric equivalents
Air Regulation
No air regulation or air filtration is provided with the dryer.
External regulation/filtration of 80 psi (5.51 bar) must be
provided. It is suggested that a filter/regulator/gauge
arrangement be added to the compressed air line just before
the dryer connection. This is necessary to ensure that correct
and clean air pressure is achieved.
Summary of Contents for D120
Page 24: ...Part No 113375 16 12 01 15 ...