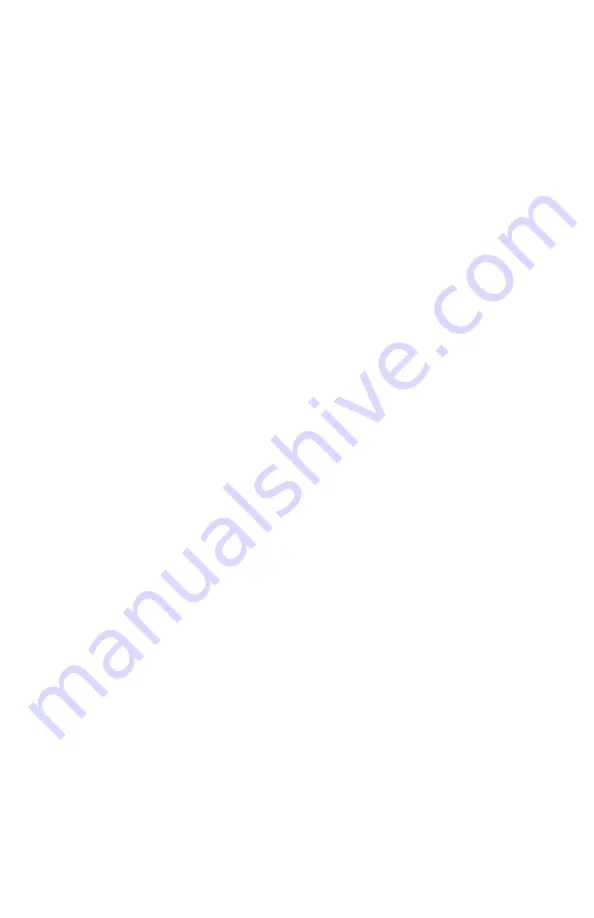
34
PI-178
July 2020
Warranty
Limited Warranty.
Each Waterblast Unit, Bareshaft Pump, and Fluid
End manufactured by Jetstream is warranted against defects in material
and workmanship for a period of 12 months or 1,000 hours, provided it
is used in a normal and reasonable manner and in accordance with all
operating instructions. If sold to an end user, the applicable warranty
period commences from the date of delivery to the end user. If used for
rental purposes, the applicable warranty period commences from the
date of delivery to the party holding the equipment available for rent. This
limited warranty may be enforced by any subsequent transferee during
the warranty period. This limited warranty is the sole and exclusive war-
ranty given by Jetstream.
Exclusive Remedy.
Should any warranted product fail during the
warranty period, Jetstream will cause to be repaired or replaced, as
Jetstream may elect, any part or parts of such Waterblast Unit, Bareshaft
Pump, or Fluid End that the examination discloses in Jetstream’s sole
judgment to be defective in material or factory workmanship. Repairs
or replacements are to be made at Jetstream in Houston, Jetstream FS
Solutions Rental Center, the customer’s location, or at other locations
approved by Jetstream. Labor is furnished only when the unit or part
is returned to the factory or when travel and expenses are paid by the
purchaser. Freight, travel and expenses incurred in connection with repair
or warranty are excluded from this warranty and shall be paid by the pur-
chaser. The foregoing remedies shall be the sole and exclusive remedies
of any party making a valid warranty claim.
The Jetstream Limited Warranty shall NOT apply to (and Jetstream shall
NOT be responsible for):
1. Major components or trade accessories that have a separate warranty
from their original manufacturer, such as, but not limited to: diesel en-
gines, electric motors, electronic soft starter and/or across the line starter
panels, axles, PTO’s, clutch packs, high pressure gauges, high pressure
hoses, flex lances, etc.
2. Normal adjustments and maintenance services.
3. Normal wear parts such as, but not limited to: oil, clutches, belts,
filters, packing, cartridges, univalves, face seals, diffusers, gland nut
bushings, plungers, nozzles, rupture disks, etc.