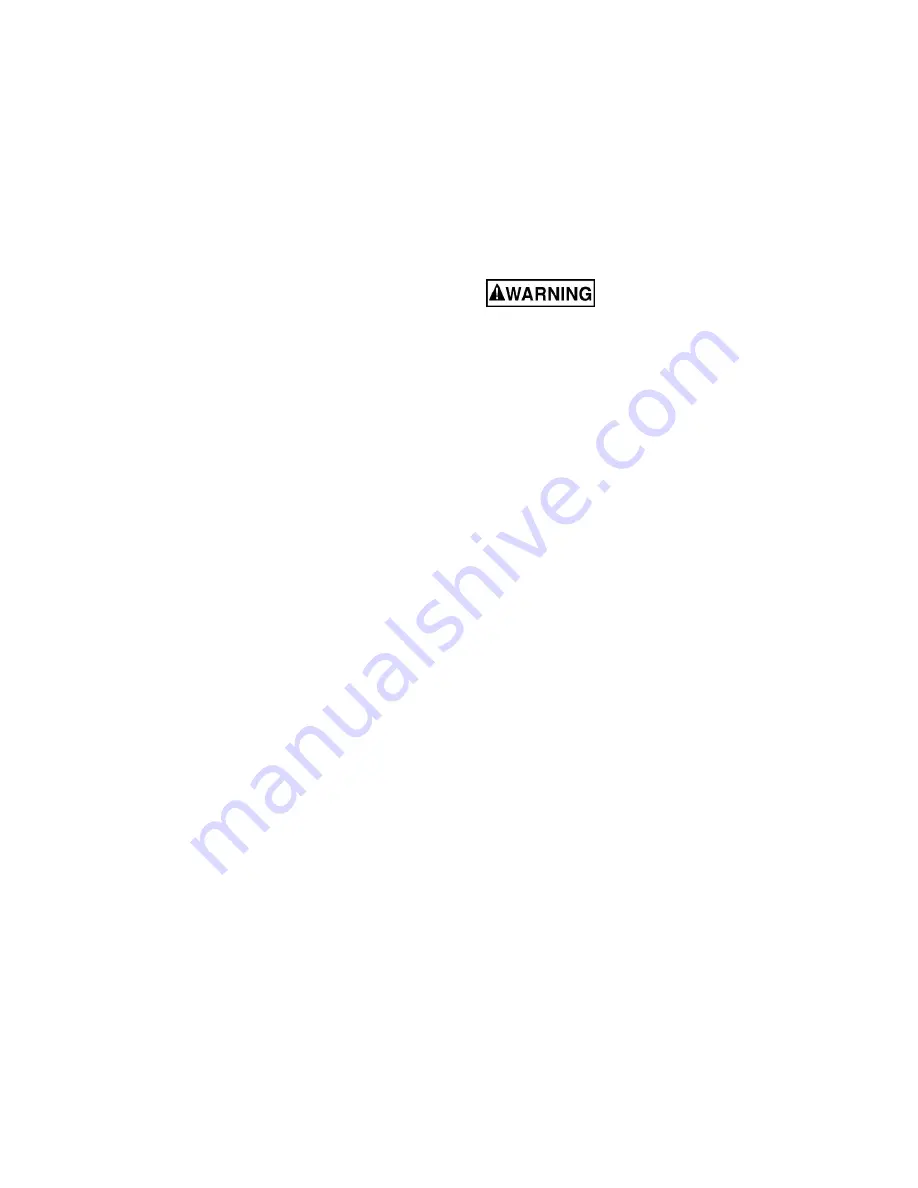
9
6. Adjust exit fence as follows: Run a test piece
through and stop machine when workpiece has
reached end of exit table but is still pinched
between the rolls. Move fence into position just
flush or slightly clear of workpiece edge. Exit
fence must not bear against workpiece. Tighten
down fence.
7. Start machine and feed workpiece.
8.0
Adjustments
8.1
Hold-downs
Refer to Figure 7-1.
Adjustment can be made to accommodate
variations in material thickness and hardness. The
hold-down
bolts
are adjusted for Pittsburgh lock set;
the hold-down
studs
are adjusted for optional roll
sets. These fasteners set the tension for top and
bottom plates to move, allowing material to slide
between them.
Only adjust hold-downs if there is
a problem feeding the material.
If material slips,
tends to leave the guide fence, or curls up at exit,
adjust as follows:
1. Disconnect machine from power source.
2. Remove top cover.
3. Tighten hold-down bolts (or studs) until snug,
then loosen them a quarter turn. This will
usually give proper adjustment for all material
thicknesses.
4. Reinstall top cover and run a test piece through
machine:
If material slips, tighten both hold-down
bolts (or studs) equally until problem is
resolved. If it slips as it leaves the rolls,
tighten hold-down bolt on exit side. If
material starts working away from entry
fence, tighten hold-down bolt on entry side.
If material curls up after leaving forming
head, or shows extremely heavy pressure
marks, loosen hold-down bolts (or studs)
slightly.
5. After adjustments, lock setting of the bolts by
tightening side screw (X, Figure 7-1). Lock
setting of studs by tightening top nuts.
9.0
User-maintenance
Before doing maintenance on
the machine, disconnect it from the electrical
supply by pulling out the plug or switching off
the main switch. Failure to comply may cause
serious injury.
9.1
Cleaning and lubrication
Insert oil every 4 hours of operation into the six oil
fittings at back of machine. These lubricate the main
bearings. Recommended oil is Mobil DTE Oil
Light
TM
, or equivalent.
Apply a multi-purpose lithium grease to the drive
gears after approximately 40 hours of operation, or
as needed.
Keep forming rolls and table surface clean and free
of deposits.
9.2
Additional servicing
Any additional servicing should be performed by an
authorized service technician.
10.0
Replacement Parts
Replacement parts are listed on the following pages. To order parts or reach our service department, call 1-800-
274-6848 Monday through Friday, 8:00 a.m. to 5:00 p.m. CST. Having the Model Number and Serial Number of
your machine available when you call will allow us to serve you quickly and accurately.
Non-proprietary parts, such as fasteners, can be found at local hardware stores, or may be ordered from JET.
Some parts are shown for reference only, and may not be available individually.
Summary of Contents for LF-20
Page 10: ...10 10 1 1 LF 20 Lockformer Exploded View ...
Page 12: ...12 10 2 1 LF 20 Upper Bracket Exploded View ...
Page 14: ...14 10 3 1 LF 20 Lower Bracket Exploded View ...
Page 17: ...17 11 0 Electrical Connections for LF 20 ...
Page 19: ...19 This page intentionally left blank ...
Page 20: ...20 427 New Sanford Road LaVergne Tennessee 37086 Phone 800 274 6848 www jettools com ...