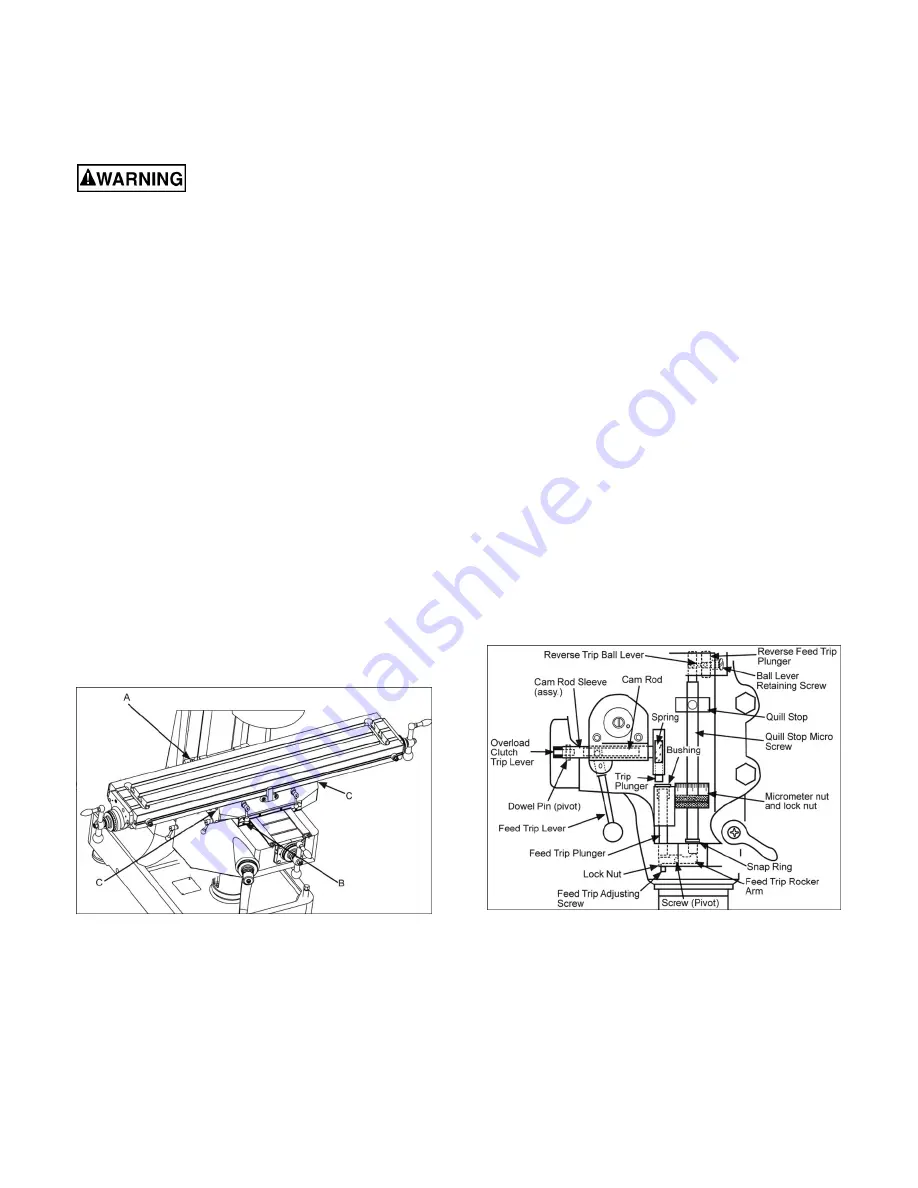
19
2. Turn ram pinion (B, Figure 19) with a wrench to slide
ram on its ways.
3. When desired position is reached, tighten handles
(A, Figure 19)[or hex nuts] securely.
10.3.2
Positioning ram on turret
Make sure machine base is secured
to floor before repositioning ram. The center of
gravity can shift enough to cause machine to tip over,
resulting in serious injury to operator and damage to
machine.
1. Loosen four turret lock bolts (C, Figure 19) that clamp
the ram to the top of the base. 1/2 turn should be
sufficient to allow turret to move.
Note:
Use gentle hand pressure to avoid rapid
movement.
2. Turn ram until spindle is in desired position. Use
scale on turret for degree measurement.
3. Tighten four turret lock bolts (C, Figure 19). Tighten
in two steps using a calibrated torque wrench. Use a
crossing pattern to tighten the nuts. Tighten initially
to 25 foot-pounds, then tighten to a final torque of 50
foot-pounds.
10.4
Gib adjustment
The table, saddle and knee are equipped with adjustable
gibs. The gibs may require adjustment if unusual
vibration is noted when the locking mechanisms are off,
or if you experience unusual vibration when spindle
speed, tooth pitch or depth of cut do not account for the
vibration.
NOTE: When adjusting gibs, always start with knee first;
adjust saddle second, and adjust table last.
Figure 20
10.4.1
Knee gib adjustment
The knee gib adjustment screw (A, Figure 20) is located
under the chip wiper at rear of knee where it contacts the
column. Remove way cover and wiper to expose gib
adjustment screw. Tighten screw until a slight drag is felt
when turning knee crank.
10.4.2
Saddle gib adjustment
The saddle gib adjustment screw is on left front of saddle
(B, Figure 20). Tighten screw until a slight drag is felt
when turning cross-feed crank.
10.4.3
Table gib adjustment
The table gib adjustment screw (C, Figure 20) is on left-
hand side, beneath table. Tighten screw until a slight drag
is felt when turning longitudinal table cranks.
10.5
Power feed trip lever mechanism
Refer to Figure 21.
The power feed trip lever mechanism will require
adjustment if worn or whenever any trip lever mechanism
components are replaced.
1. Loosen feed trip adjusting screw lock nut.
2. Loosen adjusting screw until it is loose in the lever
and no longer contacts bottom of feed trip plunger.
3. Using the coarse feed handle, move quill to bottom
of its travel so that quill stop contacts micrometer nut.
Hold the quill on the stop.
4. Pull feed handle out to engage power feed system.
5. Turn feed trip adjusting screw until power feed
disengages.
6. Tighten feed trip adjusting screw.
7. Release quill stop so you can engage power feed
mechanism using power feed trip lever.
8. Using the coarse feed handle, pull quill stop back into
firm contact with micrometer nut.
Figure 21
Note:
The power feed should disengage when the
quill stop pushes on the micrometer nut. If it does
not disengage, repeat the adjustment steps above.
9. Engage power feed and move quill stop to top of its
travel. Make sure that reverse trip mechanism also
disengages power feed. If it does not, readjust the
mechanism until positive disengagement occurs
when quill is at top of its stroke.
Summary of Contents for JTM-949EVS4
Page 13: ...13 9 3 Control positions for milling and drilling operations Table 3...
Page 23: ...23 13 1 1 JTM 949EVS JTM 1050EVS Upper Head Assembly Exploded View...
Page 26: ...26 13 2 1 JTM 949EVS JTM 1050EVS Lower Head Assembly Exploded View...
Page 30: ...30 13 3 1 JTM 949EVS Base Machine Exploded View...
Page 33: ...33 13 4 1 JTM 1050EVS Base Machine Exploded View...
Page 36: ...36 13 5 1 JTM 949EVS Table Assembly Exploded View...
Page 38: ...38 13 6 1 JTM 1050EVS Table Assembly Exploded View...
Page 46: ...46 14 0 Electrical Connections 14 1 JTM 949EVS 230 and JTM 1050EVS2 230V ONLY...
Page 47: ...47 14 1 JTM 949EVS4 and JTM 1050EVS4 460V ONLY...
Page 48: ...48 427 New Sanford Road LaVergne Tennessee 37086 Phone 800 274 6848 www jettools com...