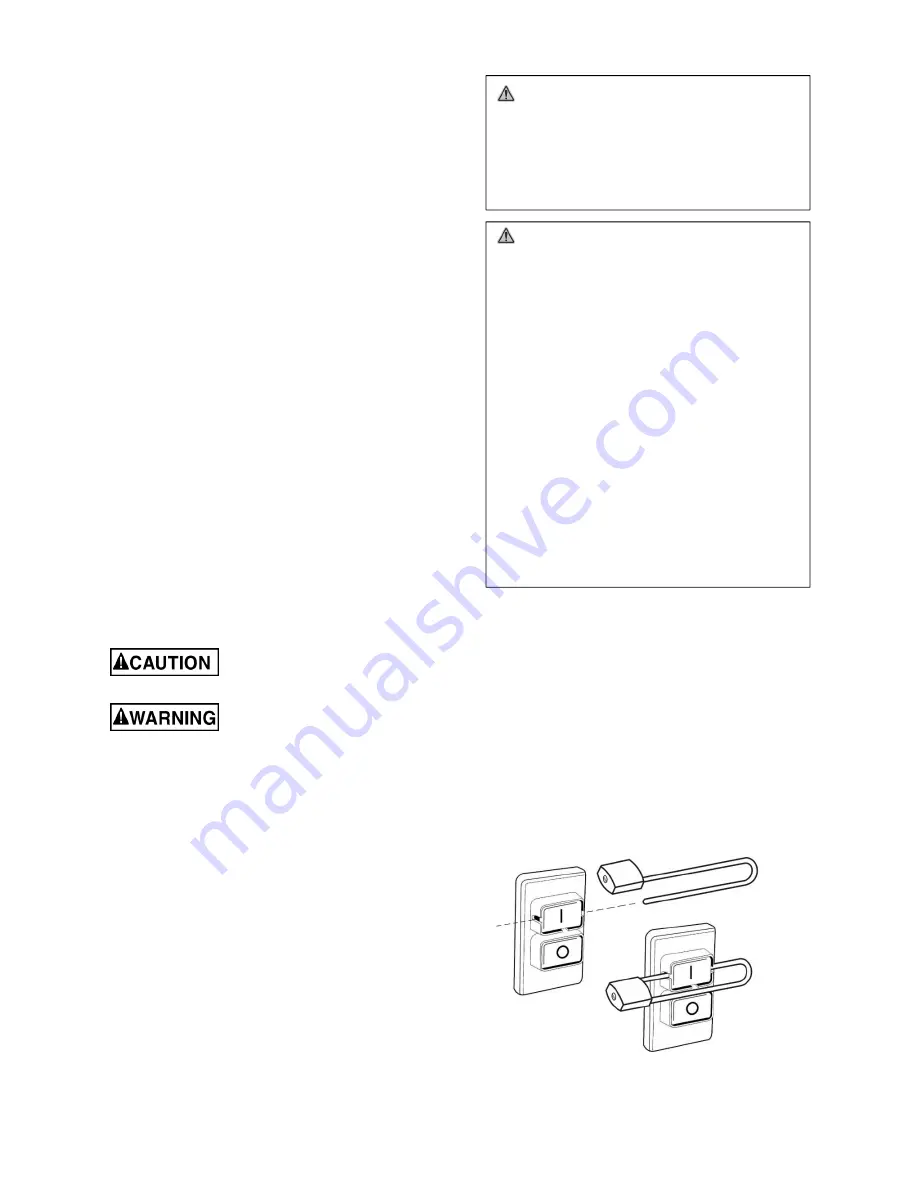
3
29. Never hand hold the material. Always use the
vise and clamp it securely.
30. Be sure that blade is not in contact with
workpiece when motor is started. Allow motor to
come up to speed before bringing blade into
contact with workpiece.
31. Avoid contact with coolant, especially guarding
your eyes.
32. Never reach around or over saw blade during
operation. Keep hands and fingers away from
blade area.
33. Do not remove jammed pieces until blade has
stopped.
34. Don’t use in dangerous environment. Don’t use
power tools in damp or wet location, or expose
them to rain. Keep work area well lighted.
35. Use proper extension cord. Make sure your
extension cord is in good condition. When using
an extension cord, be sure to use one heavy
enough to carry the current your product will
draw. An undersized cord will cause a drop in
line voltage resulting in loss of power and
overheating. Table 2
(sect. 6.3)
shows correct
size to use depending on cord length and
nameplate ampere rating. If in doubt, use the
next heavier gage. The smaller the gage
number, the heavier the cord.
Familiarize yourself with the following safety notices used in this manual:
This means that if precautions are not heeded, it may result in minor injury and/or possible
machine damage.
This means that if precautions are not heeded, it may result in serious, or possibly even fatal,
injury.
1.1
On-off switch padlock
To avoid accidental starting by young children or others not qualified to use the tool, the use of a padlock (not
provided) is required.
To lock out the on-off switch (Figure 2-1):
1. Open
padlock.
2.
Insert through hole in switch guard.
3. Close
padlock.
4.
Store key in a safe place out of the reach of
children.
Figure 1-1
WARNING:
This product can expose you to
chemicals including titanium dioxide which is
known to the State of California to cause cancer,
and lead which is known to the State of
California to cause cancer and birth defects or
other reproductive harm. For more information
go to http://www.p65warnings.ca.gov.
WARNING:
Some dust, fumes and gases
created by power sanding, sawing, grinding,
drilling, welding and other construction activities
contain chemicals known to the State of
California to cause cancer and birth defects or
other reproductive harm. Some examples of
these chemicals are:
lead from lead based paint
crystalline silica from bricks, cement and
other masonry products
arsenic and chromium from chemically
treated lumber
Your risk of exposure varies, depending on how
often you do this type of work. To reduce your
exposure to these chemicals, work in a well-
ventilated area and work with approved safety
equipment, such as dust masks that are
specifically designed to filter out microscopic
particles. For more information go to
http://www.p65warnings.ca.gov/ and http://www.
p65warnings.ca.gov/wood.
Summary of Contents for HVS-8-DMW
Page 20: ...20 11 1 1 HVBS 8 DMW Bow Assembly Exploded View Figure 11 1...
Page 21: ...21 11 1 2 HVBS 8 DMW Table Assembly Exploded View Figure 11 2...
Page 22: ...22 11 1 3 HVBS 8 DMW Motor and Support Arm Assembly Exploded View Figure 11 3...
Page 29: ...29 11 2 1 HVBS 10 DMW DMWC Bow Assembly Exploded View Figure 11 6...
Page 30: ...30 11 2 2 HVBS 10 DMW DMWC Table Assembly Exploded View Figure 11 7...
Page 31: ...31 11 2 3 HVBS 10 DMW DMWC Motor and Support Arm Assembly Exploded View Figure 11 8...
Page 32: ...32 11 2 4 HVBS 10 DMW DMWC Vise and Table Assembly Exploded View Figure 11 9...
Page 33: ...33 11 2 5 HVBS 10 DMW DMWC Base Assembly Exploded View Figure 11 10...
Page 39: ...39 12 0 Electrical Connections for HVBS DMW Band Saws Figure 12 1...