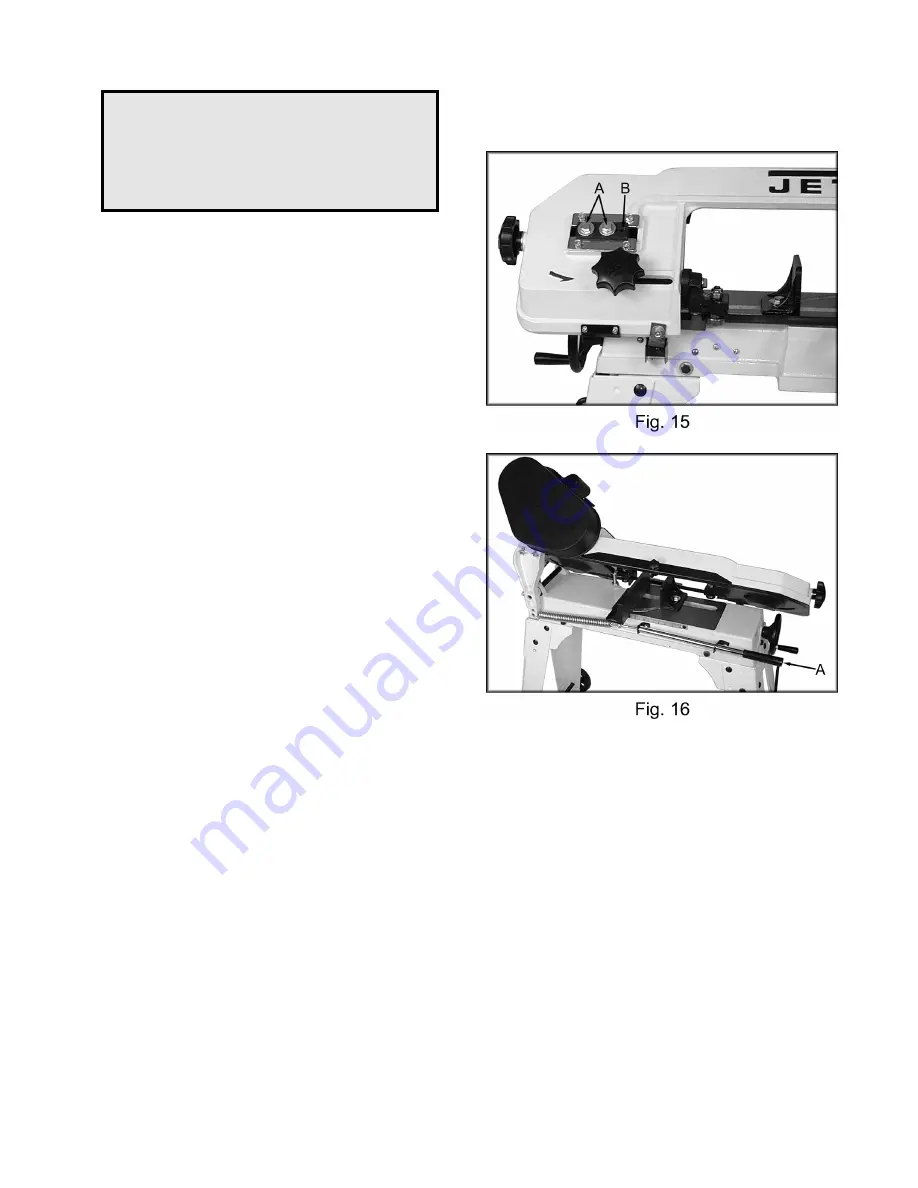
14
Adjusting Blade Tracking
WARNING
Blade tracking adjustment requires running
the saw with the back cover open! This
adjustment must be completed by qualified
persons only!
Failure to comply may cause serious injury!
Blade tracking has been set at the factory and
should not need immediate adjustment. If blade
tracking should ever require adjustment:
1. Confirm that blade tension is set properly.
To adjust, see section titled " Adjusting
Blade Tension".
2. Make sure the saw is in its slowest speed,
see “Changing Blade Speeds”.
3. Move saw arm to the vertical position and
lock in place with the lock lever.
4. Confirm that blade tension is set properly.
To adjust, see section titled " Adjusting
Blade Tension".
5. Open blade cover by removing the knob
found on the top side of the bow.
6. Run saw and observe blade. Blade should
run next to but not tightly against wheel
flange.
7. Loosen bolts (A, Fig. 15).
8. Turn set screw (B, Fig. 15) while observing
blade tracking on wheel. Turn set screw
clockwise to track closer to wheel flange.
Turn set screw counter-clockwise to track
away from the wheel flange.
Hint:
start
with ¼ turns on the set screw. The tracking
is sensitive.
9. Once tracking is set, tighten bolts (A, Fig.
15).
Adjusting Feed Pressure
1. Turn handle (A, Fig. 16) clockwise to
decrease cutting pressure and counter-
clockwise to increase cutting pressure.
A good indication of proper feed pressure is the
color and shape of the cutting chips. If the chips
are thin or powdered, increase the feed pressure.
If the chips are burned and heavy, decrease the
feed pressure. If they are still burned and heavy,
reduce the blade speed. Optimum feed
pressure has been set when the chips are curled,
silvery, and warm.
Summary of Contents for HVBS-56M
Page 17: ...17 Breakdown for Bow Assembly ...
Page 18: ...18 Breakdown for Base Assembly ...
Page 22: ...22 Wiring Diagram ...
Page 23: ...23 Notes ...