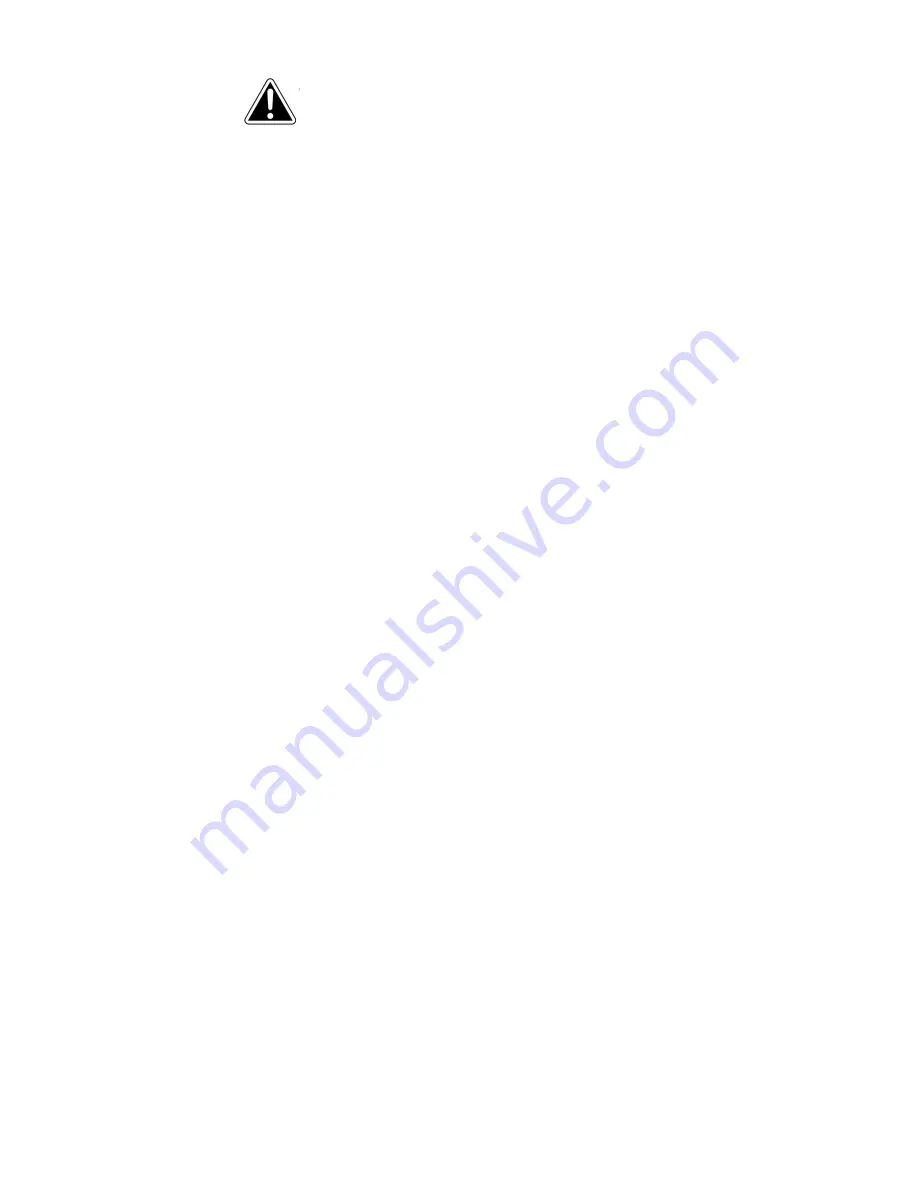
2
1.0
IMPORTANT SAFETY
INSTRUCTIONS
WARNING – To reduce risk of injury:
1. Read and understand the entire owner’s
manual before attempting assembly or
operation.
2. Read and understand the warnings posted on
the machine and in this manual. Failure to
comply with all of these warnings may cause
serious injury.
3. Replace warning labels if they become
obscured or removed.
4. This electric sheet metal notcher is designed
and intended for use by properly trained and
experienced personnel only. If you are not
familiar with the proper and safe operation of a
sheet metal notcher, do not use it until proper
training and knowledge have been obtained.
5. Do not use this sheet metal notcher for other
than its intended use. If used for other
purposes, JET disclaims any real or implied
warranty and holds itself harmless from any
injury that may result from that use.
6. Always wear ANSI Z87.1 approved safety
glasses or face shield while using this machine.
(Everyday eyeglasses only have impact
resistant lenses; they are
not
safety glasses.)
7. Wear ear protectors (plugs or muffs) if noise
exceeds safe levels.
8. Wear appropriate footwear, such as steel-toed
shoes, when working with metal materials.
9. Make certain the machine is properly grounded.
10. Before operating the machine, remove tie,
rings, watches, other jewelry, and roll sleeves
up past the elbows. Do not wear loose clothing.
Confine long hair.
11. Keep the floor around the machine clean and
free of scrap material, oil and grease.
12. Keep machine guards in place at all times when
the machine is in use. If removed for
maintenance purposes, use extreme caution
and replace the guards immediately upon
completion of maintenance.
13. Check damaged parts. Before further use of the
machine, a guard or other part that is damaged
should be carefully checked to determine that it
will operate properly and perform its intended
function. Check for alignment of moving parts,
binding of moving parts, breakage of parts,
mounting and any other conditions that may
affect its operation. A guard or other part that is
damaged should be properly repaired or
replaced.
14. Make all machine adjustments or maintenance
with machine unplugged from power source.
15. Use the right tool. Do not force a tool or
attachment to do a job that it was not designed
to do.
16. Make certain the switch is in the
OFF
position
before connecting the machine to the power
supply.
17. Remove adjusting keys and wrenches. Form a
habit of checking to see that keys and adjusting
wrenches are removed from the machine
before turning it on.
18. Give your work undivided attention. Looking
around, carrying on a conversation and "horse-
play" are careless acts that can result in serious
injury.
19. Keep visitors a safe distance from the work
area. Keep children away.
20. Make your workshop child proof with padlocks,
master switches or by removing starter keys.
21. Do not overreach. Failure to maintain proper
working position can cause you to fall into the
machine or allow clothing to get caught, pulling
you into the machine.
22. Keep the floor around the machine clean and
free of scrap material, oil and grease.
23. Use recommended accessories; improper
accessories may be hazardous.
24. Do not operate this machine while under the
influence of drugs, alcohol or any medication.
25. Keep tools sharp and clean for safe and best
performance.
26. Deburr any sharp metal edges of the workpiece
before placing it into the machine. Use leather
gloves when handling workpieces.
27. Keep hands away from the blade area during
operation.
28. Provide for adequate space surrounding work
area and non-glare, overhead lighting.
29. Don't use in dangerous environment. Don't use
power tools in damp or wet locations, or expose
them to rain.
30. Do not stand on the machine. Serious injury
could occur if the machine tips over.
31. Never leave the machine running unattended.
Turn the power off and do not leave the
machine until it comes to a complete stop.