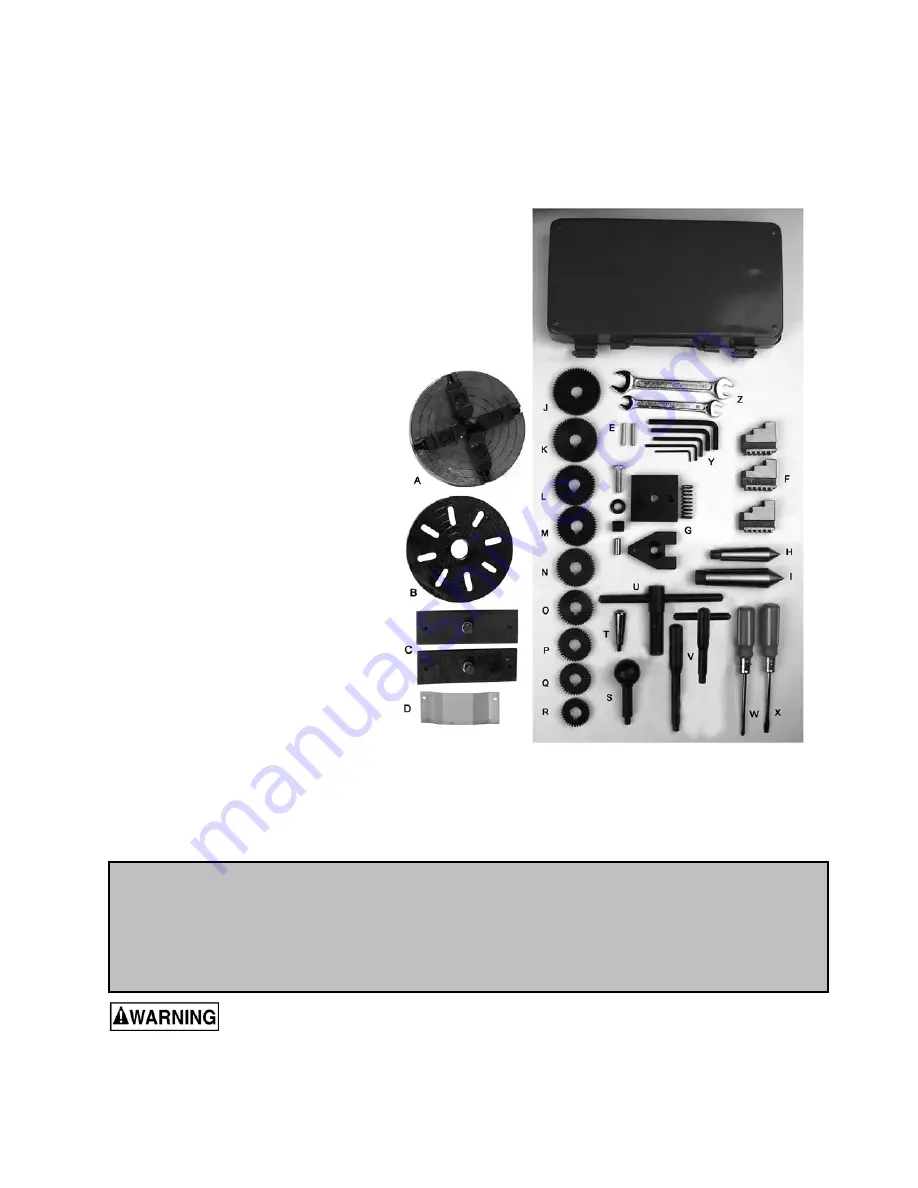
8
Unpacking
Open shipping container and check for shipping damage; report any damage immediately to your distributor
and shipping agent. Do not discard any shipping material until the Lathe is assembled and running properly.
Compare the contents of your container with the following parts list to make sure all parts are intact. Missing
parts, if any, should be reported to your distributor. Read the instruction manual thoroughly for assembly,
maintenance and safety instructions.
Contents of the Shipping Container
Referring to Figure 1:
1
Lathe (not shown)
1 6”
Four-Jaw Independent Chuck (A)
1 Faceplate
(B)
2
Lifting Plates (C)
1 Cover
(D)
1
4” Three-Jaw Universal Chuck (pre-mounted)
1
Four Way Tool Post (pre-mounted)
1
Steady Rest (pre-mounted)
1
Follow Rest (pre-mounted)
1
Operator's Manual (not shown)
1
Warranty Card (not shown)
2
Shear Pins* (E)
3
Chuck Jaws (F)
1
Single Tool Post Assembly* (G)
1 MT-2
Center*
(H)
1 MT-3
Center*
(I)
1
56T Gear* (J)
1
52T Gear* (K)
1
48T Gear* (L)
1
46T Gear* (M)
1
44T Gear* (N)
1
40T Gear* (O)
1
38T Gear* (P)
1
36T Gear* (Q)
1
32T Gear* (R)
1
Tension Roller Lever (S)
1 Handle
(T)
1
Female Chuck Key* (U)
2
Male Chuck Keys (V)
1
#1 Cross Point Screwdriver* (W)
1 #1
Flat
Blade Screwdriver* (X)
1
5pc Hex Wrench Set (Y)
2
Open End Wrenches – 8/10mm, 12/14mm (Z)
* parts marked with an asterisk are included in the tool box, stock no. BD920W-TB
Read and understand the entire contents of this manual before attempting set-up or
operation! Failure to comply may cause serious injury.
CAUTION
The three jaw chuck and the face plate have a set screw on their flanges that secures them to the
threaded spindle. Before removing the three jaw chuck or the faceplate, remove the set screw
completely from the flange. Failure to remove the set screw may cause damage to the threads on
the spindle. When installing either the jaw chuck or the faceplate, tighten the set screw firmly to
prevent the chuck or the faceplate from coming off the spindle during operation.
Figure 1
Summary of Contents for BD-920W
Page 24: ...24 Drive Assembly Exploded View ...
Page 28: ...28 Electrical Assembly Exploded View ...
Page 30: ...30 Gear Box Assembly Exploded View ...
Page 32: ...32 Apron Assembly Exploded View ...
Page 34: ...34 Apron Assembly continued Exploded View ...
Page 36: ...36 Saddle and Cross Slide Exploded View ...
Page 38: ...38 Top Slide Assembly Exploded View ...
Page 40: ...40 Tailstock Assembly Exploded View ...
Page 44: ...44 Lathe Bed Assembly Exploded View ...
Page 46: ...46 Wiring Diagram ...