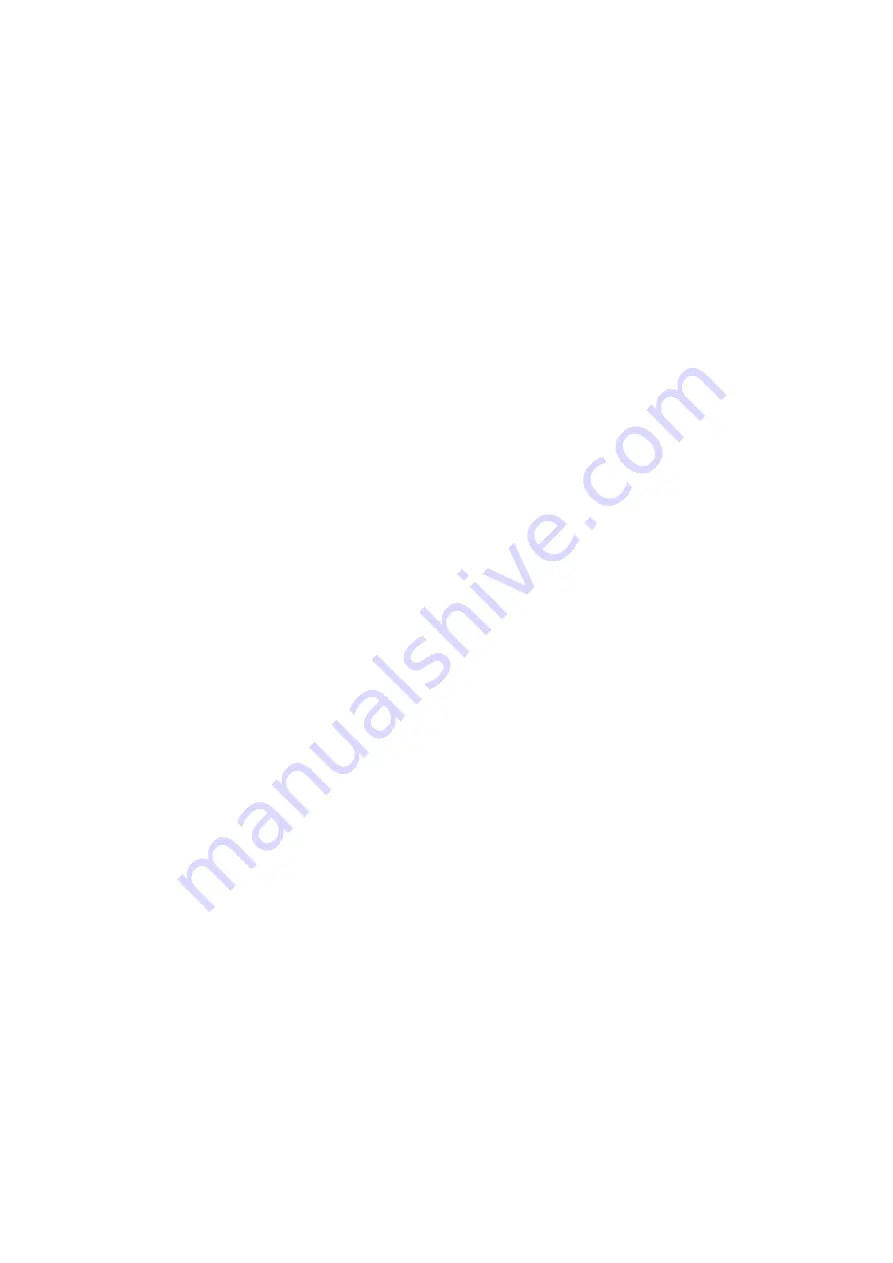
General work safety references.
The wood chipper is built to the very highest standards of engineering and is totally
reliable. Despite this however, this product can also be dangerous when it is not
operated according to the instructions.
Every person who handles the fitting, works on, and tests the wood chipper, must
have read and understood the entire instruction manual. Trouble with and damage to
the wood chipper due to a lack of knowledge on the part of the operator is not
covered by the insurance guarantee.
The wood chipper is intended exclusively for the reducing of bushes and logs, if the
service instructions do not specify any other materials. The maximum diameter of
the wood must be taken from the instruction manual. For any resulting damage the
manufactures can accept no responsibility. The risk lies solely with the user.
When a machine is purchased, the user must follow the references for use, fittings,
safety measures etc.
If any changes in the machine are desired, the owner must first check with the
manufacture. The Failure to do this, and the subsequent malfunction of the machine,
will cause the warantee to be inaffective.
With regard to all work, whether fitting, maintena nce, adjustments and servicing, it is
only to be carried out by authorised and informed members of staff.
The page marked ‘General safety and accident prevention instructions’ should be
read carefully. The safety rules for working with the machine are given by the Trade
Association.
General attendance and inspection references.
There are attendance and installation references in the service instructions and also
an insert from us which describe supply pieces (e.g. motors, clutches) for you to take
note of. Basically the following attendance and inspection work must be carried out:
–
Pay attention to the instructions and maintenance directions of the hydraulic
movements.
–
Check all of the screw joints after 5 hours of use and if necessary change them.
–
The greasing of the turntable should be checked regularly and re-lubricated if
necessary ( only for machines suited with a turntable). The turntable should not
be used if the bearings are dry.
–
A check of the wood chipper should be made after 50 working hours and then
every 100 hours thereafter, or every half a year whichever is the sooner.
–
The wood chipper’s moving parts (e.g. internal combustion engine, electric
motor) must have small checks made and be cleaned – especially the escape
vent for the air so that the cooling system is guaranteed to work - when working
in dusty surroundings or where strong gusts of dust are present during work. The
motor, the motor pieces, and the interior space of the motor must be cleaned
regularly.
The motor inspections and the motor attendance should only be carried out after
reading the instruction manual.
All manuals and user guides at all-guides.com
Summary of Contents for A240 ZKX
Page 2: ...All manuals and user guides at all guides com...
Page 4: ...All manuals and user guides at all guides com...
Page 6: ...All manuals and user guides at all guides com...
Page 8: ...All manuals and user guides at all guides com...
Page 24: ...Knife grinding overview with wear limit All manuals and user guides at all guides com...