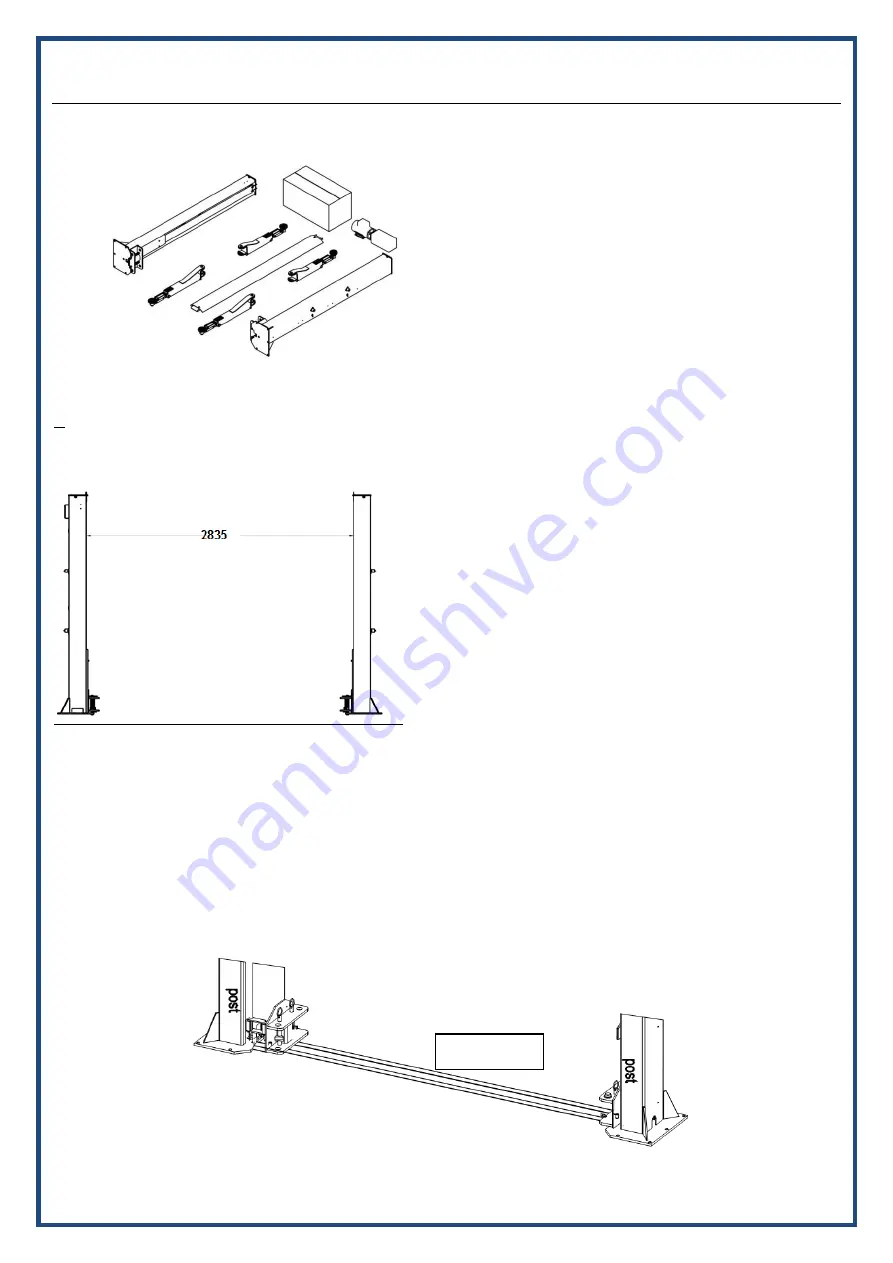
WE ARE HERE TO SURPRISE!
9
Step 5: Decide the installation position of the columns, erect the main and assistant post. Pay attention that the
width between posts is 2830mm.
1. It must also be decided on which side the main column should be placed. (Normally left in the access direction is normal)
2. When the position is selected, use now lime ribbon to place the main column and the assisting column in line to each other.
3. Before work is continued, double check that the columns are the correct position in the room and the columns are properly placed
to each other.
Step 6: Rise the columns, main post first and then the assistant post
Before drilling holes for fixing the columns, place the complete floor plate in between the columns in order to
ensure that the distance is correct.
Floor plate