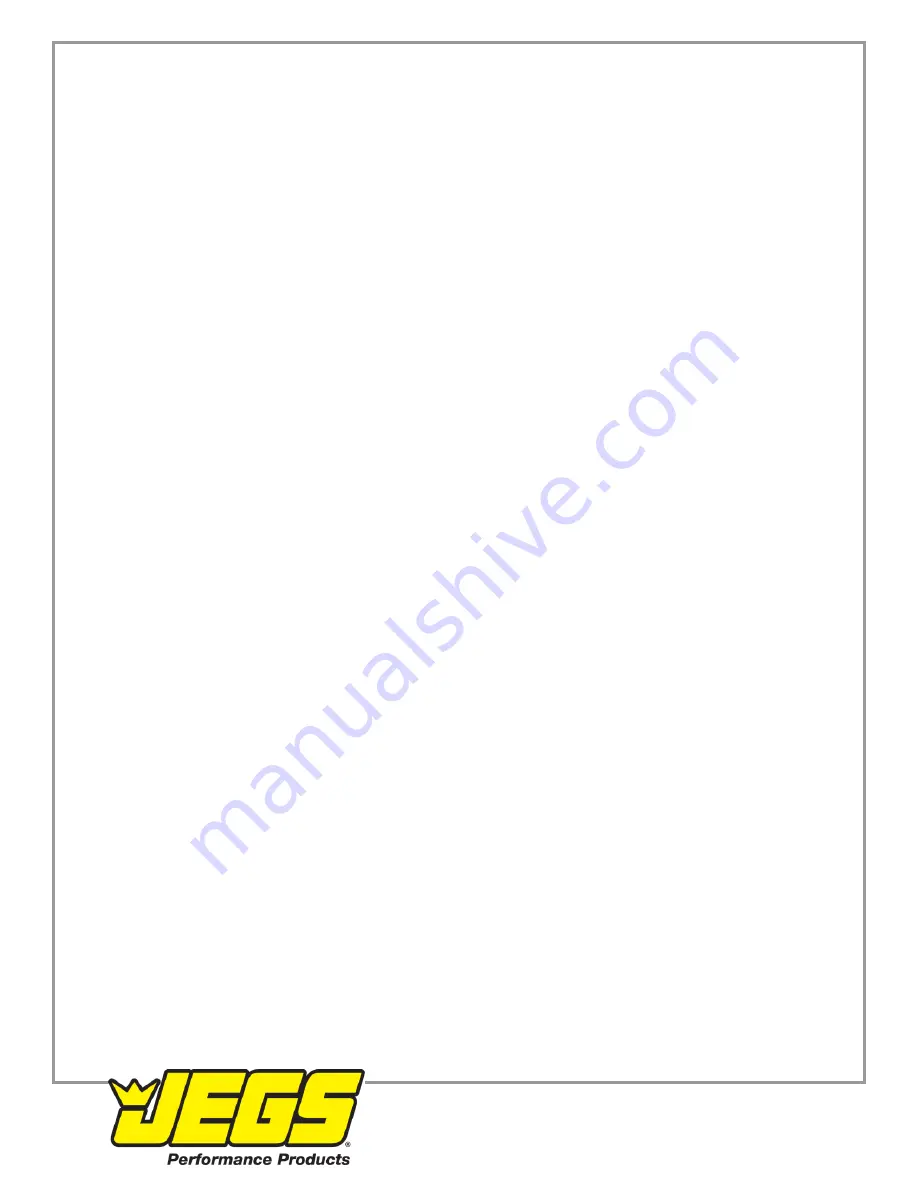
PREPARE WORK AREA FOR JOB
1. Keep work area clean. Cluttered work areas invite accidents.
2. Work area should be properly lit.
3. Keep visitors at a safe distance from work area.
4. Keep children out of workplace. Make workshop childproof. Use locks to prevent any unintentional use of tools.
TOOL SHOULD BE MAINTAINED
1. Keep tool lubricated and clean for safest operation.
2. Remove adjusting tools. Form habit of checking to see that adjusting tools are removed before using machine.
3. Keep all parts in working order. Check to determine that the guard or other parts will operate properly and perform
their intended function.
4. Check for damaged parts. Check for alignment of moving parts, binding, breakage and mounting or any other
condition that may affect a tool's operation.
5. A guard or other damaged part should be properly repaired or replaced. Do not perform makeshift repairs.
KNOW HOW TO USE THE TOOL
1. Use the right tool for the job. Do not force tool or attachment to do a job for which it was not designed.
2. Keep hands and clothing clear of roller nip joints.
3. Do not exceed capacity of the machine. Exceeding capacity may be dangerous to operator and damage the
machine.
4. Bolt machine to floor or sturdy stand that is bolted to the floor to prevent sliding or tipping the machine.
Assembly
Refer to the parts diagram.
Remove crank arm assembly (11-13) from bottom roll (19) by loosening set screw (13). Reverse position and replace
onto roll, then tighten bolt securely.
Installation
The machine should be installed on a level surface, with proper lighting. It is to be stand-mounted or bench-mounted.
Be sure to provide clearance for crank arm rotation. Use the four mounting holes in the base to bolt machine securely
to bench or stand. Fasteners not included. Area around the machine should be clear of scraps, oil & dirt. Apply a
suitable non-skid material to the floor. Allow approximately three feet of clearance on all sides of the slip rolls for ease
of operation.
Operation
1. Adjust the bottom roll position for material thickness. Insert the workpiece between the top and bottom rolls (19, 21).
Turn the bottom roll adjusting knobs (10) until the workpiece fits tightly between the rolls.
2. Adjust the rear roll (20) for the diameter of cylinder to be formed. The position of the rear roll controls the size of the
cylinder that will be formed. Setting roll lower forms a larger diameter cylinder, setting the roll higher forms a smaller
diameter cylinder. Because material sprint back varies with the type of metal being formed, several test workpieces
may need to be formed to obtain correct adjustment of the rear roll. Turn the rear roll adjusting knobs (15) to raise or
lower the rear roll. Turn crank arm (12) clockwise, until workpiece is through the rolls. Check diameter of test workpiece
and adjust the rear roll if necessary. Repeat until the correct adjustments are obtained. Rolls must be adjusted parallel
or the workpiece will spiral during the rolling process.
3. When the cylinder has been formed completely it can be removed without distortion. Grasp the pivot sleeve (22) and
pull out from the frame (16) Pulling the pivot sleeve forward will move the top roll out of the frame.
4. When rolling a workpiece near capacity thickness and length it may be necessary to pass the workpiece through rolls
several times to reduce cylinder to the desired diameter. Adjust rear roll so that the workpiece can pass through the
rolls without difficulty. Slightly raise the rear roll before each succeeding pass until the desired diameter is obtained.
1-800-345-4545 jegs.com