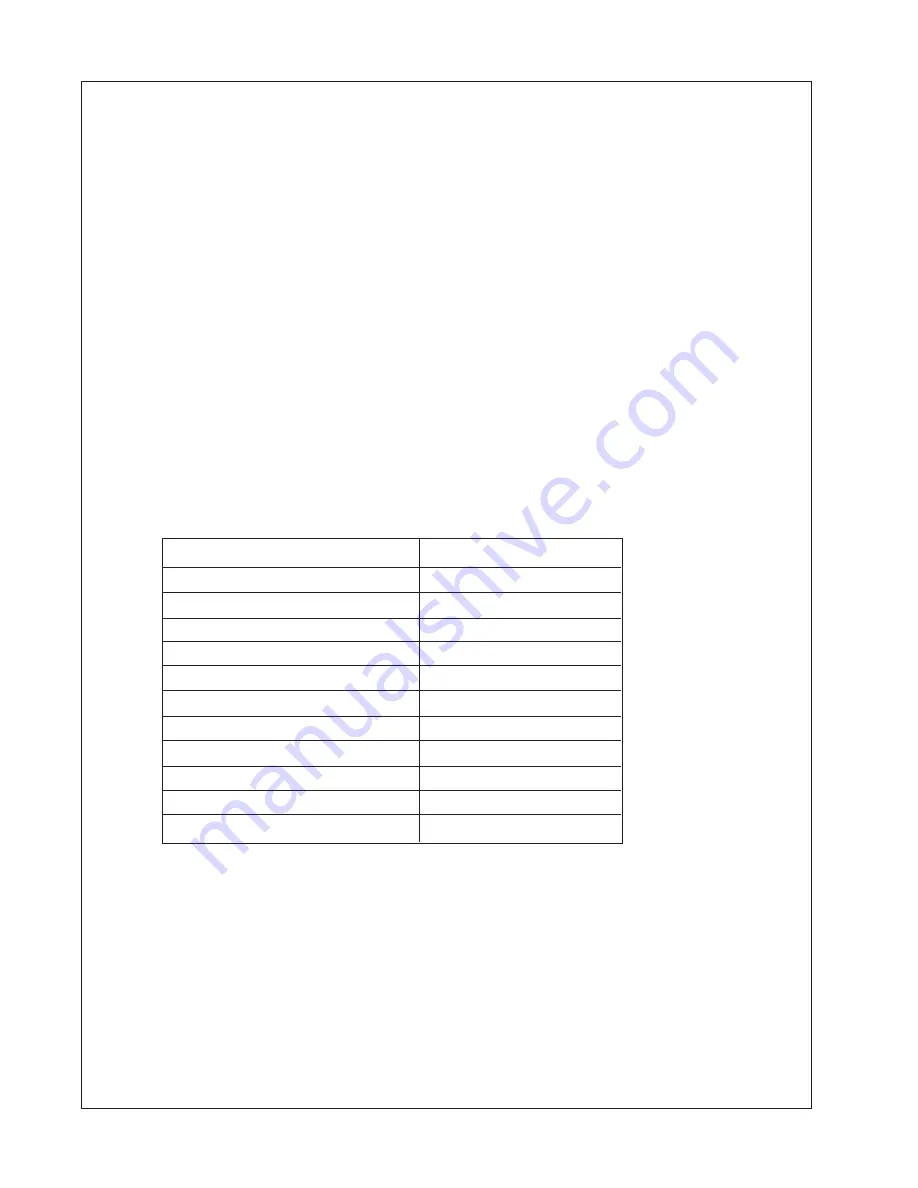
Thermal Paper Specifications
1. Overview
This specification is for thermally coated tickets designed for use with the JCM
TSP-01 thermal printer.
2. General Characteristics
2.1 Tickets to be pre-cut sheets.
2.2 Ticket edges must be smooth to prevent double feeding.
2.3 Ticket size: 65 ± 1 mm x 156 ± 1 mm.
2.4 Tickets to be supplied in bulk stacks of 200.
2.5 Each stack shall have a tear off band.
2.6 Tickets must be processed and cut in a manner that minimizes paper dust.
3. Thermal Paper Specification
ITEM
SPEC.
Weight
g/m² 102 Avg
Caliper
µ 114 Avg (4.5 mils)
Brightness
% 89 Avg
Smoothness
sec. 2000 Avg
Image Colors
Black
Initial Activation Temp.
° C 74 ± 5 O.D. = 0.2
Effective Activation Temp.
° C 83 ± 5 O.D. = 0.8
Optimum Activation Temp.
° C 90 ± 5 O.D. = 1.2
Resistance of Oils
Very Good
Resistance of Alcohol, Solvents
Very Good
15 Hr. Water Immersion
Very Good
6
Summary of Contents for TSP-01
Page 20: ...System Logic Diagram 18 ...
Page 21: ...System Logic Diagram Cont 19 ...