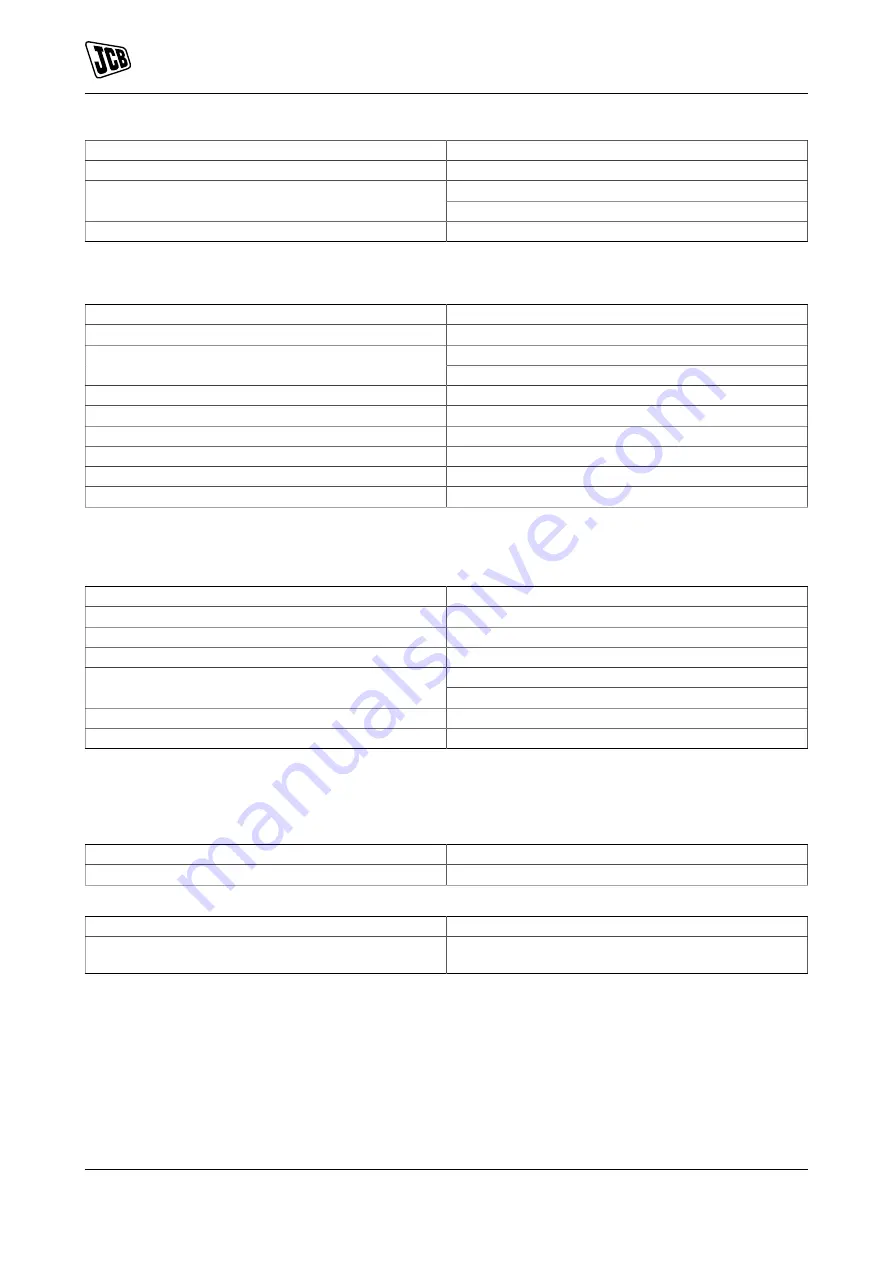
01 - Machine
06 - About this Manual
06 - Using the Manual
01 - 19
9813/7500-2
01 - 19
Cause
Remedy
Pressure switch fault
Refer to (PIL 33-90-00)
Refer to Check (Pressure) (PIL 30-50-03)
Two stage MRV (Main Relief Valve) system fault
(boost function)
Refer to (PIL 33-27-37)
Cylinder ram fault
Refer to Fault Finding (PIL 30-15-00)
(1) Check the applicable hydraulic service cycle times. Refer to Check (Operation) (PIL 30-00-15)
Table 7. Slew service does not operate as expected (including the slew brake)
(1)
Cause
Remedy
Servo pressure not correct
Refer to Check (Pressure) (PIL 30-00-15)
Refer to Controls, Excavator Arm (PIL 09-27-09)
Excavator joystick controller fault
Refer to Fault Finding (PIL 30-60-15)
Excavator control valve fault
Refer to Fault Finding (PIL 30-50-00)
(2)
Pressure switch fault
Refer to (PIL 33-90-00)
Slew lock system fault
Refer to (PIL 33-33-88)
Slew motor fault
Refer to Fault Finding (PIL 30-39-00)
Slew gearbox excessively worn or defective
Refer to (PIL 30-08-06)
Slew ring bearing excessively worn
Refer to Check (Condition) (PIL 06-24-03)
(1) Check the slew service cycle times. Refer to Check (Operation) (PIL 30-00-15)
(2) Check the applicable service spools.
Table 8. Travel service does not operate as expected
(1)(2)
Cause
Remedy
Servo pressure not correct
Refer to Check (Pressure) (PIL 30-00-15)
Excavator control valve fault
Refer to Fault Finding (PIL 30-50-00)
(3)
Travel system fault
Refer to Fault Finding (PIL 27-00-06)
Refer to (PIL 09-27-30)
Track control valve fault
Refer to (PIL 30-60-46)
Track motor fault
Refer to Fault Finding (PIL 27-38-00)
Track components excessively worn or defective
Refer to (PIL 27-36-00)
(1) Check the travel speed times. Refer to Check (Operation) (PIL 30-00-15)
(2) Check the linear travel deviation is acceptable. Refer to Check (Operation) (PIL 30-00-15)
(3) Check the applicable service spools.
Table 9. HVAC (Heating Ventilation Air Conditioning) system does not operate as expected
Cause
Remedy
Control, HVAC unit, cooling, or refrigerant circuit fault Refer to Fault Finding (PIL 12-00-00)
Table 10. Fault codes displayed on the instrumentation
Cause
Remedy
Machine or engine ECU (Electronic Control Unit) has
detected a device fault
Look up the fault code description. Refer to (PIL
33-57-90)
Summary of Contents for JS300
Page 2: ...9813 7500 2 Notes Find manuals at https best manuals com ...
Page 4: ...Notes 9813 7500 2 Find manuals at https best manuals com ...
Page 8: ...Notes 01 2 9813 7500 2 01 2 Find manuals at https best manuals com ...
Page 20: ...Notes 01 14 9813 7500 2 01 14 ...
Page 34: ...Notes 01 28 9813 7500 2 01 28 ...
Page 40: ...Notes 03 2 9813 7500 2 03 2 ...
Page 44: ...Notes 03 6 9813 7500 2 03 6 ...
Page 50: ...Notes 03 12 9813 7500 2 03 12 ...
Page 51: ...This as a preview PDF file from best manuals com Download full PDF manual at best manuals com ...