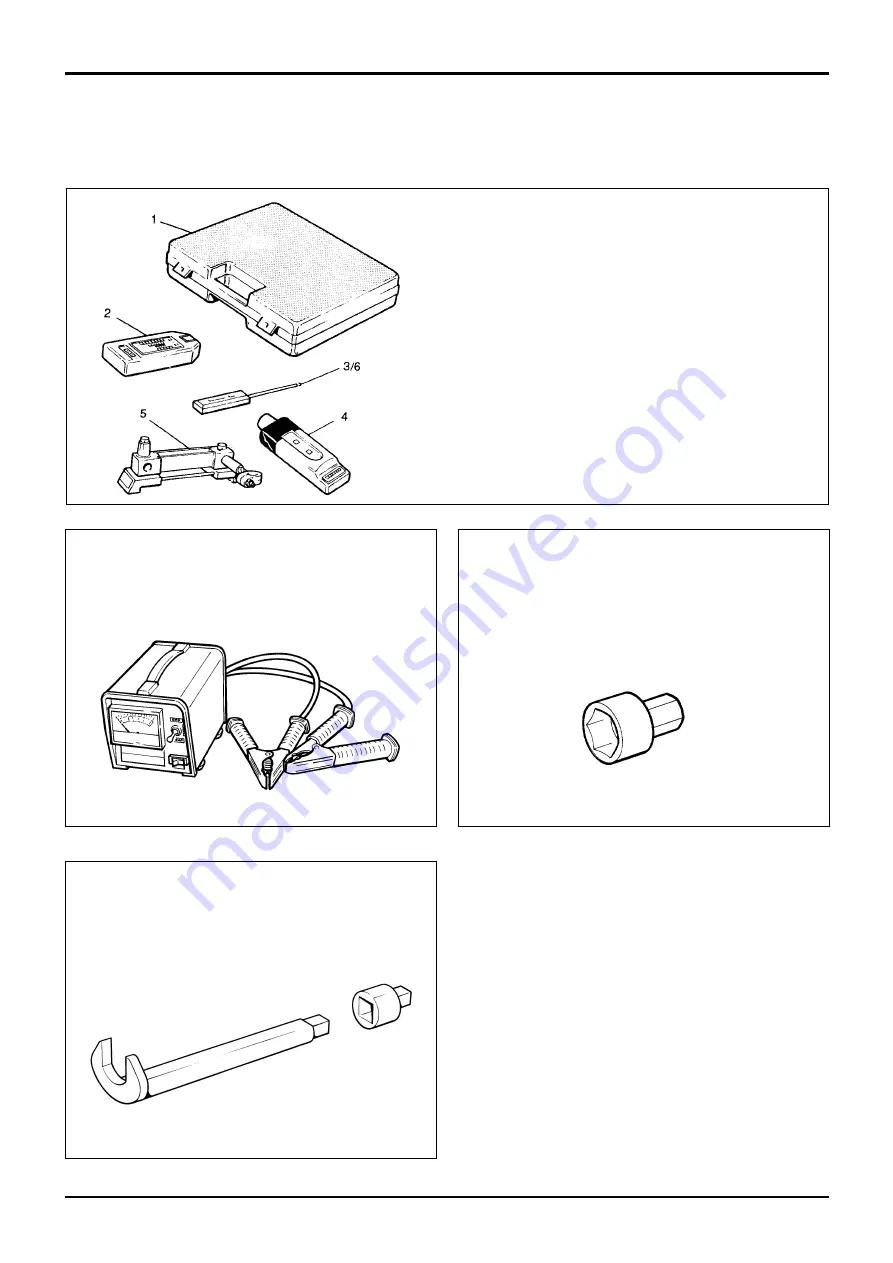
993/85700
Battery Tester
AVO Test Kit
1
892/00283
Tool Kit Case
2
892/00298
Fluke Meter 85
3
892/00286
Surface Temperature Probe
4
892/00284
Venture Microtach Digital
Tachometer
5
892/00282
100 amp Shunt - open type
6
892/00285
Hydraulic Temperature Probe
825/00410
15 mm Crowfoot Wrench
825/99833
Adapter
1 - 1
Section C
9803/3280
Section C
1 - 1
Issue 1
Service Tools
S216200
892/00882
Socket for Alternator Pulley Nut
S216770
S239510
S188231