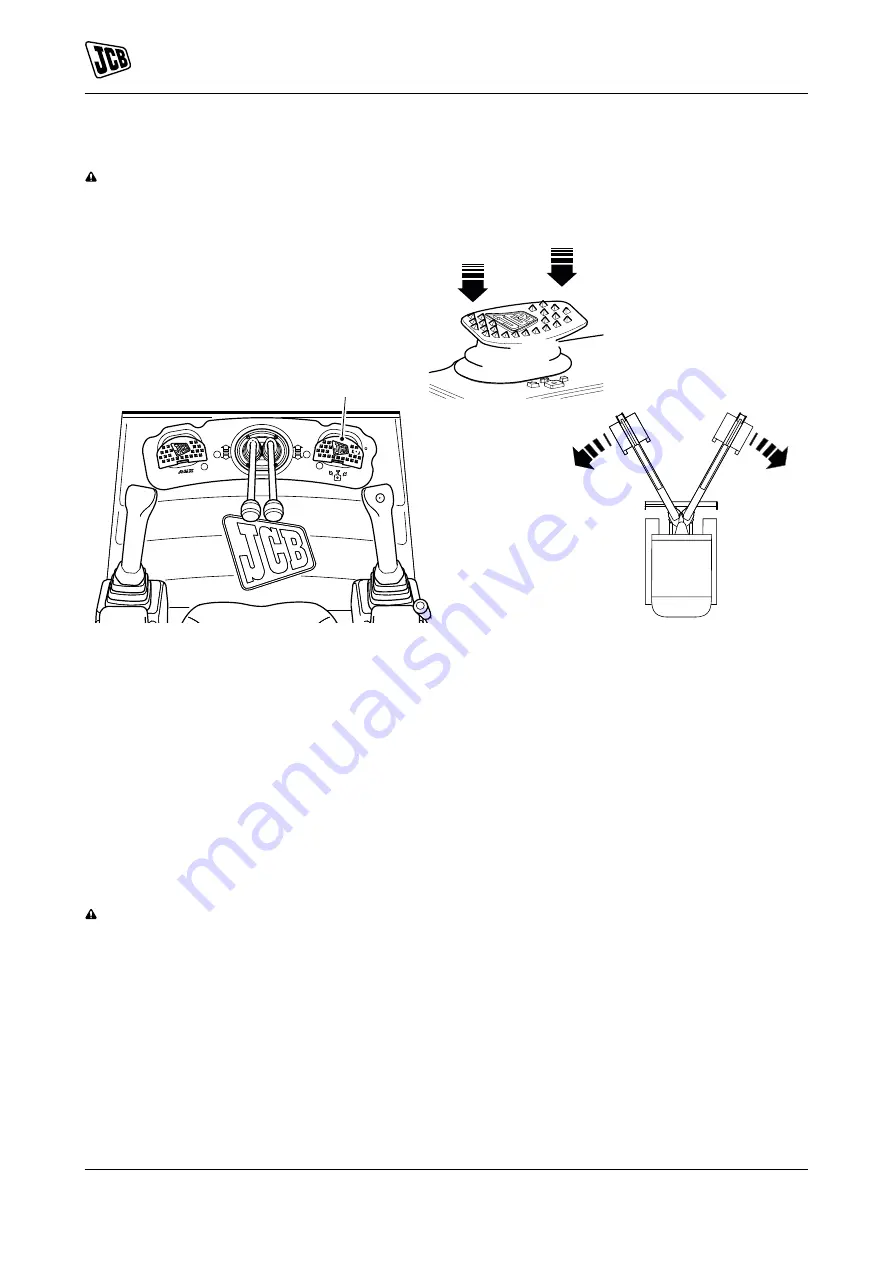
Operation
Operating Levers/Pedals
61
9821/6100-4
61
Swing Pedal
CAUTION
The slew pedal must be in the locked position when not in use.
Figure 50.
B
A
A
B
C
A
Swing left
B
Swing right
C
Swing pedal
To swing the boom to your left:
•
Unlock the swing pedal. (Pivot the swing pedal forward into its operating position).
•
Push the swing pedal to the left side.
•
Release the pedal when the excavator end has reached the required position.
To swing the boom to your right:
•
Unlock the swing pedal. (Pivot the swing pedal forward into its operating position).
•
Push the swing pedal to the right side.
•
Release the pedal when the excavator end has reached the required position.
Dozer Blade Controls
Notice:
Before operating the dozer blade, make sure that large rocks or other objects will not jam the dozer
mechanism.
The dozer is operated by a single control lever on the right side of the cab.
The lever is spring loaded to the central position. In this position the dozer will not move.
To raise the dozer pull the lever backwards. At the required position release the lever.
To lower the dozer push the lever forward until an increased resistance is felt and the blade moves. At the
required position release the lever.
Summary of Contents for 2069289
Page 2: ......
Page 4: ...9821 6100 4 Notes...
Page 12: ...Notes viii 9821 6100 4 viii...
Page 18: ...Notes 6 9821 6100 4 6...
Page 30: ...Notes 18 9821 6100 4 18...
Page 45: ...Operation Windows 33 9821 6100 4 33 Figure 21 A B A Latch B Frame...
Page 98: ...Notes 86 9821 6100 4 86...
Page 207: ...Technical Data Warranty Information 195 9821 6100 4 195 Figure 154 11000h 132 Month h...
Page 208: ...Notes 196 9821 6100 4 196...