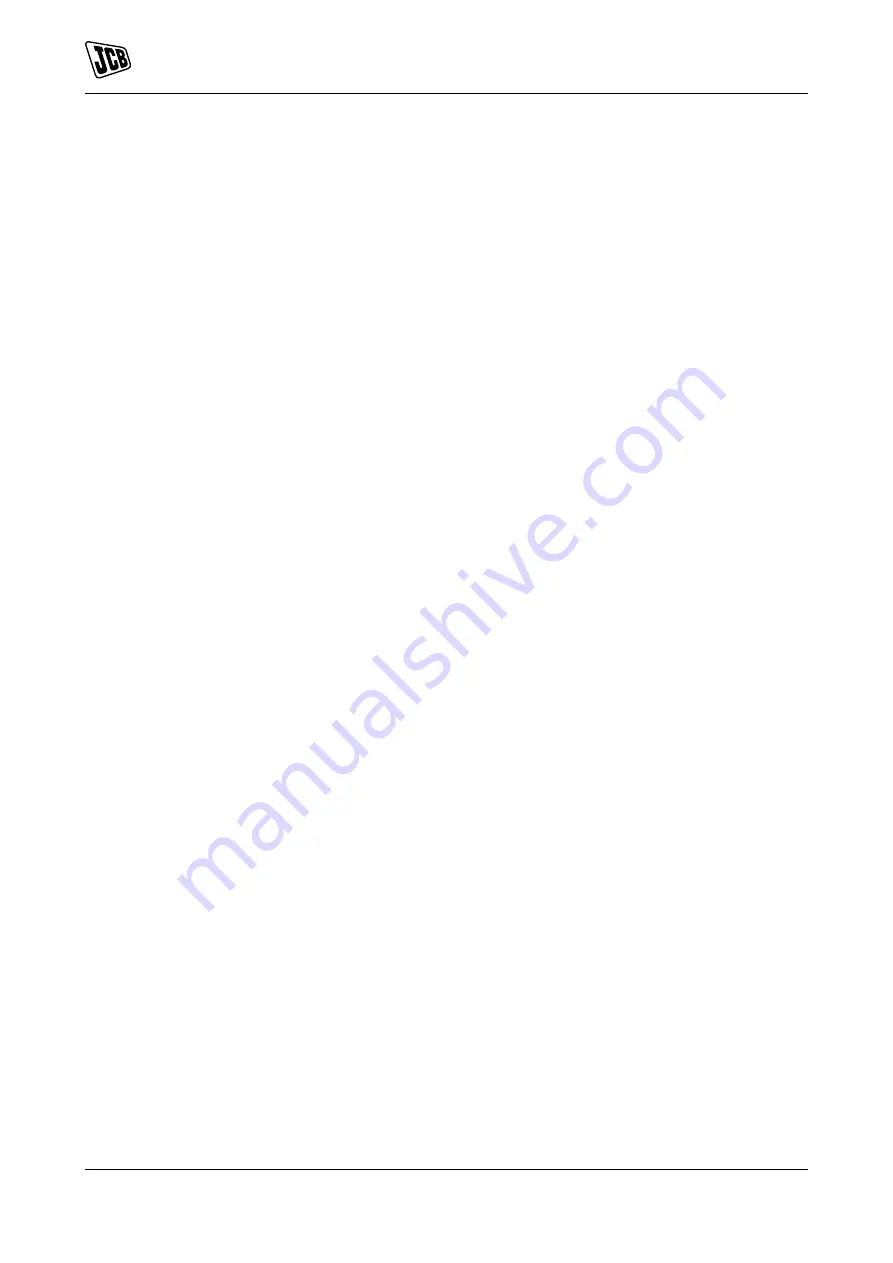
01 - Machine
03 - Safety
12 - Maintenance Safety
01 - 7
9813/5350-2
01 - 7
Working Under the Machine
Make the machine safe before getting beneath it.
Make sure that any attachments on the machine are
correctly attached. Engage the park brake, remove
the ignition key, disconnect the battery. If the machine
has wheels use blocks to prevent unintentional
movement.
Lifting the Machine
Under no circumstances must the engine be run with
the transmission in gear and only one driving wheel
jacked clear of the ground, since the wheel on the
ground will move the machine.
Chemicals
Certain seals and gaskets (e.g. crankshaft oil
seal) on JCB machines contain fluoroelastomeric
materials such as Viton®, FluorelTM and
Technoflon®. Fluoroelastomeric materials subjected
to high temperatures can produce highly
corrosive hydrofluoric acid. This acid can severely
burn. New fluoroelastomeric components at
ambient temperature require no special safety
precautions. Used fluoroelastomeric components
whose temperatures have not exceeded 300°C
(571.6°F) require no special safety precautions. If
evidence of decomposition (e.g. charring) is found,
refer to the next paragraph for safety instructions.
Do not touch component or surrounding area.
Used fluoroelastomeric components subjected to
temperatures greater than 300°C (571.6°F) (e.g.
engine fire) must be treated using the following
safety procedure. Make sure that heavy duty gloves
and special safety glasses are worn: Thoroughly
wash contaminated area with 10% calcium hydroxide
or other suitable alkali solution, if necessary use
wire wool to remove burnt remains. Thoroughly
wash contaminated area with detergent and water.
Contain all removed material, gloves etc. used in this
operation in sealed plastic bags and dispose of in
accordance with Local Authority Regulations. Do not
burn fluoroelastiometric materials.
Hydraulic Hoses
Never re-use hydraulic hose end crimps or use
reusable hose end crimps.
Personal Protective Equipment
Use the appropriate personal protective equipment
before performing maintenance on the machine,
otherwise you could be injured.
Working at Height
Use appropriate access equipment such as ladders
or a working platform if it is necessary to work at
height to perform maintenance tasks on the machine.
If you do not use suitable access equipment there is
a risk of falling, resulting in personal injury or death.
Summary of Contents for 10TFT
Page 2: ...9813 5350 2 Notes Find manuals at https best manuals com ...
Page 4: ...Notes 9813 5350 2 Find manuals at https best manuals com ...
Page 8: ...Notes 01 2 9813 5350 2 01 2 Find manuals at https best manuals com ...
Page 20: ...Notes 01 14 9813 5350 2 01 14 ...
Page 24: ...Notes 01 18 9813 5350 2 01 18 ...
Page 36: ...Notes 06 2 9813 5350 2 06 2 ...
Page 40: ...Notes 06 6 9813 5350 2 06 6 ...
Page 48: ...Notes 06 14 9813 5350 2 06 14 ...
Page 51: ...This as a preview PDF file from best manuals com Download full PDF manual at best manuals com ...