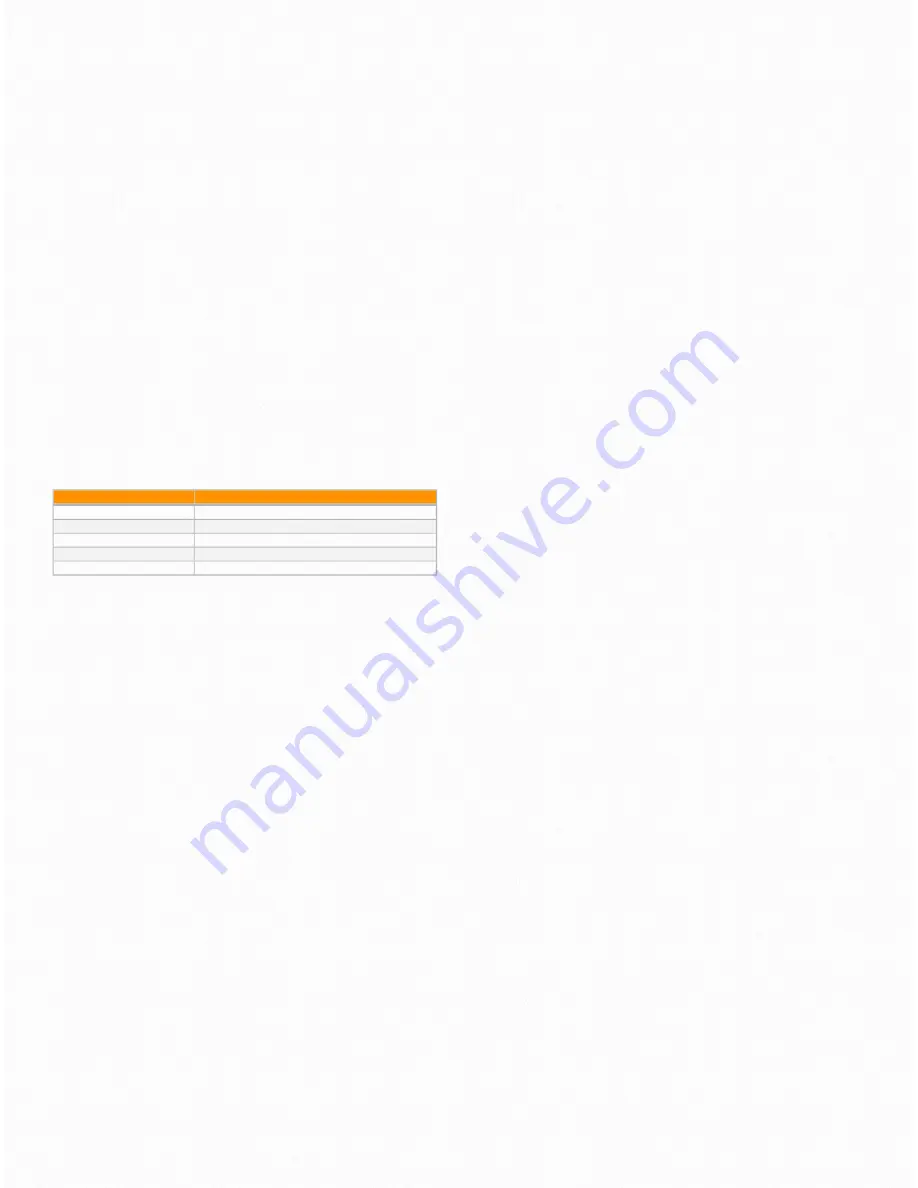
Operation
Before starting any welding activity ensure that you have
suitable eye protection and protective clothing. Also take
the necessary steps to protect any persons within the
area.
MMA
After connecting the welding leads as detailed you will need
to switch the power switch to “ON”
Select MMA by switching to the MMA welding mode. There
is voltage output at both output terminals.
Select the current mode - AC or DC
Set the amperage on the machine suitable for the electrode
being used. Please see below a guide to amperages
required. Ensure you check that you have the electrode
polarity correct.
Set the arc force current percentage as required. This can be
adjusted during welding.
Standard TIG mode
Connect the TIG torch leads as detailed above. Ensure that a
suitable inert gas supply is connected and the flow rate is
set
Switch the power switch on the front panel to “ON”
Select the TIG welding mode using the selector switch.
Select the TIG operating mode (2T, 4T) using the selector
switch.
2T: Press the torch trigger, gas valve opens, and HF arc
ignition starts; Keep the torch 2~4mm away from the work
piece to ignite the arc. When the arc is established the HF
stops, and current rises to the preset value; Release the
torch trigger, current decreases to the minimum value, and
then arc stops; Gas keeps flowing for the post-flow time,
and welding ends.
4T: Press the torch trigger, gas valve opens, and HF arc
ignition starts; Keep the torch 2~4mm away from the work
piece to ignite the arc. When the arc is established the HF
stops, and current rises to the preset value; Release the
torch trigger, and welding continues at the preset current
level. Press the torch trigger again and release it, current
begins to decrease to the minimum value, and then arc
stops; Gas keeps flowing for the post-flow time, and welding
ends.
Select the welding mode AC or DC
Set the welding current to suit the application
Set the downslope time
If welding in AC mode then set the cleaning control
percentage as required
If using a remote control current device connect it to the
socket on the front of the machine
Pulsed TIG mode
Connect the TIG torch leads as detailed above. Ensure that a
suitable inert gas supply is connected and the flow rate is
set
Switch the power switch on the back panel to “ON”
Select the TIG welding mode using the selector switch.
Select the TIG operating mode (2T, 4T) using the selector
switch.
2T:
Press the torch trigger, gas valve opens, and HF arc ignition
starts; Keep the torch 2~4mm away from the work piece to
ignite the arc. When the arc is established the HF stops, and
current rises to the preset value; Release the torch trigger,
current decreases to the minimum value, and then arc stops;
Gas keeps flowing for the post-flow time, and welding ends.
4T:
Press the torch trigger, gas valve opens, and HF arc ignition
starts; Keep the torch 2~4mm away from the work piece to
ignite the arc. When the arc is established the HF stops, and
current rises to the preset value; Release the torch trigger,
and welding continues at the preset current level. Press the
torch trigger again and release it, current begins to decrease
to the minimum value, and then arc stops; Gas keeps
flowing for the post-flow time, and welding ends.
Select the welding mode AC or DC
Select the pulse operating mode using the selector switch
10
Electrode Diameter (mm)
Recommended Welding Current (A)
1.6
44~84
2.0
60~100
2.5
80~120
3.2
108~148
4.0
140~180