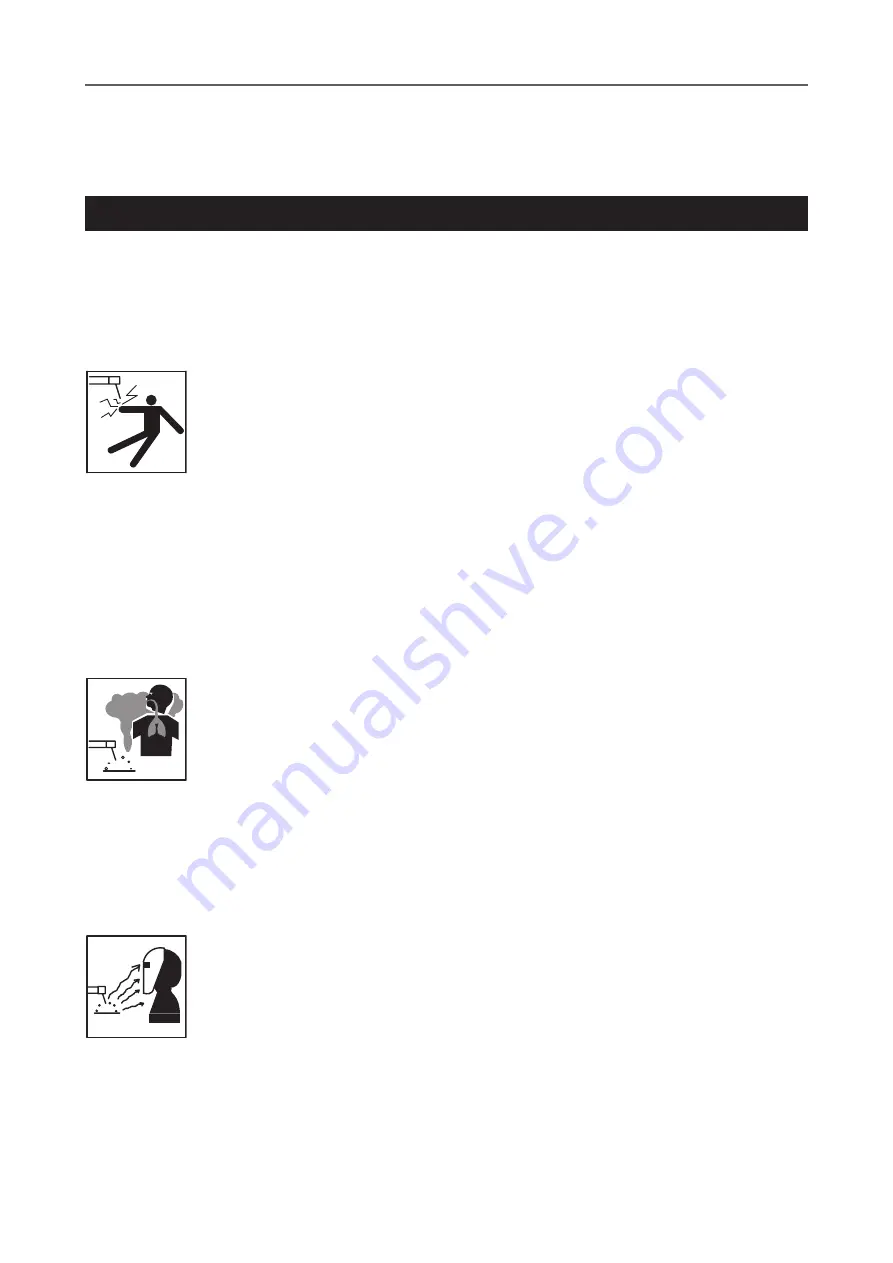
Welding and cutting equipment can be dangerous to both the operator and people in or near the
surrounding working area if the equipment is not correctly operated. Equipment must only be used
under the strict and comprehensive observance of all relevant safety regulations.
Read and understand this instruction manual carefully before the installation and operation of this equipment.
WARNING: USE COMPRESSED AIR ONLY WITH THIS MACHINE
Machine Operating Safety
• Do not switch the function modes while the machine is operating. Switching of the function modes during
welding can damage the machine. Damage caused in this manner will not be covered under warranty.
• Disconnect the electrode-holder cable from the machine before switching on the machine, to avoid arcing
should the electrode be in contact with the workpiece.
• Operators should be trained and or qualified.
Arc rays: harmful to people’s eyes and skin.
Arc rays from the welding/cutting process produce intense visible
and invisible ultraviolet and infrared rays that can burn eyes and skin.
• Always wear a welding helmet with the correct shade of filter lens and suitable protective clothing, including
welding gloves while the welding/cutting operation is performed.
• Measures should be taken to protect people in or near the surrounding working area. Use protective screens or
barriers to protect others from flash, glare and sparks; warn others not to watch the arc.
Fumes and gases are dangerous.
Smoke and gas generated while welding or cutting can be harmful to people’s
health. Welding produces fumes and gases. Breathing these fumes and gases can be hazardous to your health.
• Do not breathe the smoke and gas generated while welding or cutting, keep your head out of the fumes.
• Keep the working area well ventilated, use fume extraction or ventilation to remove welding/cutting fumes and
gases.
• In confined or heavy fume environments always wear an approved air-supplied respirator.
• Welding/cutting fumes and gases can displace air and lower the oxygen level, causing injury or death. Be sure
the breathing air is safe.
• Do not weld/cut in locations near degreasing, cleaning, or spraying operations. The heat and rays of the arc can
react with vapours to form highly toxic and irritating gases.
• Materials such as galvanised, lead, or cadmium plated steel, containing elements that can give off toxic fumes
when welded/cut. Do not weld/cut these materials unless the area is very well ventilated, and or wearing an
air-supplied respirator.
Electric shock: It can kill.
Touching live electrical parts can cause fatal shocks or severe burns. The electrode
and work circuit is electrically live whenever the output is on. The input power circuit and internal machine circuits
are also live when power is on. In MIG/MAG welding, the wire, drive rollers, wire feed housing, and all metal
parts touching the welding wire are electrically live. Incorrectly installed or improperly grounded equipment is
dangerous.
•
Connect the primary input cable, according to North American Standards.
•
Avoid all contact with live electrical parts of the welding/cutting circuit, electrodes and wires with bare hands.
•
The operator must wear dry welding gloves while he/she performs the welding/cutting task.
•
The operator should keep the workpiece insulated from himself/herself.
•
Keep cords dry, free of oil and grease, and protected from hot metal and sparks.
•
Frequently inspect input power cable for wear and tear, replace the cable immediately if damaged, bare
wiring is dangerous and can kill.
•
Do not use damaged, undersized, or badly joined cables.
•
Do not drape cables over your body.
SAFETY
4
Summary of Contents for RAZORCUT 40PCI
Page 1: ...OPERATING MANUAL RAZORCUT 4OPCI 40 AMP PLASMA CUTTER WITH INTERNAL AIR COMPRESSOR SKU RC40PCi...
Page 2: ...2...
Page 26: ...NOTES 25...
Page 27: ...NOTES 26...
Page 28: ...NOTES 27...