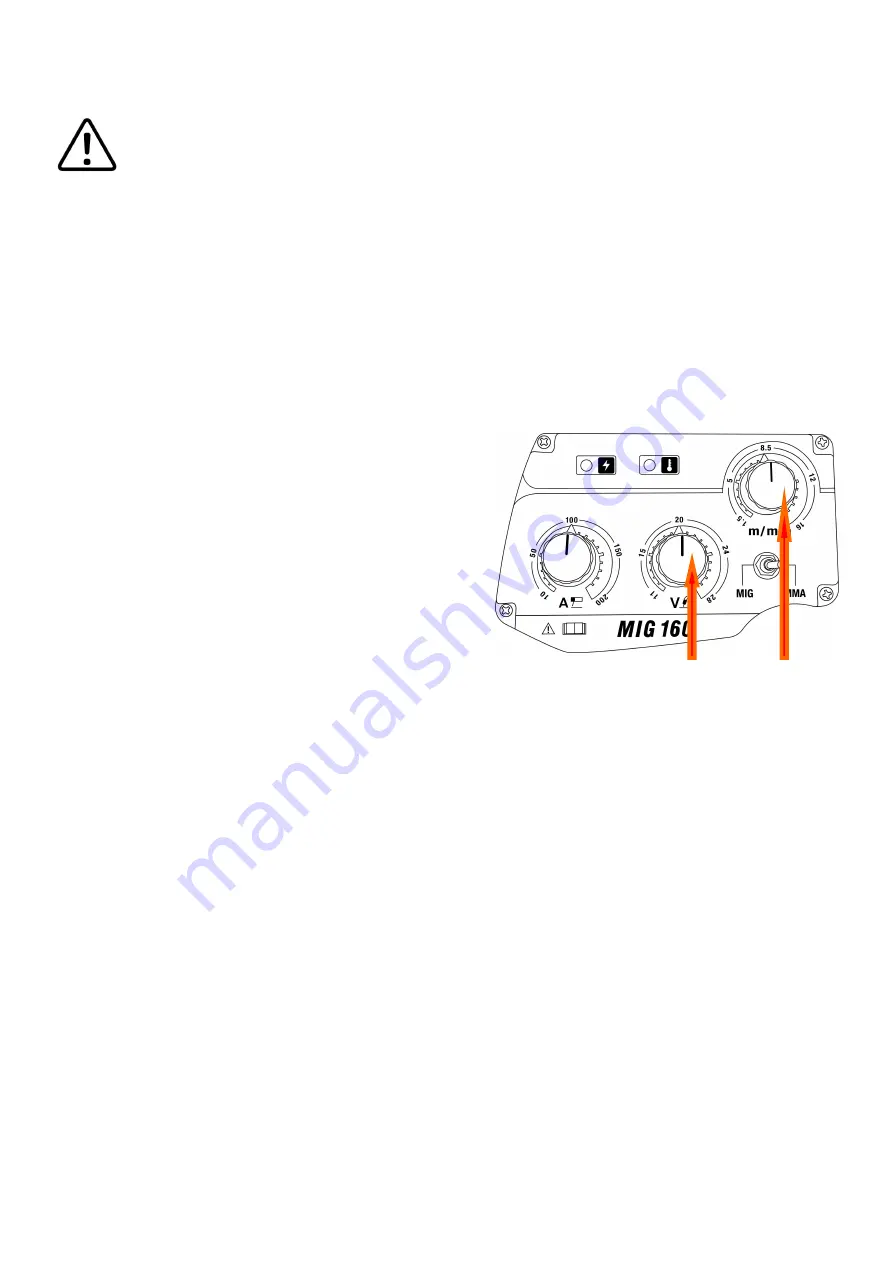
24
GUIDE TO MIG/MAG WELDING
Before starting any welding activity ensure that you have suitable eye protection and
protective clothing. Also take the necessary steps to protect any persons within the welding
area.
MIG controls
The main basic controls for the MIG/MAG system are as follows. Controls can be electro mechanical
or electronic but the effects will be the same.
Wire feed speed
The wire speed is directly related to the current. The higher the wire speed the more wire is deposited
and hence more current is required to burn off the consumable wire.
Wire speed is measured in m/min (metres per min) or sometimes in ipm (inches per minute).
The diameter of the wire also forms part of the current demand e.g. a 1.0mm wire feeding at 3m per min
will require less current than a 1.2mm wire feeding at the
same rate.
The wire feed is set according to the material to be
welded.
If the wire feed rate is too high in comparison to the
voltage then a “stubbing” effect happens where unmelted
consumable contacts the work piece creating large
amounts of weld spatter.
Too little wire feed comparison to the voltage will result in
a long arc being created with poor transfer and eventual
burning back of the wire onto the contact tip.
Voltage Wire Speed
Voltage setting
The voltage polarity in MIG/MAG welding is in the majority of cases with the positive (+). This means
that the majority of the heat is in the electrode wire. Certain special wires may require the polarity to be
reversed i.e. electrode wire negative (-) polarity. Always consult the manufacturer's data sheet for the
best operating parameters.
The voltage is often referred to as the “heat setting”. This will be altered dependent on the material type,
thickness, gas type, joint type and position of the weld. Combined with the wire speed it is the main
control adjusted by the welder. The voltage setting varies depending on the type and size of electrode
wire being used.
Most MIG/MAG welders are CV or Constant Voltage power sources which means the voltage does
not vary much during welding. Modern inverter power sources also have control circuits to monitor
conditions to ensure voltage remains constant.
The voltage determines height and width of the weld bead. If the operator has no reference to settings
required the best method of set up is to use scrap material of the same thickness to obtain the correct
setting. If there is too much voltage the arc will be long and uncontrollable and cause the wire to fuse
to the contact tip. If the voltage is too low then there will not be enough heat to melt the wire and then
stubbing occurs.
To obtain a satisfactory weld a balance needs to be made between voltage and wire speed.
Characteristics of the voltage are that the higher voltage produces a flatter and wider weld bead but
care must be taken to avoid undercut. The lower the voltage the weld bead becomes narrow and higher.