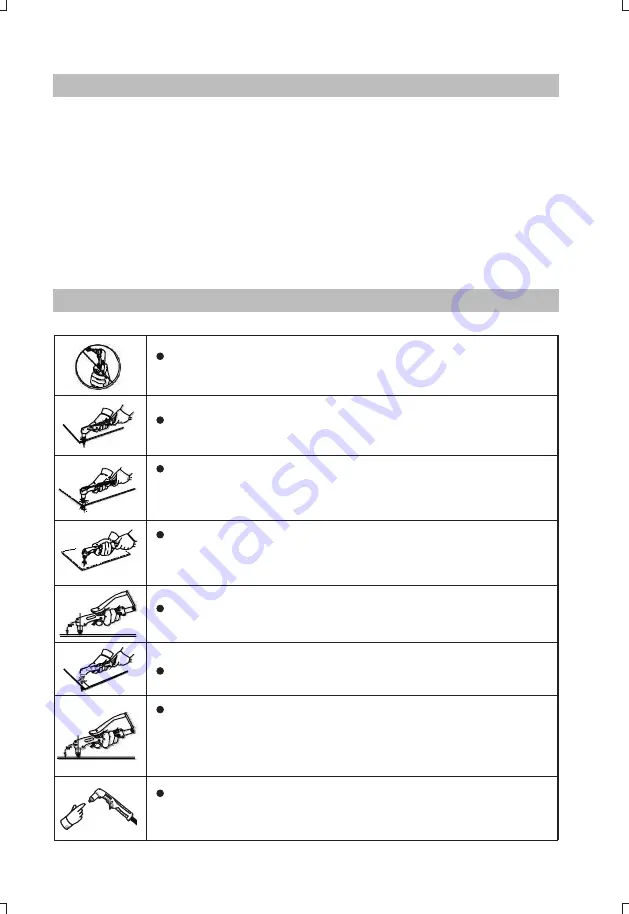
12
3.4 Operation method
1
)
Turn on the power switch of the machine, and the power indicator illuminates.
2
)
Select proper working mode and proper function. There are two working modes available on
the machine panel: 2T and 4T. There are two functions available: normal cutting and metal mesh
cutting. The electrode and nozzle are more easily to wear out in metal mesh cutting.
3
)
Push the torch trigger on the cutting torch, the cutting machine works.
4
)
Set cutting current according to the thickness of workpiece.
5
)
Bring the copper nozzle of the cutting torch into contact with the workpiece
(
For models with
pilot arc function, keep a distance of about 2mm between the copper nozzle of the torch and the
workpiece.
)
, and then push the torch trigger. After the arc is ignited and started, raise the cutting
torch to the position about 1mm above the workpiece, and start cutting.
3.5 Notes for cutting operation
It is recommended not to ignite the arc in the air if not necessary, for it
will shorten the lifespan of the electrode and nozzle of the torch.
It is recommended to initiate the cutting from the edge of workpiece,
unless penetration is needed.
Ensure spatters fly from the bottom of workpiece while cutting. If spatters
fly from the top of workpiece, it indicates that the workpiece can not be
fully cut because the cutting torch is moved too fast or the cutting current
is too low.
Keep the nozzle slightly touching the workpiece or keep a short distance
between the nozzle and workpiece. If the torch is pressed against the
workpiece, the nozzle may stick to the workpiece, and smooth cutting
is unavailable.
For cutting round workpiece or to meet precise cutting requirement,
molding board or other assistant tools are needed.
It is recommended to pull the cutting torch while cutting.
Keep the nozzle of cutting torch upright over the workpiece, and check
if the arc is moving with the cutting line. If the space is not enough,
don’t bend the cable too much, step on or press upon the cable to avoid
suffocating of gas flow. The cutting torch may be burned because the
gas flow is too small. Keep the cutting cable away from edge tools.
Clean up the spatters on the nozzle timely, for it will affect the cooling
effect of the nozzle. Clean up the dust and spatters on the torch head
after using everyday to ensure good cooling effect.