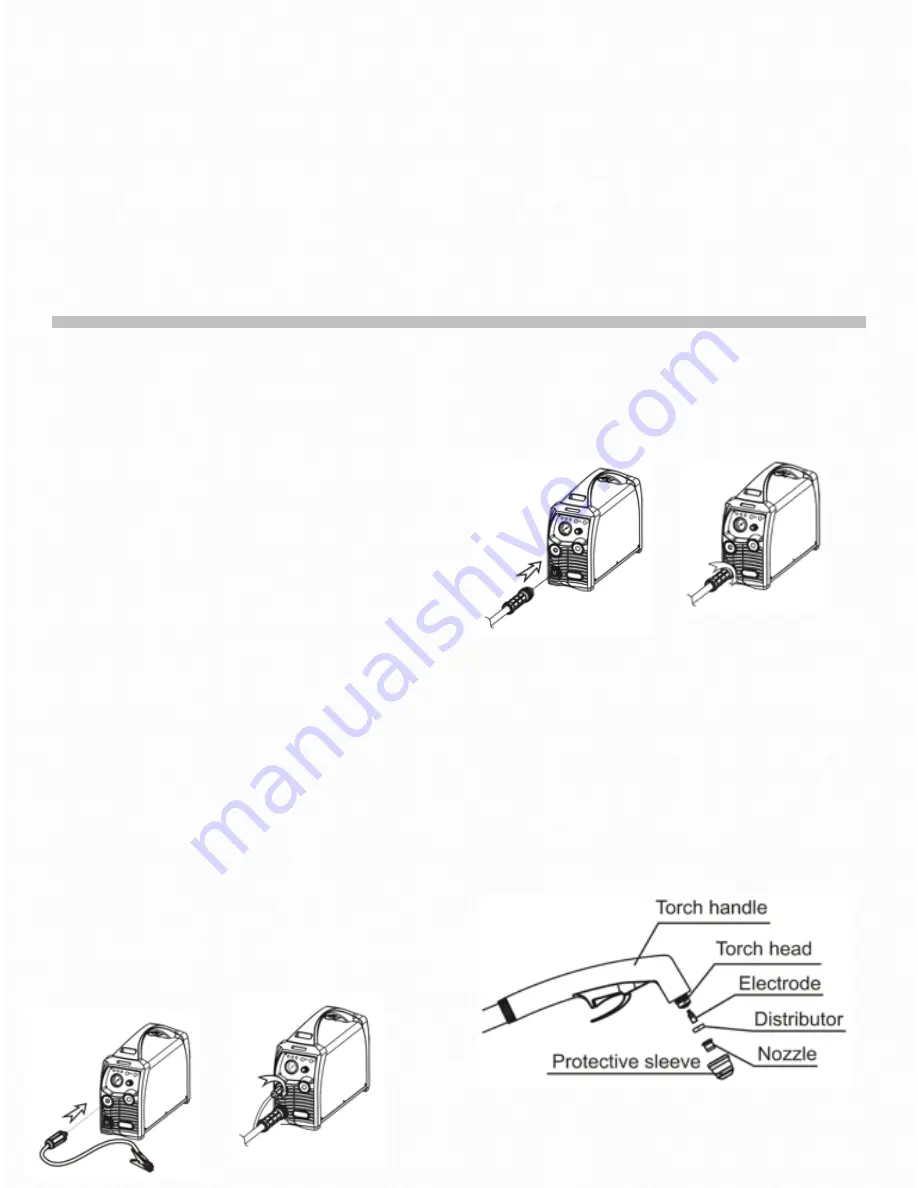
Installation
5
Unpacking
Check the packaging for any signs of damage.
Carefully remove the machine and retain the packaging until
the installation is complete.
Location
The machine should be located in a suitable position and
environment. Care should be taken to avoid moisture, dust,
steam, oil or corrosive gases
Place on a secure level surface and ensure that there is
adequate clearance around the machine to ensure natural
airflow.
Input connection
Before connecting the machine you should ensure that the
correct supply is available. Details of the machine
requirements can be found on the data plate of the machine
or in the technical parameters shown in the manual.
The equipment should be connected by a suitably qualified
competent person. Always ensure the equipment has a
proper grounding.
Never connect the machine to the mains supply with the
panels removed.
Connection of work cable
Insert the quick plug on the work cable into the quick socket
at the bottom of the front panel of the machine, and tighten
it clockwise. Clamp the workpiece with the work clamp at
the other end of the earth cable.
Connection of cutting torch
Connect the central connection plug on the cutting torch to
the central connection socket of the power supply, and
tighten It clockwise to avoid gas leakage.
Installation of the cutting torch
1)
Screw the end of the electrode with screw thread into
the torch head, and tighten it.
2)
Insert the other end of the electrode into the
distributor.
3)
Connect the nozzle with the electrode and distributor.
4)
Connect the protective sleeve with the nozzle, screw
it into the torch head, and tighten it.
Note: Screw the electrode into the torch with an inner
hexagon spanner, and tighten it. Otherwise, the inner thread
of the electrode will be burned.
9