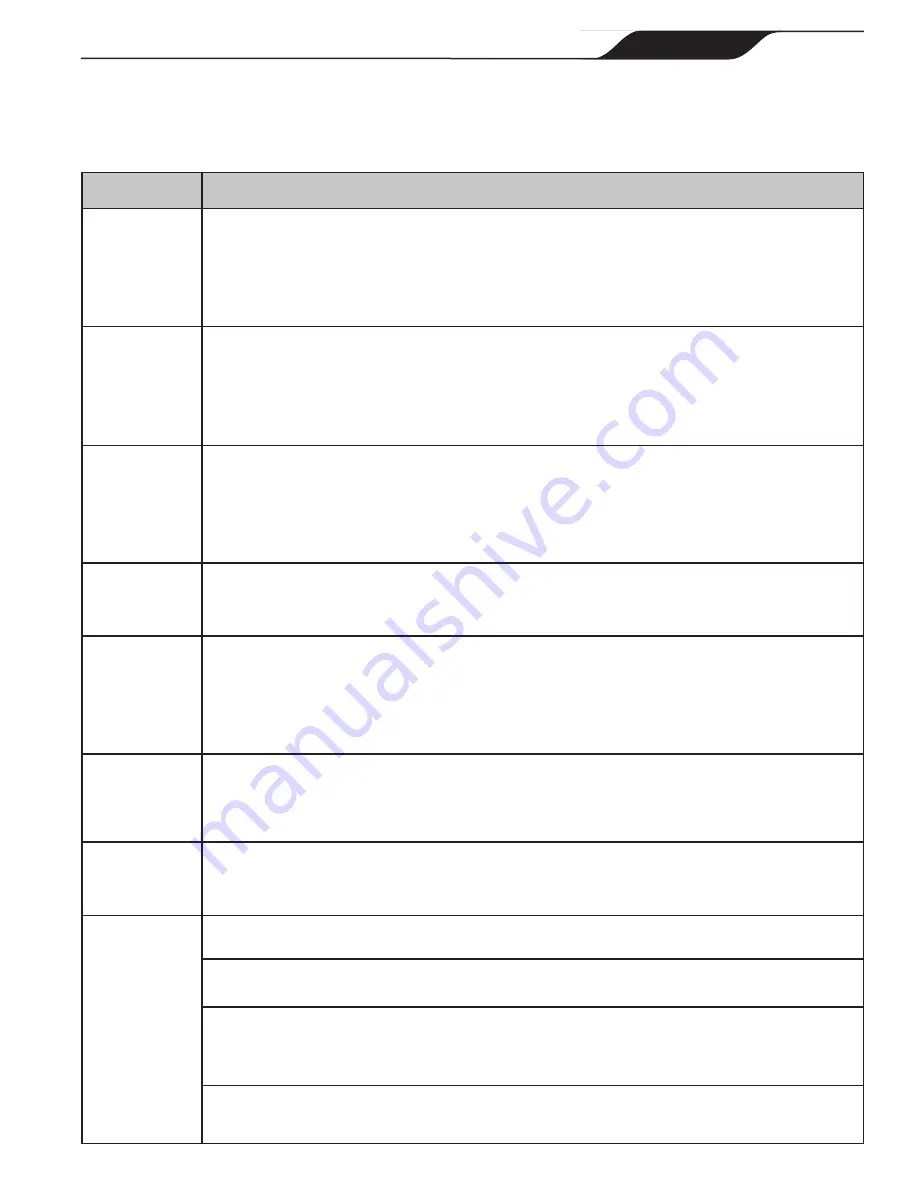
Page 15
ENGLISH
Jandy
®
Pro Series VS PlusHP Pumps
|
Installation & Operation Manual
Section 6. Troubleshooting and Repair
Zodiac® strongly recommends that you call a qualified service technician to perform any repairs on the filter/pump
system. To locate a qualified technician, check your local yellow pages or visit www.zodiacpoolsystems.com
or www.zodiacpoolsystems.ca and click on “Dealer Locator.”
Symptom
Possible Cause/Solution
Reduced flow
being returned
to pool and/or
less water being
pulled in by
skimmer.
Verify that skimmer baskets, pump basket and other screens are clean. Clean as necessary.
Check filter and clean as necessary.
Check valve positions. Adjust as necessary.
NOTE
Multiple pieces of equipment operating at one time (for example, waterfalls, spa jets, and surface
returns) will affect the proper operation of the cleaning system.
Check the cleaning system manual to ensure that the system is adjusted according to the manufacturer's
recommendations.
Bubbles are
present in the
pump basket.
Air is in the system. Check the pool or spa water level to ensure that it is at the proper level and air is not
being drawn into the suction piping. If the water is at the normal level, turn off the pump. Turn the lid's locking
ring counter-clockwise until 'START' aligns with the ports. Remove the lid and check for debris around the
lid seal seat OR improper installation of the lid seal, as either condition will allow air to leak into the system.
Clean the lid seal and replace it on the lid. Replace the lid on the pump housing. Align 'START' with the ports
and turn the locking ring clockwise until 'LOCKED' aligns with the ports.
Hand-tighten
the lid to make an air-
tight seal.
Do not use any tools to tighten the lid.
Turn the pump back on.
Air leaks are still
present.
Check the suction side piping union. While the pump is running, try to tighten the union. If this does not stop
the air leak, turn off the pump. Loosen both unions and slide the pump out of the way. Remove, clean, and
re-install both union o-rings.
Reposition the pump next to the piping and secure the union nuts to the pump. With clean union o-rings,
hand-tightening of the unions should create a seal. If the unions still do not seal, gently tighten with a large
pair of tongue-and-groove pliers.
Do not over-tighten
.
There is no air in
the system, but
the pressure is
still low.
It is possible that debris is caught in the pump impeller. The pump impeller moves the water, and the vanes in the
impeller can become blocked with debris.
There is no debris
blocking the
impeller
and
the
pressure is still
low.
The pump impeller and diffuser are showing signs of normal wear. Have a qualified service technician check
the impeller and diffuser and replace as necessary.
If the pump is part of a relatively new installation, it could be an electrical problem. Contact a qualified
service technician. Have the technician check for loose electrical connections and check the voltage at the
pump motor while it is in operation. The voltage must be within 10% of the motor's data plate rating. If the
voltage is not within 10%, contact a qualified electrician and/or the local power service provider.
Pump seal is leaking air. Have a qualified service technician replace the seal.
The pump is
leaking water
between the
motor and pump
body.
This is caused by a damaged or failed mechanical seal. Replace the seal.
The pump gets
hot and shuts off
periodically.
Make sure that there is adequate room around the motor to circulate air and keep the motor cool. Have
a qualified electrician check for loose connections and check the voltage at the pump motor while it is in
operation. The voltage must be within 10% of the motor's data plate rating. If the voltage is not within 10%,
contact a qualified electrician and/or the local power service provider.
Pump will not
start.
No power to pump.
Make sure pump is properly connected to high voltage. See
“3.2 Electrical Installation”
Improper low-voltage wiring.
Check low-voltage wiring between pump and controller. Correct if necessary. See
“3.2 Electrical Installation”
Improper pump address setting.
Make sure that pump dip switches 3 and 4 are set properly for the installation. Both should be OFF for use
with Variable-Speed Controller or set to the proper address when connected to an AquaLink
®
RS controller,
an AquaLink
PDA, or an AquaLink Z4. See
“3.2.4.1 Install with AquaLink® controller”
Fault condition exists.
View fault message on controller and correct fault before proceeding. If unsure how to correct fault, contact
Zodiac
®
Technical Support at 800.822.7933.