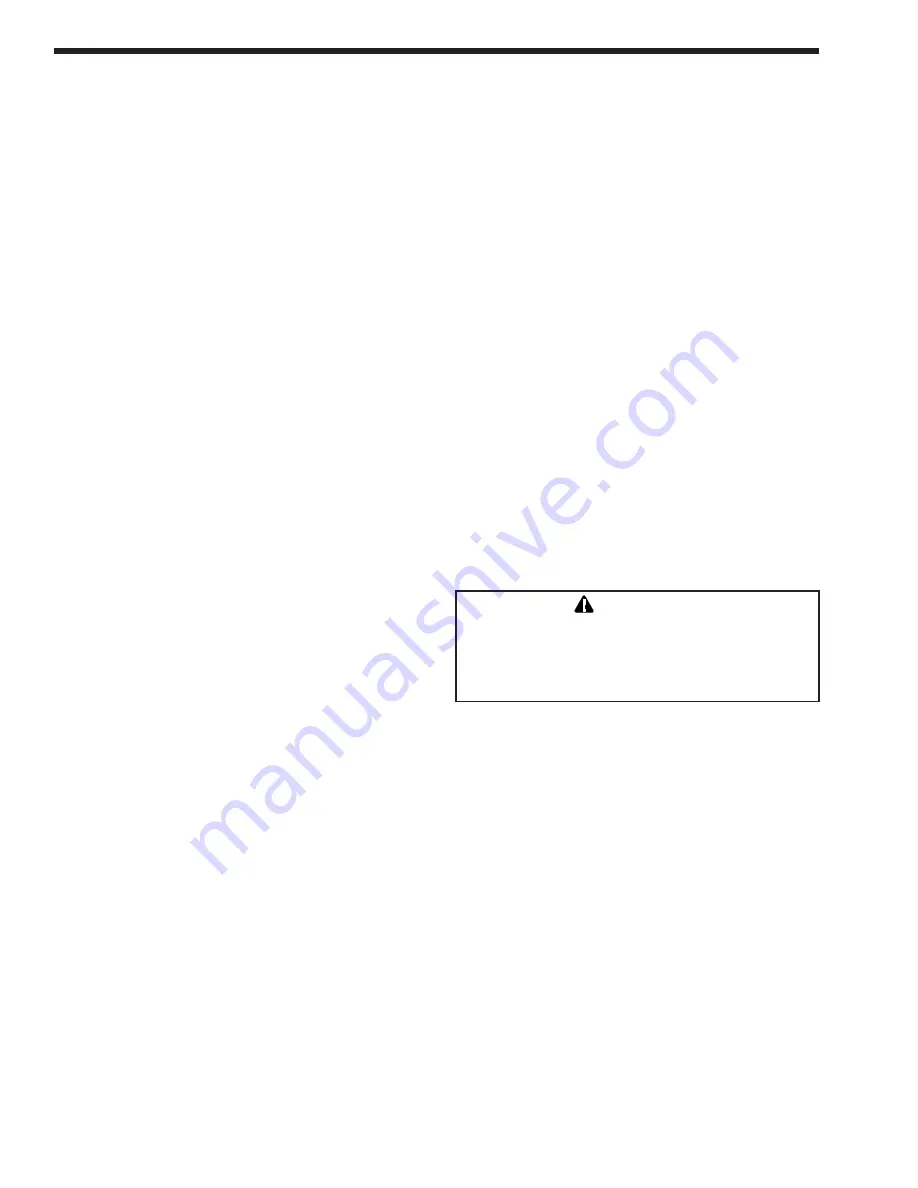
Water Pik Technologies, Inc.
Page 10
4.
If there are still air leaks check the suction side
piping union.
a. While the pump is running, try to tighten the
union. If this does not stop the air leak,
continue to the next step.
b. Turn off the pump.
c. Loosen both unions and slide the pump out
of the way.
d. Remove, clean and place both union o- rings.
e. Reposition the pump next to the piping and
secure the union nuts to the pump. With
clean union o-rings, hand tightening of the
unions should create a seal. If the unions still
do not seal, gently tighten with a large
tongue-and-groove pliers. DO NOT over
tighten.
5.
If there is no air in the system, but the pressure
is still low.
a. It is possible that debris is caught in the
pump impeller. The Impeller is what moves
the water and has vanes that can become
blocked with debris. See "Blocked Impeller"
(Section 9A) under the "Specialty Service"
section of this manual.
6.
If there is nothing blocking the impeller and the
pressure is still low. There are three other
possible reasons for this;
a. The pump has been in an abrasive
environment for a long period of time, and
the impeller and diffuser are showing signs
of wear. If the problem is normal wear on the
Impeller and diffuser, have a qualified
service technician replace them.
b. If this is a relatively new installation, it could
be an electrical problem. This problem can
be easily identified by a qualified service
technician. Have the technician check for
loose electrical connections and check the
voltage at the pump motor while it is in
operation. The voltage must be within 10%
of the motor's nameplate rating. If it is not,
then a qualified electrician and/or the power
company needs to get involved to resolve the
problem.
c. Pump seal is leaking air. Have a qualified
service technician replace the seal.
7.
The pump is leaking water between the motor
and pump body.
a. This is caused by a damaged or failed
mechanical seal. To solve this problem, the
seal must be replaced. See "Mechanical Seal
Replacement" under "Speciality Service"
section of this manual.
8.
The pump gets hot and shuts off periodically.
a. Make sure the motor has plenty of room to
circulate air and keep cool. Have a qualified
electrician check for loose connections and
check the voltage at the pump motor while it
is in operation. The voltage must be within
10% of the motor's nameplate rating. If it is
not, then a qualified electrician and/or the
power company needs to get involved to
resolve the problem.
SECTION 9.
Specialty Service
TWater Pik Technologies, inc. recommends that
you call a qualified service technician to perform any
repairs on the filter/pump system.
9A. Blocked Impeller
1.
Turn off the pump. Switch off the circuit breaker
to the pump motor.
2.
Remove the lid and basket.
3.
Look inside the pump for any debris. Remove
any debris found inside.
4.
Replace the basket and lid.
5.
Switch on the circuit breaker to the pump motor.
6.
Turn on the pump, and see if the problem is
solved.
7.
If the impeller is still blocked with debris and it
is not possible to remove the debris this way, the
pump will need to be disassembled to access the
inlet and outlet of the impeller.
While servicing the pump, switch off the circuit
breakers at the power source. Severe personal
injury or death may occur if the pump starts while
your hand is inside the pump.
WARNING