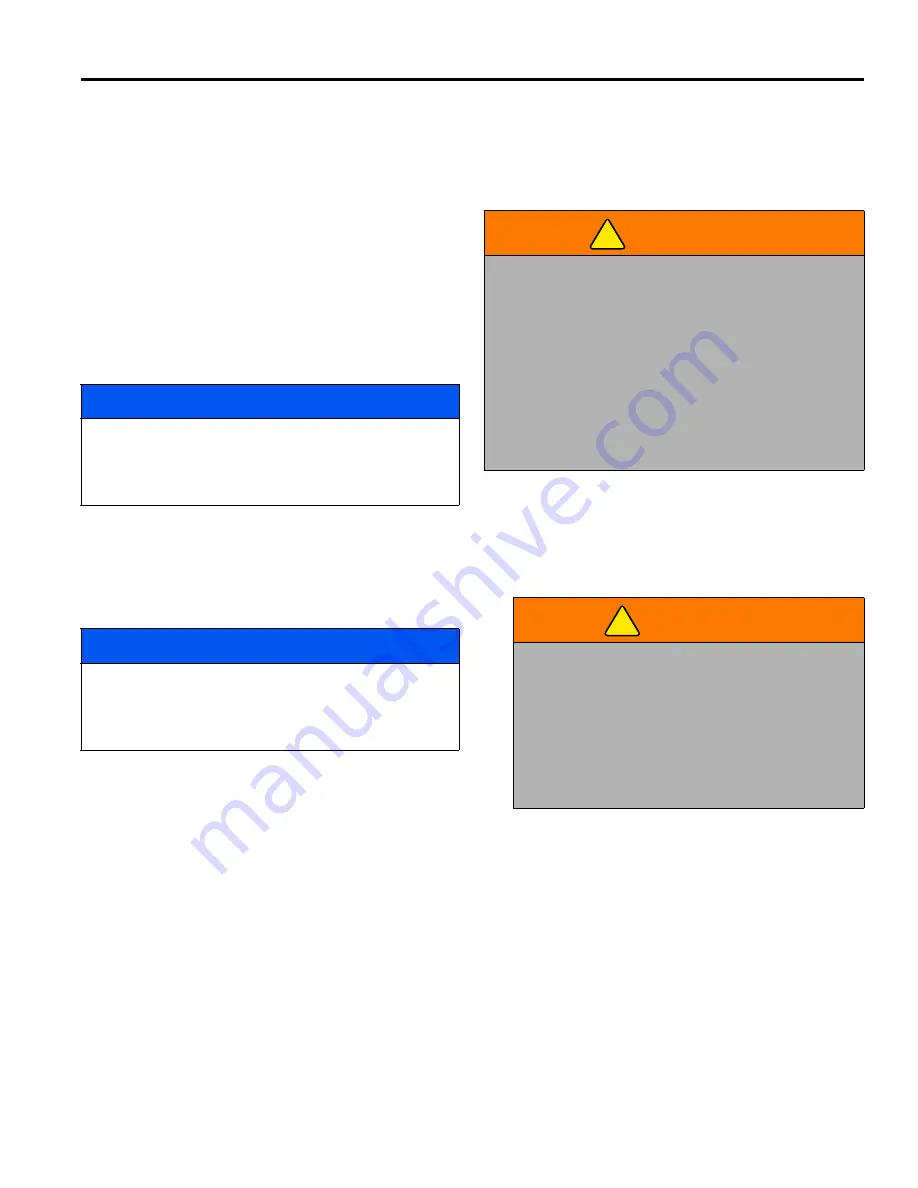
OPERATION 6
23
6.10 DAILY MAINTENANCE______________________________________________________
Important:
For more detailed maintenance information,
adjustments, and maintenance/lubrication charts, see
the
Parts & Maintenance
manual.
1.
Park the mower on a flat, level surface. Fully lower
the implements to the ground, engage parking brake,
stop the engine, and remove key from ignition switch.
2.
Grease and lubricate all points if required. To
prevent fires, wash the cutting units and mower after
each use.
a.
Use only fresh water for cleaning your
equipment.
b.
Do not use high pressure spray.
c.
Do not spray water directly at the instrument
panel, or any electrical components.
d.
Do not spray water into the cooling air intake or
the engine air intake.
FUEL
Fill mower’s fuel tank at the end of each operating day to
full mark on fuel gauge.
Always use clean, fresh, #2 low or ultra low sulfur
diesel fuel. Minimum Cetane Rating 45.
Handle fuel with care - it is highly flammable.
Use an
approved container; the spout must fit inside the fuel filler
neck. Avoid using cans and funnels to transfer fuel.
• Store fuel according to local, state, or federal ordinances
and recommendations from your fuel supplier.
• Never overfill or allow the tank to become empty.
HYDRAULIC HOSE, OIL, AND FILTER
1.
Inspect hydraulic hoses and tubes daily. Look for wet
hoses or oil spots and replace worn or damaged
hoses and tubes before operating the machine.
2.
Check the engine oil and hydraulic oil at the start of
each day, before starting the engine. If the oil level
is low, remove the oil filler cap, and add oil as
required. Do not overfill.
NOTICE
Use of salt water or effluent water has been known to
encourage rust and corrosion of metal parts resulting
in premature deterioration or failure. Damage of this
nature is not covered by the factory warranty.
NOTICE
Do not wash a hot or running engine. Use
compressed air to clean the mower, engine, and
radiator fins to reduce the potential for corrosion and
moisture contamination.
WARNING
Never remove the fuel cap from the fuel tank, or add fuel,
when the engine is running or while the engine is hot.
Do not smoke when handling fuel. Never fill or drain the
fuel tank indoors.
Do not spill fuel. Clean spilled fuel immediately.
Never handle or store fuel containers near an open flame
or any device that may create sparks and ignite the fuel
or fuel vapors.
Be sure to reinstall and tighten fuel cap securely.
WARNING
To prevent serious injury from hot, high pressure
oil, never use your hands to check for oil leaks;
use paper or cardboard.
Hydraulic fluid escaping under pressure can have
sufficient force to penetrate skin. If fluid is injected
into the skin, it must be surgically removed within
a few hours by a doctor familiar with this form of
injury or gangrene may result.
!
!
Summary of Contents for Super LF 1880 67955
Page 53: ...NOTES 12 53 12 NOTES...