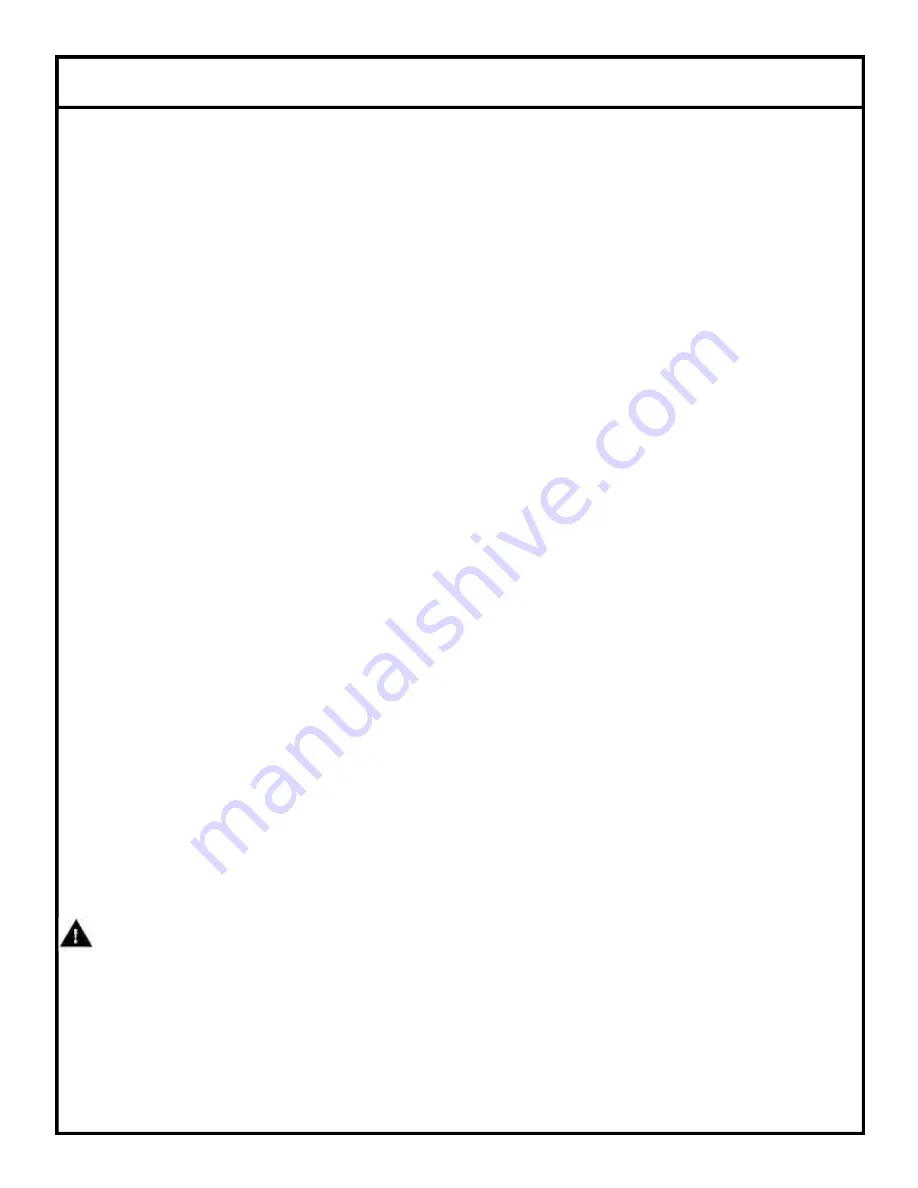
2
Jackson MSC Inc. provides technical support for all of the dishmachines detailed in this manual. We strongly recommend that you refer
to this manual before making a call to our technical support staff. Please have this manual with you when you call so that our staff can
refer you, if necessary, to the proper page. Technical support is available from 8:00 a.m. to 5:00 p.m. (EST), Monday through Friday.
Technical support is not available on holidays. Contact technical support toll free at 1-888-800-5672. Please remember that technical
support is available for service personnel only.
VISUAL INSPECTION:
Before installing the unit, check the container and machine for damage. A damaged container is an indicator
that there may be some damage to the machine. If there is damage to both the container and machine, do not throw away the con-
tainer. The dishmachine has been inspected and packed at the factory and is expected to arrive to you in new, undamaged condition.
However, rough handling by carriers or others may result in there being damage to the unit while in transit. If such a situation occurs,
do not return the unit to Jackson; instead, contact the carrier and ask them to send a representative to the site to inspect the damage
to the unit and to complete an inspection report. You must contact the carrier within 48 hours of receiving the machine. Also, contact
the dealer through which you purchased the unit.
UNPACKING THE DISHMACHINE:
Once the machine has been removed from the container, ensure that there are no missing parts
from the machine. This may not be obvious at first. If it is discovered that an item is missing, contact Jackson immediately to have the
missing item shipped to you.
LEVEL THE DISHMACHINE:
The dishmachine is designed to operate while being level. This is important to prevent any damage to
the machine during operation and to ensure the best results when washing ware. The unit comes with adjustable bullet feet, which can
be turned using a pair of channel locks or by hand if the unit can be raised safely. Ensure that the unit is level from side to side and
from front to back before making any connections.
PLUMBING THE DISHMACHINE:
All plumbing connections must comply with all applicable local, state, and national plumbing codes.
The plumber is responsible for ensuring that the incoming water line is thoroughly flushed prior to connecting it to any component of
the dishmachine. It is necessary to remove all foreign debris from the water line that may potentially get trapped in the valves or cause
an obstruction. Any valves that are fouled as a result of foreign matter left in the water line, and any expenses resulting from this foul-
ing, are not the responsibility of the manufacturer.
CONNECTING THE DRAIN LINE:
The Conserver 24 series machines are a pumped (pressure) drain capable of pumping waste water
to a height of 24 inches from the floor to the kitchen’s drain system. The dishmachines are supplied with a 10 foot long hose that extends
from the rear side of the machine. There must also be an air gap between the machine drain line and the floor sink or drain. If a grease
trap is required by code, it should have a flow capacity of 5 gallons per minute.
WATER SUPPLY CONNECTION:
Ensure that you have read the section entitled “PLUMBING THE DISHMACHINE” above before pro-
ceeding. Install the water supply line (1/2” pipe size minimum) to the dishmachine line strainer using copper pipe. It is recommended
that a water shut-off valve be installed in the water line between the main supply and the machine to allow access for service. The water
supply line is to be capable of 20
A
5 PSI “flow” pressure at the recommended temperature indicated on the data plate.
Do to areas where the water pressure fluctuates or is greater than the recommended pressure, it is recommended installing supplied
water pressure regulator. Do not confuse static pressure with flow pressure. Static pressure is the line pressure in a “no flow” condition
(all valves and services are closed). Flow pressure is the pressure in the fill line when the fill valve is opened during the cycle.
It is also recommended that a shock absorber (not supplied with the Conserver 24 series models) be installed in the incoming water
line. This prevents line hammer (hydraulic shock), induced by the solenoid valve as it operates, from causing damage to the equipment.
PLUMBING CHECK:
Slowly turn on the water supply to the machine after the incoming fill line and the drain line have been installed.
Check for any leaks and repair as required. All leaks must be repaired prior to placing the machine in operation.
This equipment is not recommend for use with deionized water or other aggressive fluids. Use of deionized water or
other aggressive fluids will result in corrosion and failure of materials and components. Use of deionized water or other
aggressive fluids will void the manufacturer's warranty.
INSTALLATION INSTRUCTIONS