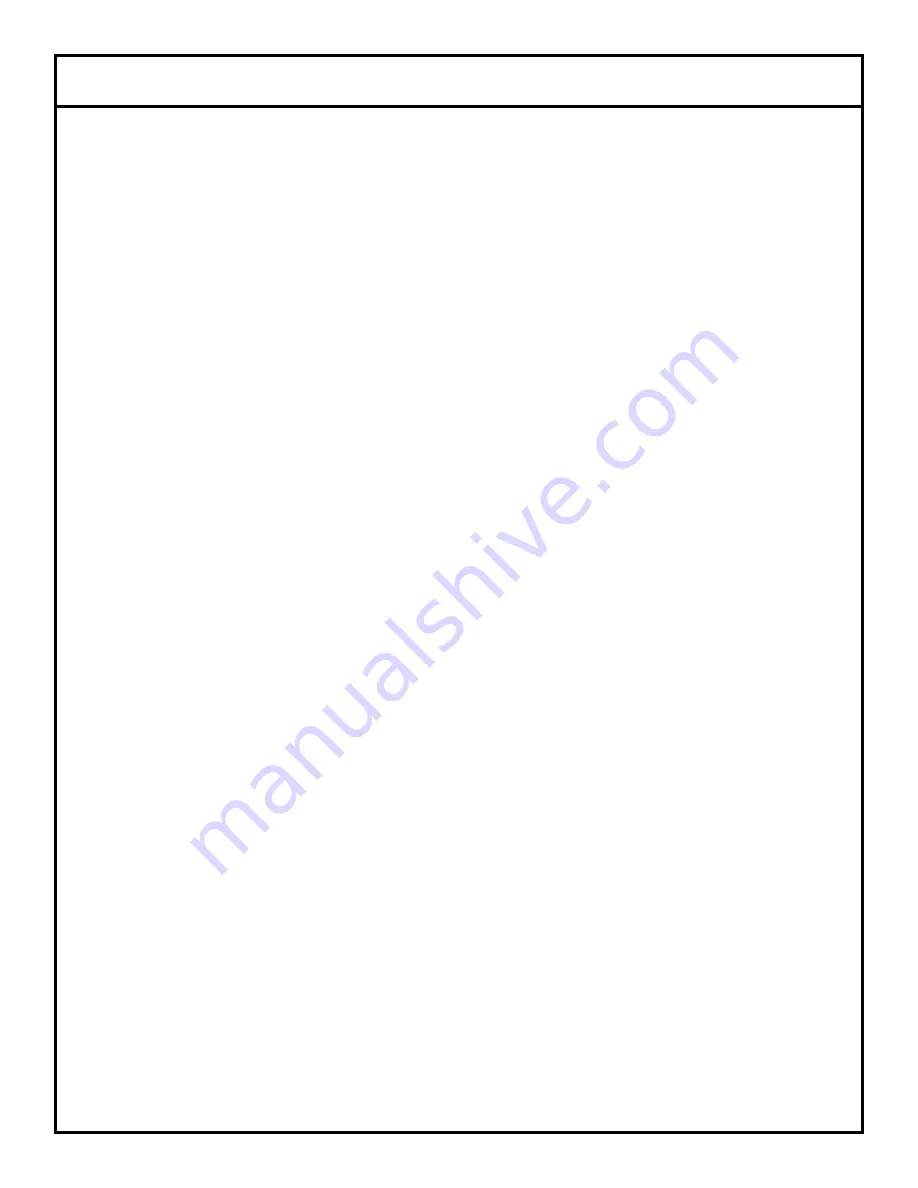
VISUAL INSPECTION:
Before installing the unit, check the con-
tainer and the machine for any damage. A damaged container
could be an indication of damage to the unit. If there is damage to
both the container and the unit, DO NOT throw away the contain-
er. The dishmachine has been inspected and packed at the facto-
ry with the expectation that it will arrive to you in new, undamaged
condition. However, rough handling by carriers or others may
damage the unit while in transit. If this situation does occur, do not
return the unit to Jackson; instead contact the carrier and ask
them to inspect the damage to the unit and to complete an
inspection report. You must contact the carrier within 48 hours of
receiving the machine. Also, contact the dealer you purchased the
machine through.
UNPACKING THE DISHMACHINE:
Remove the machine from
the container and inspect for any missing parts. If an item appears
to be missing, contact Jackson immediately to report it.
LEVEL THE DISHMACHINE:
The dishmachine(s) covered in this
manual are designed to operate on a level surface. Ensure that
the machine is level from side to side and from front to back;
adjust the unit’s bullet feet as required. Failure to level the dish-
machine may cause decreased washing performance.
PLUMBING THE DISHMACHINE:
All plumbing connections must
comply with all applicable local, state and national plumbing
codes. The plumber is responsible for flushing the incoming water
line prior to connecting it to remove all foreign debris that may get
trapped in the valves or cause an obstruction. Any valves that are
fouled by matter left in the water line and the expenses resulting
are not the responsibility of the manufacturer.
CONNECTING THE DRAIN LINE:
The Delta 5 drain requires a
minimum 2” IPS piping that is pitched at least 1/4” per foot. There
must also be an air gap between the machine drain line and the
floor sink or drain. If a grease trap is required by code, it should
have a flow capacity of 5 gallons per minute.
WATER SUPPLY CONNECTION:
Install the water supply line
(1/2” IPS minimum) to the dishmachine line strainer using copper
pipe. It is recommended that a water shut-off valve be installed
between the main supply and the machine to allow for service.
The water supply line must be capable of 20 PSI “flow” pressure
at the recommended temperature as indicated on the data plate.
In areas where the water pressure fluctuates or is greater than the
recommended pressure, it is suggested that a water pressure reg-
ulator be installed. The Delta 5 does not come with a water pres-
sure regulator as standard equipment.
It is also recommended that a shock absorber (not supplied with
the Delta 5) be installed in the incoming water line. This prevents
line hammer (hydraulic shock), induced by the solenoid valve,
which can cause damage to the equipment.
PLUMBING CHECK:
Slowly turn on the water supply to the
machine after connecting the incoming fill line and drain line.
Check for leaks and repair as required. Leaks must be repaired
prior to placing the machine in operation.
ELECTRICAL POWER CONNECTION:
Electrical and grounding
connections must comply with all applicable portions of the
National Electric Code (ANSI/NFPA 70) and/or other electrical
codes that may apply.
Disconnect the electrical power supply and place a safety tag at
the disconnect switch to indicate that you are working on the cir-
cuit.
The dishmachine data plate is located on the left front corner of
the machine. Refer to this data plate for information concerning
the unit’s specific electrical requirements.
To install the incoming power lines, open the connection box by
removing the connection box lid. Install 1/2” coduit into the pre-
punched holes in the back of the connection box. Route the power
wires and connect to the power block and grounding lug. Install
the service wires (L1 and N) to the appropriate terminals as they
are marked on the terminal block. Install the grounding wire into
the lug provided. Wires should be firmly secured in place.
It is recommended that “De-Ox” or another similar anti-oxidation
agent be used on all voltage connections.
VOLTAGE CHECK:
Ensure that the machine is off and apply
power to the machine. Check the incoming power at the terminal
block and ensure it corresponds to the voltage on the machine
data plate. Do not run the dishmachine if the voltage is too high or
too low. Shut off the service breaker and mark it as being for the
dishmachine. Advise all personnel of the location of the service
breaker. Replace all covers and tighten the screws.
INSTALLATION INSTRUCTIONS
2