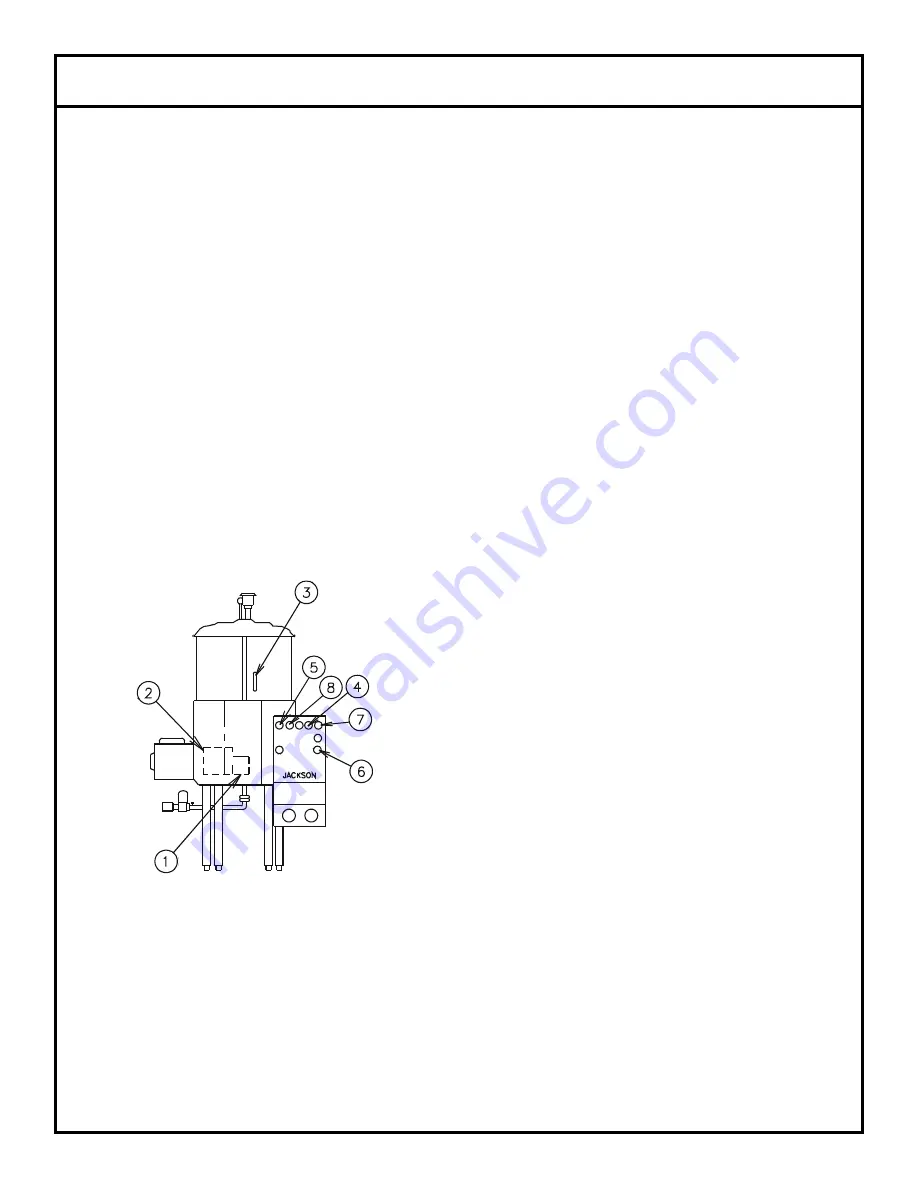
PREPARATION:
1. Ensure that the pump intake strainer (1) and basket overflow
strainer (2) are inserted and tight.
2. Ensure that the wash and rinse arms are installed and secure.
3. Remove all solid wastes in order to avoid obstructing filters,
drain and wash and rinse arms.
4. Ware that is encrusted with soil should be presoaked prior to
being placed in the machine.
5. When placing dishes into the racks, do not allow them to lean
on each other.
6. Place the glasses upside down in the open rack. With the model
10 series, a four compartment silverware rack is supplied. Place
silver in compartment rack loosely not allowing it to mix with other
silverware of the same nature. Place the compartment rack in the
open rack and wash with the cups and glasses.
DAILY MACHINE PREPARATION:
Refer to the section entitled
“PREPARATION” at the top of this page and follow the instructions
there. Afterwards, check that all of the chemical levels are correct
and/or that there is plenty of detergent available for the expected
workload.
WARM-UP CYCLE:
At the beginning of each work day, a warm up
cycle will need to be performed. Close the hood (3). Turn on the
master switch (4). Raise the fill switch (5) until the machine is filled
to the top of the basket overflow strainer (2.) Once the proper
water level has been reached, turn on the heater switch (6).
Observe the temperature gauges, the rinse temperature should
rise to a specified level of 180°F within five minutes if the incom-
ing water to the booster tank is 140°F. The wash heater will take
longer to reach 150°F as the element is designed for maintaining
temperature, not heating. Once the proper temperature has been
reached, with the hood closed, turn on the manual wash switch.
You should hear the water being pumped as it strikes the top of
the hood. Turn off the manual wash switch. The dishmachine is
now ready to proceed with washing of the dishes.
WARE PREPARATION:
Proper preparation of ware will help
ensure good results and less re-washes. If not done properly,
ware may not come out clean and the efficiency of the dishma-
chine will be reduced. It is important to remember that a dishma-
chine is not a garbage disposal and that throwing unscraped dish-
es into the machine will defeat the purpose altogether of washing
the ware. Scraps should be removed from ware prior to being
loaded into a rack. Pre-rinsing and pre-soaking are good ideas,
especially for silverware and casserole dishes. Place cups and
glasses upside down in racks so that they do not hold water dur-
ing the cycle. The dishmachine is meant not only to clean, but to
sanitize as well, to destroy all of the bacteria that could be harm-
ful to human beings. In order to do this, ware must be properly
prepared prior to being placed in the machine.
WASHING A RACK OF WARE:
To wash a rack, open the hood
completely (being careful for hot water that may drip from the top
of the hood), manually load detergent into the wash chamber, or if
automatic detergent dispenser is used, follow the manufacturers
instructions. Slide the rack of dishes into the dishmachine. Close
the hood. Start the automatic wash and rinse cycle of the dishma-
chine by flipping the start switch (7) either up or down (NOTE: The
start switch, is a three position switch. Up = Start, Center = Off,
Down = Start) the indicating light (8) will come on at the start of the
cycle. When the light goes off, the cycle is complete. Open the
hood, remove the rack of clean dishes to air dry. Repeat the cycle
by adding another rack of soiled dishes, adding the detergent,
close hood and flip start switch (8) in opposite direction.
SHUT DOWN AND CLEANING:
At the end of meal time, shut off
the dishmachine by placing the start switch in center position and
turn heat switch off. Drain the dishmachine by removing the over-
flow strainer. Remove the pump intake strainer after water has
drained. Clean both strainers. Clean the inside of the unit. Clean
wash head, upper and lower rinse arms and replace the clean
strainers. Replace all removed parts. The machine is now ready
for refilling and operation.
OPERATION INSTRUCTIONS
4
Summary of Contents for 10A
Page 41: ...HOOD AND ASSOCIATED ASSEMBLIES 39 2 1 3 14 15 16 17 18 19 5 4 11 12 13 9 10 20 7 8 6 5 4...
Page 49: ...10A 208 230 VOLT 60 HERTZ 1PHASE WIRING DIAGRAM 47...
Page 50: ...10AB 208 230 VOLT 60 HERTZ 1PHASE WIRING DIAGRAM 48 9905 000 54 97...
Page 51: ...10AB 208 230 VOLT 60 HERTZ 3PHASE WIRING DIAGRAM 49 9905 002 55 90a...
Page 52: ...10APRB 208 230 VOLT 60 HERTZ 1PHASE WIRING DIAGRAM 50 9905 002 55 91a...
Page 53: ...10APRB 208 230 VOLT 60 HERTZ 3PHASE WIRING DIAGRAM 51 9905 002 55 92a...