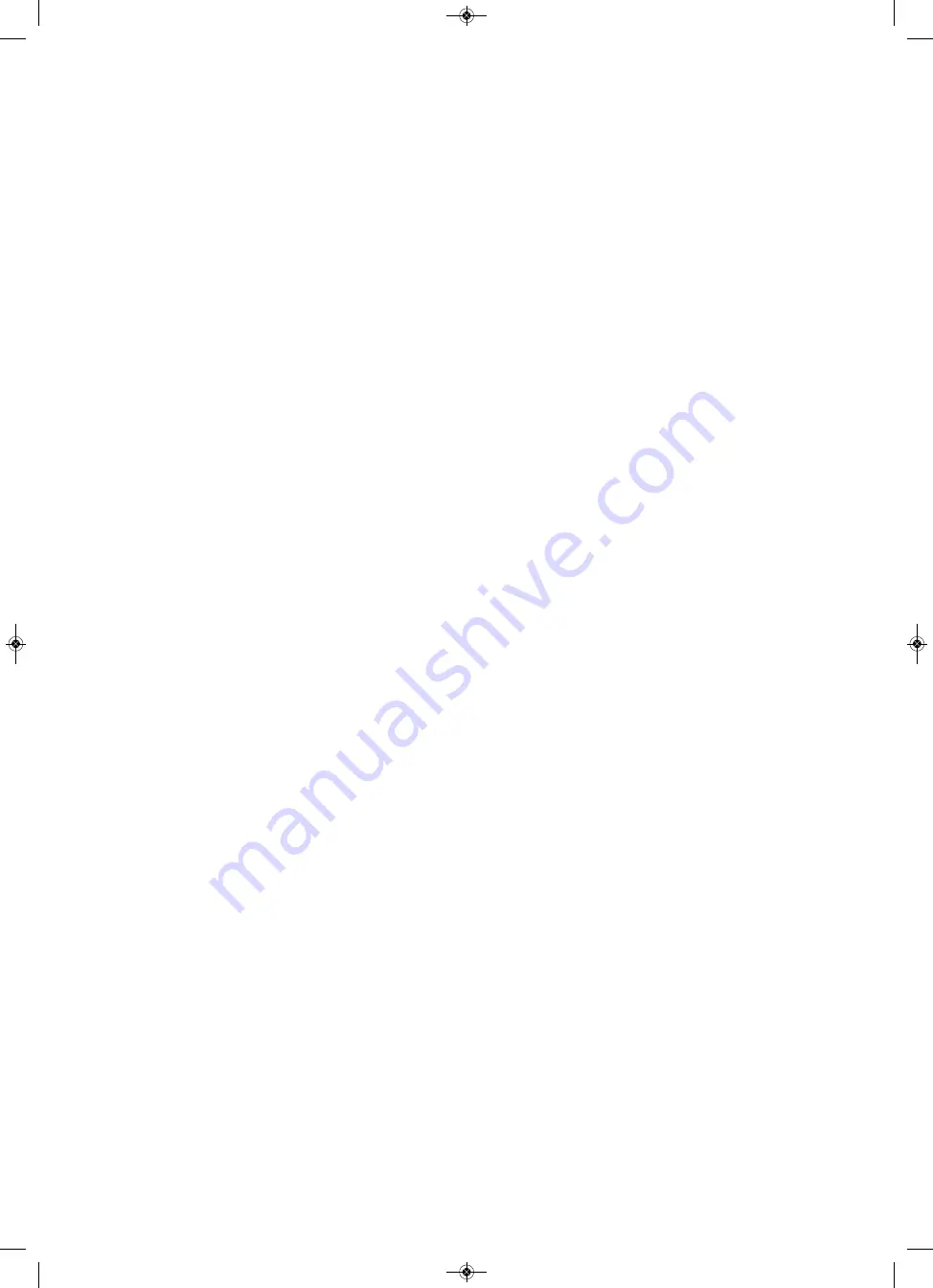
6. Insert screwdriver between OD of outer bearing
seal and pump bore and pry out seal.
7. Remove bearing to body retaining ring.
8. Press on impeller drive end of shaft to remove
shaft and bearing assembly. Heating outside of
body at bearing will ease disassembly.
9. Remove bearing-to-shaft retaining ring.
10. Supporting bearing inner race, press shaft
through bearing.
11. using extreme care not to mar bore, insert
screwdriver between OD of inner seal and pump
bore and pry out the seal.
NOTE: Inspect all parts for wear or damage and
replace if necessary.
ASSEMBLY
1. Lubricate inner seal with grease and press into
body bearing seal bore with lip facing away from
bearing bore.
2. Press shaft into bearing, using care to support
inner race of bearing.
3. Install bearing-to-shaft retaining ring with flat side
toward bearing.
4. Position slinger in body drain area on 6400-
Series pumps only. Insert splined end of shaft
through bearing bore and guide slinger over shaft
until bearing contacts body.
5. Pressing on bearing outer race, install bearing
and shaft assembly into bore.
6. Install bearing to body retaining ring in body
groove with flat side toward bearing.
7. Lubricate outer bearing seal with grease and
press into bearing bore until it is flush with the
body.
8. Install wearplate in body bore, aligning slot in
wearplate with dowel pin in body.
9. Apply a thin coat of sealant to cam screw threads
and top side of cam and install in body.
10. Lubricate seal seat assembly with water and insert
in seal bore of body with polished surface facing
outward. Care must be taken not to mar or scratch
seal seat face. Installing this assembly with a
slight rotary motion will insure seating the gasket
firmly in the cavity.
11. Slide carbon ring assembly, with carbon facing
ceramic, over the shaft and firmly up against the
ceramic seat.
12. Slide O-ring onto shaft and position in the O-ring
groove at the base of the spline (-10XX series
pumps only).
13. Lubricate impeller bore with a light coat of water
pump grease and start impeller into bore with a
rotary motion until splines engage, then push into
bore.
14. Install gasket and end cover and secure with end
cover screws.
OPERATING INSTRuCTIONS (Continued)
3. SPEEDS - 100 RPM to the maximum shown in the
performance table. For longer pump life, operate
at lowest possible speeds.
4. SELF-PRIMING - Primes at low or high speeds.
For vertical dry suction lift of 10 feet, (3.1m) a min-
imum of 800 RPM is required. Pump will produce
suction lifts up to 22 (6.7m) feet when wetted. BE
SuRE SuCTION LINES ARE AIRTIGHT.
5. RuNNING DRY - unit depends on liquid pumped
for lubrication.DO NOT RuN DRY for more than 30
seconds. Lack of liquid will damage the impeller.
6. NOTICE – If pumping light fraction petroleum
derivatives, solvents, thinners, highly con-
centrated or organic acids, consult Jabsco
“Chemical Resistance Table” (which is available
upon request from Jabsco) for proper body
materials and impeller compounds. If corrosive flu-
ids are handled, pump life will be prolonged if
pump is flushed with water after each use or after
each work day.
7. PRESSuRES – For continuous operation,
pressure should not exceed 30 psi (2.1 kg/sq cm).
For intermittent service only, pressures from 35 to
50 psi (2.5 – 3.5 kg/sq cm) can be attained using
807-1001 impeller, plus an extra gasket.
8. TEMPERATuRES –
Neoprene: 45°-180° F (7°-82° C)
Nitrile: 50°-180° F (10°-82° C)
Natural Rubber: 33°-120° F (0.6°-49° C)
9. FREEZING TEMPERATuRES – Drain unit by
loosening end cover. The following anti-freeze
compounds can be used without any adverse
effect to the neoprene impeller: Atlas
“Permaguard”, DuPont “Zerex” and “Telar”, Dow
Chemical “Downguard” and Olin Mathison “Pyro”.
Most methyl alcohol (methanol) based anti-
freezes can be used. DO NOT uSE PETROLEuM
BASED ANTI-FREEZE COMPOuNDS OR RuST
INHIBITORS.
10. GASKET – use standard pump part. A thicker
gasket will reduce priming ability. A thinner gas-
ket will cause impeller to bind. Standard gasket
is 0.015" thick.
11. SPARE PARTS – To avoid costly shut downs,
keep a Jabsco Service Kit on hand.
SERVICE INSTRuCTIONS
DISASSEMBLY
1. Remove end cover screws, end cover and gasket.
2. Remove impeller (and O-ring on -10XX pumps
only).
3. Remove seal with hooked wire. Remove seal seat
and gasket.
4. Loosen cam screw and remove cam. Clean off
sealant.
5. Remove wearplate.
43000-0011_C-102012_0011 (6400 & 7420-Series Bronze Ped Pumps).qxd 10/4/12 4:55 PM Page 2