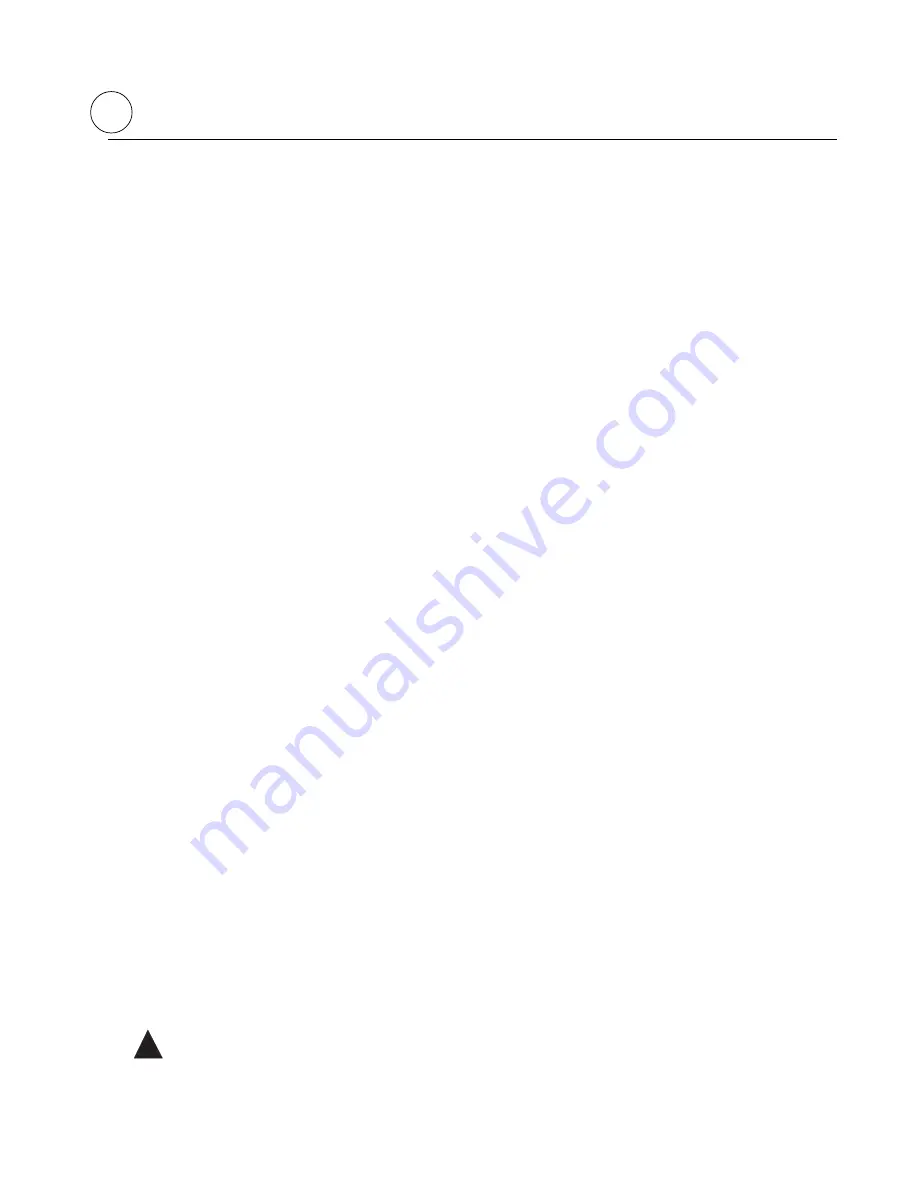
5
n
4
Handling
1. Dry run operation, unless using a "-D" model
Dry run operation of the pump may cause damage to the pump internally. The internal bushings used in
the MDH-(F) series pump are lubricated and cooled by the fluid being pumped. If the pump is unavoid-
ably or accidentally operated dry, with no obvious damage, allow the pump to cool down for a minimum
of one hour before attempting to restart. Do not allow fluid to enter the pump cavity until the pump has
cooled down. Sudden or rapid introduction of a cold fluid may cause damage to the bearing system. A dry
run protection device is recommended for the prevention of damage when dry pump operation is antici-
pated.
"-D" Models
Most MDH-(F) models are designed to tolerate brief or intermittent dry run operation, they are identified
by a "-D" at the end of the model number. These models can tolerate dry run conditions for up to one
hour. Longer dry run periods, or frequent dry running may result in premature wear of the bearing sur-
faces. This can rapidly affect the standard clearances of the rotating elements inside the pump. These
pumps are designed to reduce the likelihood of cracking resulting from sudden cooling with liquid imme-
diately after dry run operation. However, to ensure that this does not occur, Iwaki Walchem recommends
that the pump be allowed to cool for at least 20 minutes after dry running before introducing fluid again.
"-E" Models
Pumps identified with "E" at the end of the model identification cannot endure dry running opera-
tion.
2. Starting and Stopping
Pay close attention to the following points to avoid water hammer upon starting and stopping pump
operation. Extra attention is required when the discharge piping is very long.
Starting
Prior to starting the pump, make sure that the power is turned off. Then carry out priming to fill the
pump cavity with liquid. Close the cocks of any pressure or vacuum gauges to prevent damage from
sudden pressure changes. Open only when taking measurements.
Next, close the valve on the discharge side. Now you can turn the power on and start up the pump.
Run the motor momentarily to check the direction of motor rotation. The motor should run in the
direction indicated by the arrow sealed on the pump. If the direction is reversed, exchange two wires of
the three-phase power wires. When the pump has reached full speed and line pressure is stable, the
discharge valve can be opened until the desired pressure setting is obtained.
Stopping
When stopping the pump, first close the discharge valve gradually. When it is completely closed, turn
off the power switch so that the pump stops. Never stop the pump suddenly by quickly closing a valve
(i.e., solenoid or hydraulic valves).
Caution
Quick valve closure may cause water hammer which may result in severe damage to the pump.
!