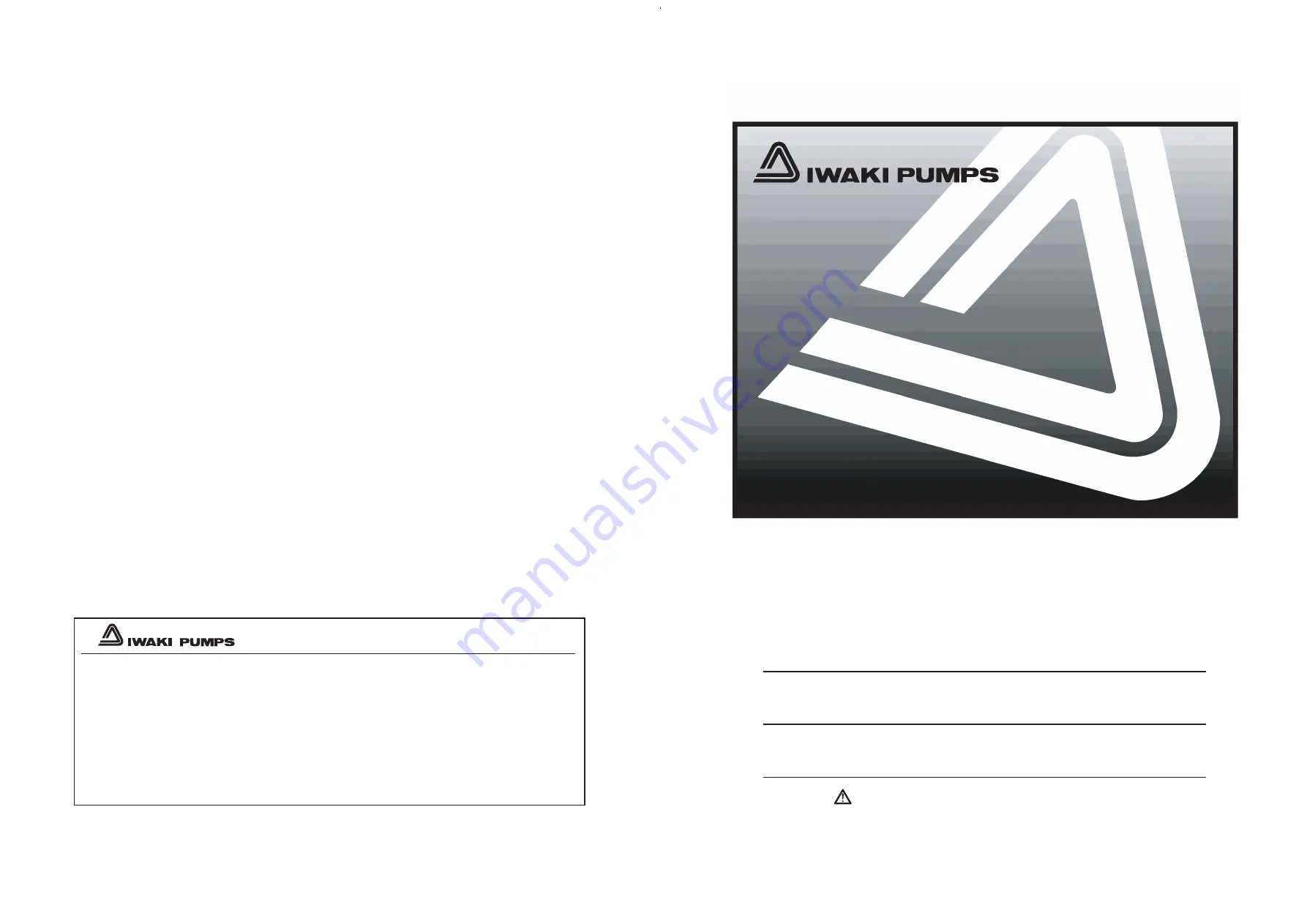
Read this manual before use of product
IWAKI Magnetic Drive Pump
MX-F250/-F403 (Asia Edition)
Instruction Manual
T496-8 '15/07
http://www.iwakipumps.jp
IWAKI CO.,LTD. 6-6 Kanda-Sudacho 2-chome Chiyoda-ku Tokyo 101-8558 Japan
TEL: +81 3 3254 2935 FAX: +81 3 3252 8892
European office
/ IWAKI Europe GmbH
TEL: +49 2154 9254 0 FAX: +49 2154 9254 48
Norway
/ IWAKI Norge AS
TEL: +47 23 38 49 00 FAX: +47 23 38 49 01
Australia
/ IWAKI Pumps Australia Pty Ltd.
TEL: +61 2 9899 2411 FAX: +61 2 9899 2421
Germany
/ IWAKI Europe GmbH
TEL: +49 2154 9254 50 FAX: +49 2154 9254 55
Sweden
/ IWAKI Sverige AB
TEL: +46 8 511 72900 FAX: +46 8 511 72922
China
(Hong Kong) / IWAKI Pumps Co., Ltd.
TEL: +852 2607 1168 FAX: +852 2607 1000
Holland
/ IWAKI Europe GmbH (Netherlands Branch)
TEL: +31 74 2420011 FAX: +49 2154 9254 48
U.K.
/ IWAKI Pumps (U.K.) LTD.
TEL: +44 1743 231363 FAX: +44 1743 366507
China
(Guangzhou) / GFTZ IWAKI Engineering & Trading Co., Ltd.
TEL: +86 20 84350603 FAX: +86 20 84359181
Italy
/ IWAKI Europe GmbH (Italy Branch)
TEL: +39 0444 371115 FAX: +39 0444 335350
U.S.A.
/ IWAKI America Inc.
TEL: +1 508 429 1440 FAX: +1 508 429 1386
China
/ IWAKI Pumps (Shanghai) Co., Ltd.
TEL: +86 21 6272 7502 FAX: +86 21 6272 6929
Spain
/ IWAKI Europe GmbH (Spain Branch)
TEL: +34 93 37 70 198 FAX: +34 93 47 40 991
Argentina
/ IWAKI America Inc. (Argentina Branch)
TEL: +54 11 4745 4116
Korea
/ IWAKI Korea Co., Ltd.
TEL: +82 2 2630 4800 FAX: +82 2 2630 4801
Belgium
/ IWAKI Belgium N.V.
TEL: +32 13 670200 FAX: FAX: +32 13 672030
Singapore
/ IWAKI Singapore Pte Ltd.
TEL: +65 6316 2028 FAX: +65 6316 3221
Taiwan
/ IWAKI Pumps Taiwan Co., Ltd.
TEL: +886 2 8227 6900 FAX: +886 2 8227 6818
Denmark
/ IWAKI Nordic A/S
TEL: +45 48 242345 FAX: +45 48 242346
Indonesia
/ IWAKI Singapore (Indonesia Branch)
TEL: +62 21 6906606 FAX: +62 21 6906612
Thailand
/ IWAKI (Thailand) Co., Ltd.
TEL: +66 2 322 2471 FAX: +66 2 322 2477
Finland
/ IWAKI Suomi Oy
TEL: +358 9 2745810 FAX: +358 9 2742715
Malaysia
/ IWAKIm SDN. BHD.
TEL: +60 3 7803 8807 FAX: +60 3 7803 4800
Vietnam
/ IWAKI Pumps Vietnam Co., Ltd.
TEL: +84 613 933456 FAX: +84 613 933399
France
/ IWAKI France S.A.
TEL: +33 1 69 63 33 70 FAX: +33 1 64 49 92 73