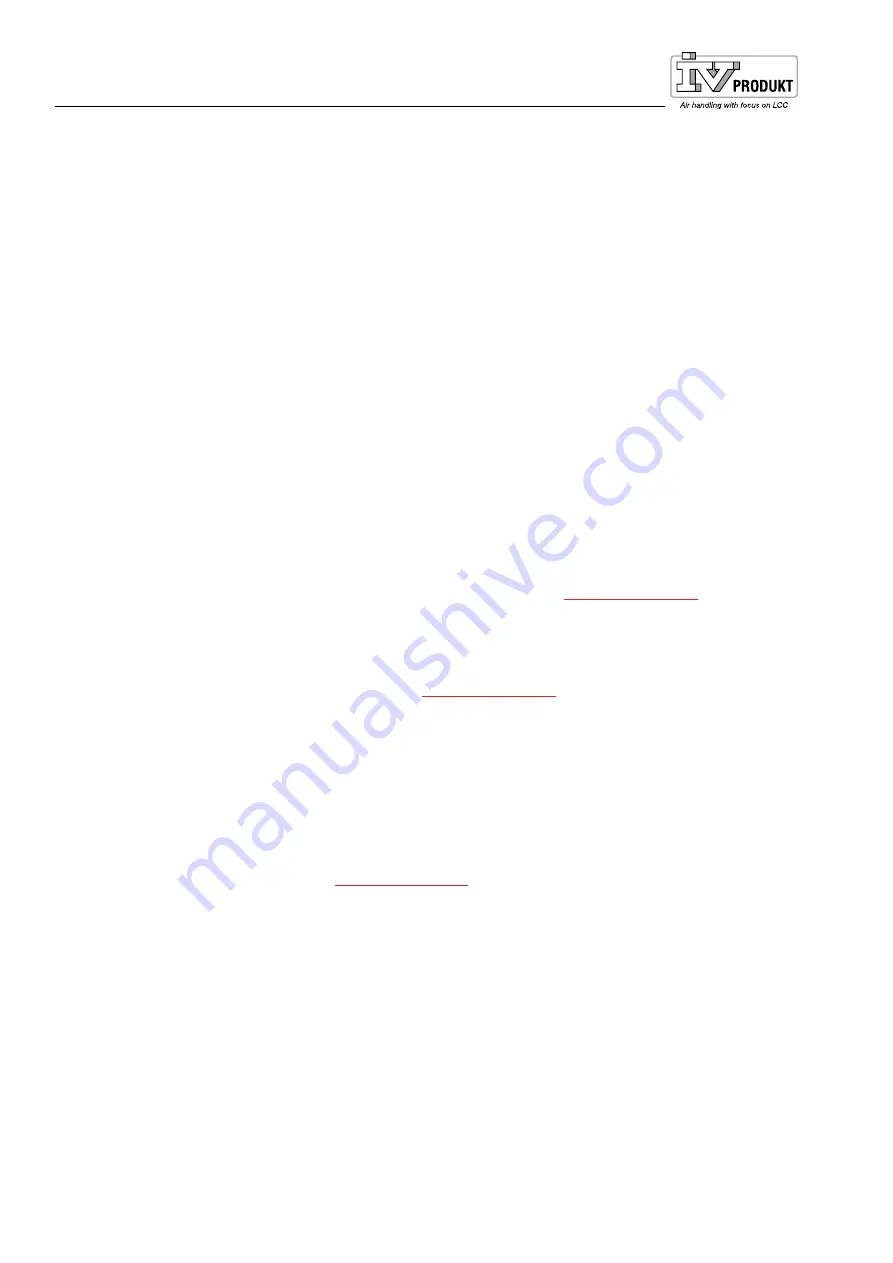
Page 10
Operation and maintenance
Envistar Compact
DSEC181201.00.EN
Continuous product development may give rise to specification changes without notice.
5 Wiring instructions and fuse protection
5.1 MX – Complete control equipment and UC – Complete electrical
connection to terminal (without DUC).
Applies to:
• units supplied prewired with complete, integrated Siemens Climatix control
equipment (code MX).
• units supplied without process unit (DUC) but with sensor and damper ac-
tuator connected electrically to the terminal (code UC). Fans and heat ex-
changers are fused and connected electrically to the terminal. The terminal
connections are positioned at a shared place in the unit. For further con-
nection to an external process unit, we recommend using a multi-conductor
cable.
Safety switch
A safety switch must be fitted and wired on each power supply.
Wiring diagrams
For wiring diagrams for units with integrated control equipment, refer to the order
unique wiring diagram supplied with the unit or
(Control
Diagram).
Unit functions, power supply and fuse protection
For power supply to the unit functions and recommended fuses, refer to Order
(Technical Data and Control
Diagram), or the product program IV Produkt Designer.
5.2 MK – Fans and heat exchangers electrically connected to terminal
For units supplied without control equipment but with fans and heat exchangers
connected electrically to terminals (code MK).
Connections to terminal blocks are located on each unit section.
For wiring instructions and recommended fuses, refer to Order Unique Docu-
mentation at
(Terminal Connection and Technical Data).
Safety switch
A safety switch must be fitted and wired on each power supply.
Summary of Contents for Envistar Compact Series
Page 2: ......