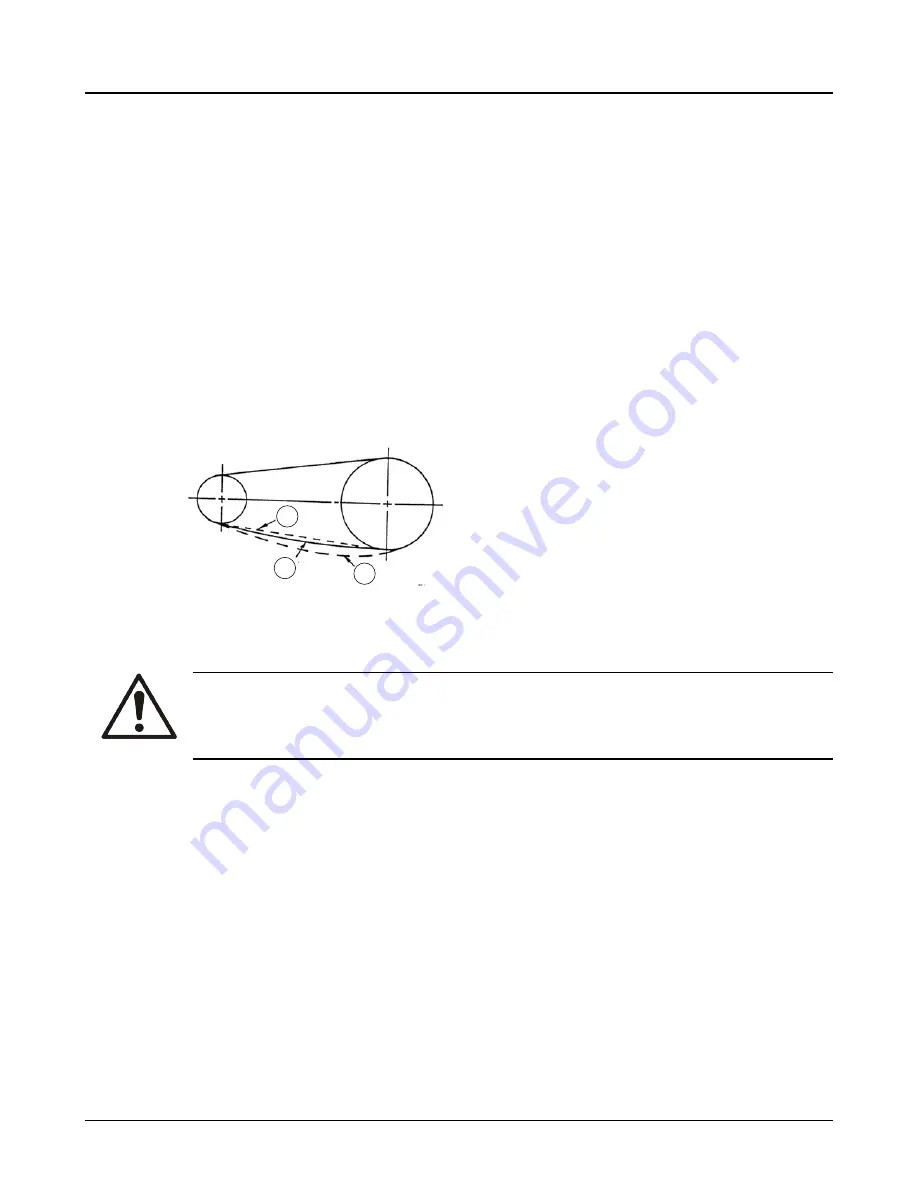
2.
Check Belt Fit -
Regardless of the belt section used, the belt should never be allowed to bottom
in the groove. This will cause the belts to lose their wedging action and slippage can occur.
Sheaves or belts that permit such a condition to occur should be changed.
3.
Maintain Proper Belt Tension -
Proper tension is essential for long belt life. Improper tension
could cause belt fatigue and/or hot bearings.
4.
Impeller Alignment after Belt Tensioning
– If the impeller was aligned prior to belt tensioning a
check should be made to determine that it is still centered. An off center impeller may rub and
cause unnecessary pump damage. Belt Tension will usually cause impeller misalignment oppo-
site the motor. Be sure to align or re-align in accordance with the
4.5 Impeller Alignment on page
The general method of tensioning belts is given below, and should satisfy most drive requirements.
General Method:
1.
Reduce the center distance so that the belts may be placed over the sheaves and in the grooves
without forcing them over the sides of the grooves. Arrange the belts so that both belt spans have
a proximately the same sag between the sheaves. Apply tension to the belts by increasing the
center distance until the belts are snug, see Figure:
Belt tensioning
.
1
2
3
1. Too tight
2. Slight bow
3. Too loose
Figure 13: Belt tension
WARNING:
Do not operate the pump without the proper drive guard in place. Failure to observe this warn-
ing could result in personal injury to operating personnel.
2.
Operate the drive a few minutes to seat the belts in the sheave grooves. Observe the operation
of the drive under its highest load condition (usually starting). A Slight bowing of the slack side of
the drive indicates proper tension. If the slack side remains taut during the peak load, the drive is
too tight. Excessive bowing or slippage indicates insufficient tension. If the belts squeal as the
motor begins operation or at some subsequent peak load, they are not tight enough to deliver the
torque demanded by the drive machine. The drive should be stopped and the belts tightened.
3.
Check the tension on a new drive frequently during the first day by observing the slack side span.
After a few days of operation the belts will seat themselves in the sheave grooves and it may be-
come necessary to readjust so that the drive again shows a slight bow in the slack side.
Other methods of determining proper belt tension can be obtained from the drive manufacturer.
4.
Use Belt Guards -
Belt guards protect personnel from danger and the drive from contamination.
Inspect periodically to assure that belts do not rub against guard.
5.
Keep Belts Clean -
Dirt and grease reduce belt life. An occasional wiping with a dry cloth to re-
move any build-up of a foreign material can extend the life of the belt. Should oil or grease splat-
ter onto the belts, clean with soap and water.
Belt dressing affects performance only temporarily and is never recommended. Maintaining a clean drive
is a better practice.
4.4 Drive Alignment Procedures
28
Model AF (42"/1200mm/54"/60"/66") LM/LMR Bearings Installation, Operation, and Maintenance Manual