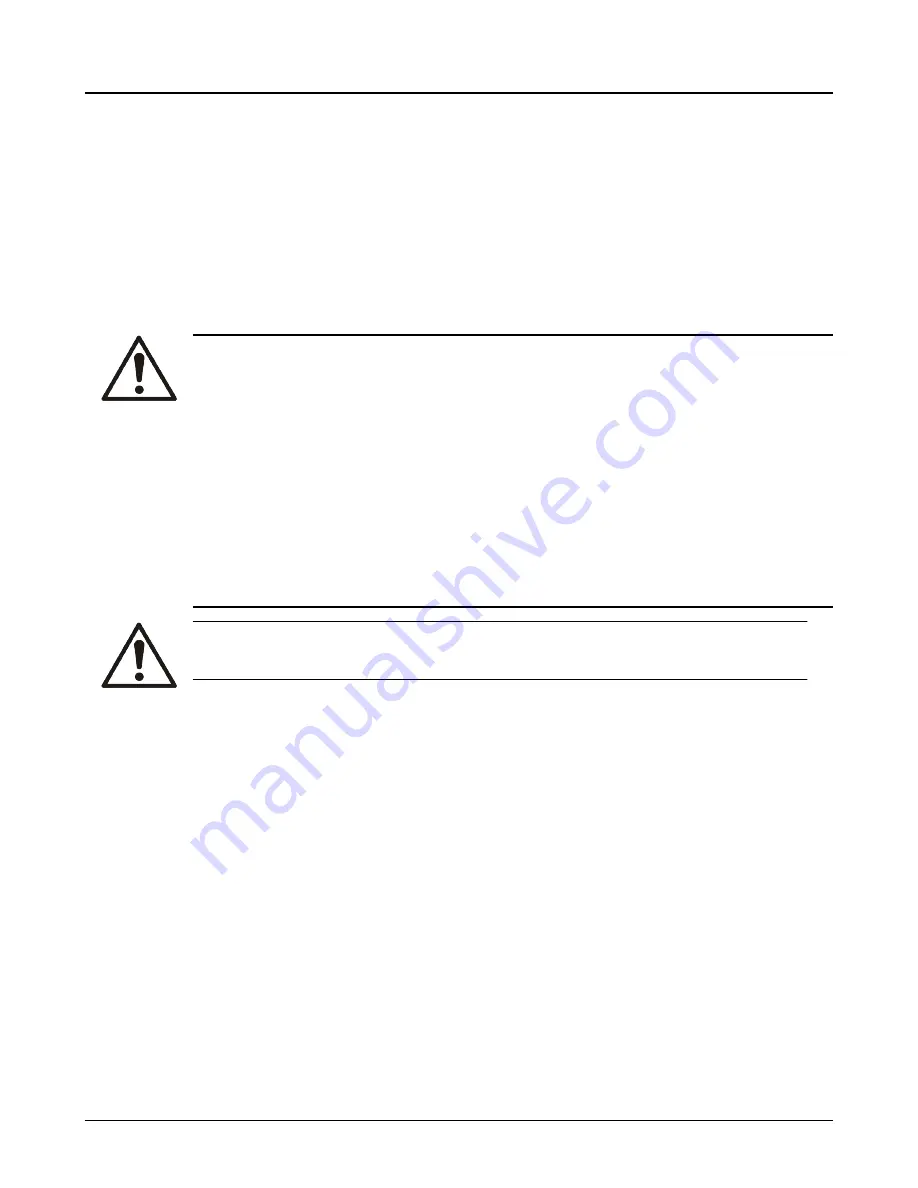
25. Tap the oil seal from the coupling end bearing end cover if replacement of seal is required. Refer
to
6.6 Inspection and Overhaul on page 61
for replacement sizes.
26. Slide the bearing housing off shaft.
27. Straighten "tang" in lock washer and remove bearing lock nut and washer.
28. Remove coupling end bearing using a bearing puller as shown in
. Care must be taken to prevent damage to bearings. Never use a hammer to drive shaft through
bearing. Protect bearing from contamination.
6.6 Inspection and Overhaul
Impeller
WARNING:
•
Risk of death or serious injury. Leaking fluid can cause fire and/or burns. Replace all gas-
kets and O-rings at each overhaul or disassembly.
•
Risk of death or serious injury. Leaking fluid can cause fire and/or burns. Inspect and en-
sure gasket sealing surfaces are not damaged and repair or replace as necessary.
•
Risk of serious personal injury or property damage. Fasteners such as bolts and nuts are
critical to the safe and reliable operation of the product. Ensure appropriate use of fasten-
ers during installation or reassembly of the unit.
•
Use fasteners of the proper size and material only.
•
Replace all corroded fasteners.
•
Ensure that all fasteners are properly tightened and that there are no missing fas-
teners.
CAUTION:
Risk of physical injury from sharp edges. Wear heavy work gloves when handling impellers.
Replace if impeller shows excessive erosion (especially on ejector vanes on back side of impeller), cor-
rosion, extreme wear or vane breakage. O-ring groove and impeller hub must be in good condition. Im-
peller has a push fit on shaft 0.000mm to 0.038mm | 0.000" to 0.0015" loose. Check impeller balance.
Sideplate
To maintain maximum efficiency, the clearance between sideplate and impeller should be 0.038mm |
0.015". Overall travel in casing is between 1.499mm and 2.159mm | 0.059" and 0.085". Sideplates
should be inspected for erosion, pitting or excessive wear. Replacement is required when distance be-
tween impeller and suction sideplate cannot be held to 0.038mm | 0.015" with the axial impeller adjust-
ment.
Shaft
Check for runout to see that the shaft is not bent. Bearing seats and oil seal areas must be in perfect
condition and free of scratches and grooves. O.D. and finish in these areas must be within bearing man-
ufacturer's specifications. Check that the keyway is free of corrosion. Replace shaft if necessary.
Shaft Sleeve
The shaft sleeve is a push fit and is bored: "S"- 0.000mm to 0.051mm | 0.000'' to 0.002"; "M" & "L" -
0.025mm to 0.076mm | 0.001" to 0.003" larger than the shaft and should tap easily on the shaft. If the
sleeve does not tap on easily, the bore and shaft should be inspected to see that they are free from
6.6 Inspection and Overhaul
3175 Installation, Operation and Maintenance Instructions
61