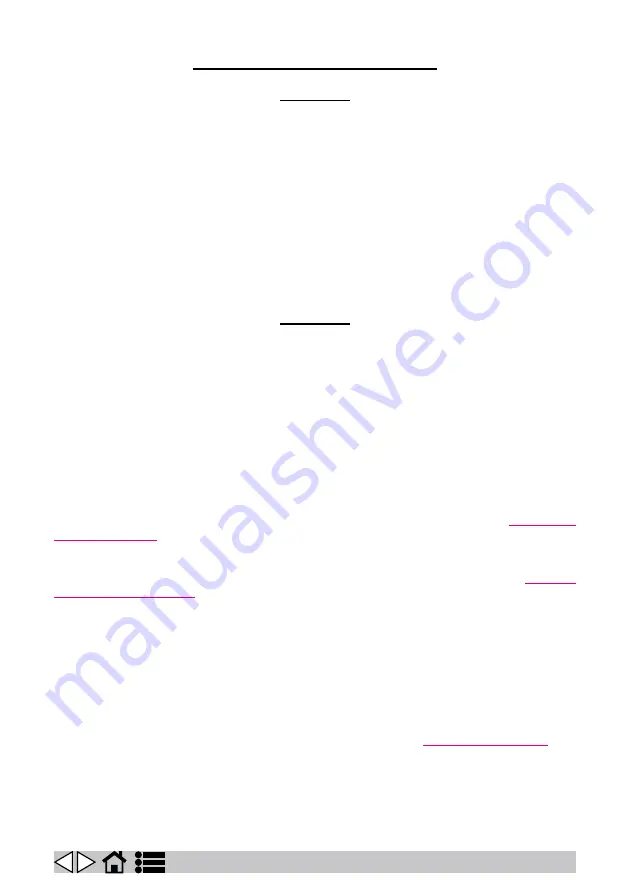
GB
MOVEMENT INSTALLATION
Lifting and transporting the packaged machine
! WARNING!
During all lifting operations, make sure the packaged machine is firmly secured to avoid it
tipping up or being accidentally dropped.
Always load/unload lorries in adequately illuminated areas.
The machine is packaged on a wooden pallet by the Manufacturer. It must be loaded on to the trans-
porting vehicle using suitable equipment (see EC Directive 89/392 and subsequent amendments
and/or additions). At destination, it must be unloaded using similar means.
A fork lift truck must always be used to lift the packaged body of the machine. Handle with care to
avoid knocking or overturning the machine.
Delivery checks
When the carrier delivers the machine, make sure the packaging and machine are both whole and
undamaged. If the machine is damaged, make sure the carrier is aware of the damage and before
accepting the goods, reserve the right (in writing) to request compensation for the damage.
Unpacking
! WARNING!
When unpacking the machine, the operator must be provided with the necessary personal
protection devices (gloves, goggles, etc.) to limit the risk of injury.
Proceed as follows to unpack the machine.
►
Cut and remove the plastic straps using scissors or nippers.
►
Remove the cardboard packaging.
►
Remove the bags from the battery compartment and check their contents:
this Operator’s Manual, the maintenance manual, declaration of conformity, certificate of
warranty;
battery bridges with terminals;
connector for battery charger.
Depending on the model, remove the metal brackets or cut the plastic straps fixing the machine
chassis to the pallet.
Using a sloping ramp, push the machine backwards off the pallet; see the paragraph “
” for details on engaging/disengaging the electric brake on the drive wheel.
Unpack the brushes from their packaging.
Clean the outside of the machine, taking care to respect safety regulations.
Once the machine is clear of the packaging, proceed to install the batteries (see the “
The packaging may be kept and reused to protect the machine if it is moved to another site or to a
Otherwise it must be disposed of in compliance with current legislation.
Batteries (Battery version)
Two different types of battery may be installed on these machines:
►
Leak-proof tubular batteries: these require regular checks on electrolyte level. When nec-
essary, top up with distilled water until the plates are covered. Do not over-fill (5 mm max.
above the plates).
Gel batteries: this type of battery requires no maintenance.
Battery technical characteristics must correspond to those listed in the
tion. The use of higher capacity batteries could seriously jeopardise manoeuvrability and lead to
the drive motor overheating. Batteries with a lower capacity and weight will require charging more
Batteries must be kept charged, dry and clean and the connections must be kept tight.
13