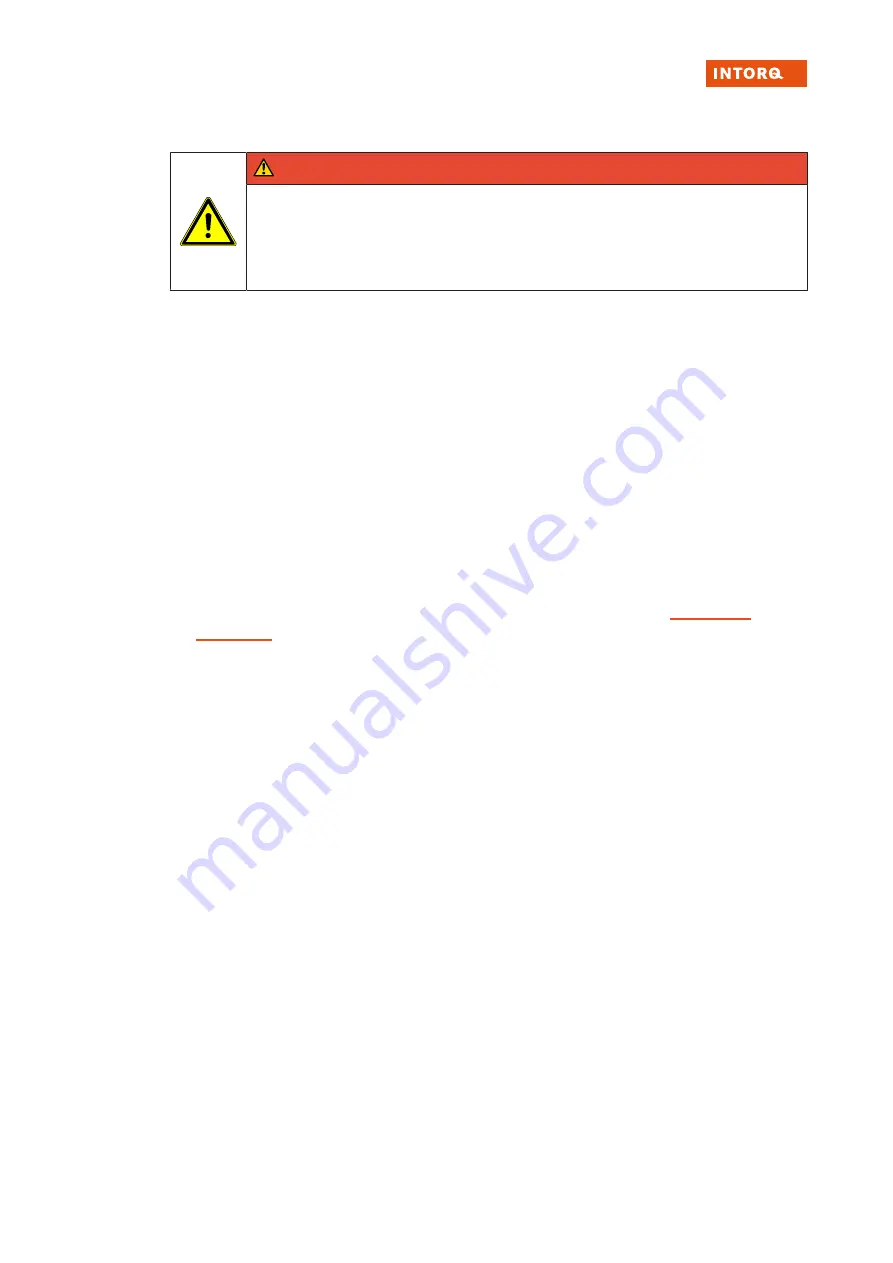
Maintenance and repair
INTORQ | BA 14.0214 | 10/2019
51
8.3.5
Replace rotor
DANGER
Danger: rotating parts!
Switch off the voltage. The brake must be free of residual torque.
Your system should be mechanically immobilized in the event that it could start moving
when the brake is released.
1. Remove the connection cables.
2. Loosen the screws evenly and then remove them.
3. Pay attention to the connection cable during this step! Remove the complete stator from the end
shield.
4. Check the armature plate's friction surface. Replace the complete stator when there is clearly visible
scoring at the running surface.
5. Pull the rotor off the hub.
6. Check the hub's gear teeth.
7. Replace the hub if wear is visible.
8. Check the end shield's friction surface. Replace the friction surface on the end shield when there is
clearly visible scoring at the running surface.
9. You can now install and adjust the new rotor and the complete stator. (Refer to Brake mount-
10. Re-connect the connection cables.
11. If necessary, deactivate the mechanical shutdown of the system.