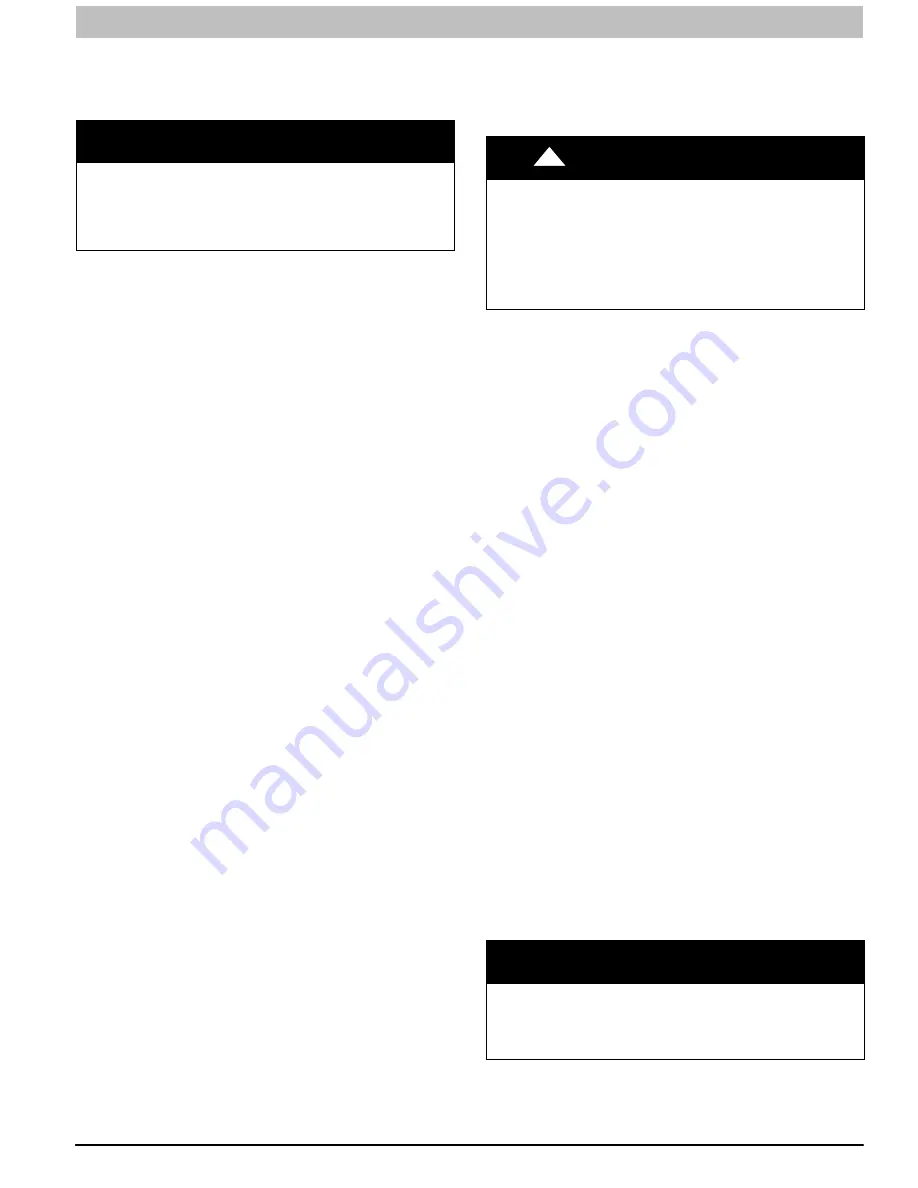
INSTALLATION INSTRUCTIONS
Gas Furnace: N9MSE
440 01 4103 03
47
Specifications subject to change without notice.
5. Insert a length of vent pipe through the coupling into the
outlet of the vent elbow.
6. Tighten the clamp around the outlet of the vent elbow.
Torque the clamp to 15 lb
−
in.
NOTICE
The following instructions are for PVC/ABS DWV vent
piping, only. DO NOT USE THESE TECHNIQUES FOR
POLYPROPYLENE VENT PIPING SYSTEMS. See the
polypropylene vent system manufacturer’s instructions
for installing polypropylene venting systems.
Install the remaining vent and combustion air pipes as shown
below. It is recommended that all pipes be cut, prepared, and
preassembled before permanently cementing any joint.
1. Working from furnace to outside, cut pipe to required
length(s).
2. De
−
burr inside and outside of pipe.
3. Chamfer outside edge of pipe for better distribution of
primer and cement.
4. Clean and dry all surfaces to be joined.
5. Check dry fit of pipe and mark insertion depth on pipe.
6. Insert the vent pipe into the vent elbow.
7. Torque clamp on vent elbow 15 lb
−
in.
8. Torque clamp on vent coupling 15 lb
−
in.
9. Insert the combustion air pipe into the adapter.
10. Pilot drill a screw hole through the adapter into the
combustion air pipe and secure the pipe to the adapter
with sheet metal screws. DO NOT DRILL INTO
POLYPROPYLENE VENT PIPES. Use an optional
accessory vent coupling, if needed.
11. Seal around the combustion air pipe with silicone or foil
tape. SILICONE SEALERS MAY NOT BE
APPROPRIATE FOR POLYPROPYLENE VENT
SYSTEMS. SEE POLYPROPYLENE VENT SYSTEM
MANUFACTRUER’S INSTRUCTIONS.
12. After pipes have been cut and preassembled, apply
generous layer of cement primer to pipe fitting socket
and end of pipe to insertion mark. Quickly apply
approved cement to end of pipe and fitting socket (over
primer). Apply cement in a light, uniform coat on inside of
socket to prevent buildup of excess cement. Apply
second coat. DO NOT CEMENT POLYPROPYLENE
FITTINGS.
13. While cement is still wet, twist pipe into socket with
1/4
−
in.
turn. Be sure pipe is fully inserted into fitting
socket.
14. Wipe excess cement from joint. A continuous bead of
cement will be visible around perimeter of a properly
made joint.
15. Handle pipe joints carefully until cement sets.
16. Horizontal portions of the venting system shall be
supported to prevent sagging. Support combustion air
piping and vent piping a minimum of every 5 ft. (1.5 M) [3
ft. (.91M) for SDR
−
21 or
−
26 PVC] using perforated
metal hanging strap or commercially available hangars
designed to support plastic pipe.
17. Prevent condensate from accumulating in the pipes by
sloping the combustion air piping and vent piping
downward towards furnace a minimum of 1/4-in. per
linear ft. with no sags between hangers.
18. Complete the vent and combustion air pipe installation
by connecting to the concentric vent or by installing the
required termination elbows as shown in
Figure 47
and
Figure 48
, Alberta
Figure 44
and
Figure 46
. For
ventilated combustion air terminations, refer to
Figure 48
, Alberta
Figure 44
and
Figure 46
.
19. Use appropriate methods to seal openings where
combustion air pipe and vent pipe pass through roof or
sidewall.
WARNING
!
CARBON MONOXIDE POISONING HAZARD
Failure to follow this warning could result in personal
injury or death.
DO NOT use cement to join polypropylene venting
systems. Follow the polypropylene venting system
manufacturer’s instructions for installing polypropylene
venting systems.
Optional Installation of the Vent Pipe
NOTE
: DO NOT USE THIS TECHNIQUE FOR
POLYPROPYLENE VENTING SYSTEMS.
This option provides a disconnect point for the vent pipe. The
vent pipe must be cemented to the plastic vent pipe adapter to
maintain a sealed vestibule. See
Figure 42
and
Figure 43
1. Insert a length of vent pipe through the casing into the
outlet of the vent elbow.
2. Slide the plastic vent pipe adapter over the length of the
vent pipe down to the furnace casing. Mark the pipe
where it is flush with the outlet of the adapter.
3. Remove the pipe from the furnace and the adapter and
cut off any excess pipe.
4. Clean and prime the end of the pipe that is flush with the
vent adapter with a primer that is appropriate for the type
of pipe being used.
5. Re
−
insert the pipe through the casing into the vent
elbow.
6. Tighten the clamp around the outlet of the vent elbow.
Torque the clamp to 15 lb
−
in.
7. Apply cement to the end of the pipe and to the inside of
the plastic vent adapter.
8. Slide the adapter over the vent pipe and align the screw
holes in the adapter with the dimples in the furnace
casing.
9. Pilot drill 1/8
−
in. screw holes for the adapter in the casing
and secure the adapter to the furnace with sheet metal
screws.
10. Loosen the clamps on the rubber vent coupling.
11. Slide the end of the coupling with notches in it over the
standoffs in the vent pipe adapter.
12. Tighten the clamp of the coupling over the vent pipe
adapter. Torque the lower clamp around the vent pipe
adapter to 15 lb
−
in.
13. Pilot drill a 1/8
−
in. hole in the combustion air pipe
adapter.
14. Complete the vent and combustion air pipe as shown in
“Install the Vent
and Combustion Air Pipe”
NOTICE
FOR POLYPROPYLENE VENTING SYSTEMS
When using polypropylene venting systems, all venting
materials used, including the vent terminations, must
be from the same manufacturer.