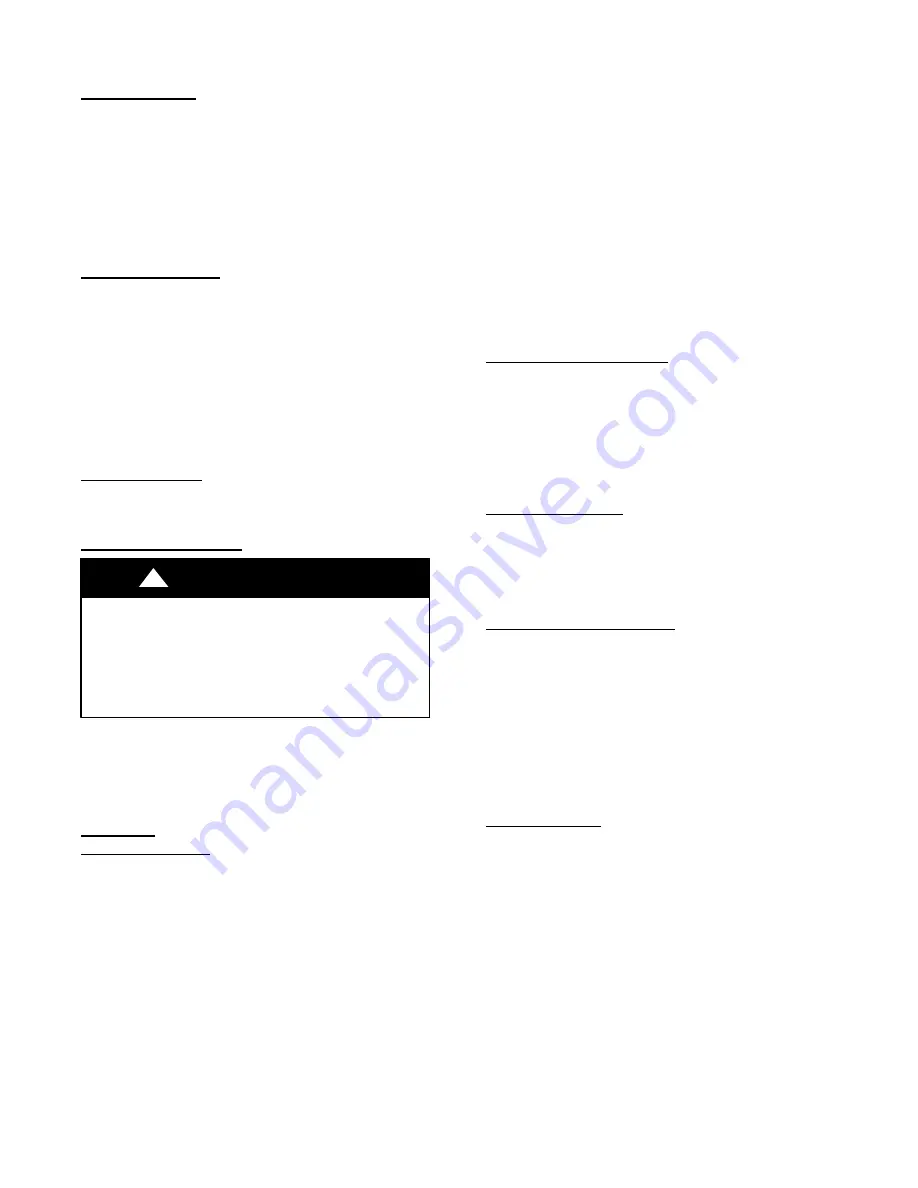
Specifications are subject to change without notice.
12
441 01 7201 00
installations, if the furnace is not suspended from the floor joists,
the ground underneath furnace must be level and the furnace set
on blocks or bricks.
Roll- Out Protection
Provide a minimum 17- 3/4 in. x 22 in. (451 mm x 559 mm)
piece of sheet metal for flame roll- out protection in front of
burner area for furnaces closer than 12 inches (305 mm) above
the combustible deck or suspended furnaces closer than 12 inches
(305 mm) to joists. The sheet metal MUST extend underneath the
furnace casing by 1 in. (25 mm) with the door removed.
The bottom closure panel on furnaces of widths 17- 1/2 in. (445
mm) and larger may be used for flame roll- out protection when
bottom of furnace is used for return air connection. See Fig. 17
for proper orientation of roll- out shield.
Bottom Return Air Inlet
These furnaces are shipped with bottom closure panel installed in
bottom return- air opening. Remove and discard this panel when
bottom return air is used. To remove bottom closure panel,
perform the following:
1. Tilt or raise furnace and remove two screws holding bot-
tom filler panel. (See Fig. 9)
2. Rotate bottom filler panel downward to release holding
tabs.
3. Remove bottom closure panel.
4. Reinstall bottom filler panel and screws. Side Return Air
Inlet
Side Return Air Inlet
These furnaces are shipped with bottom closure panel installed in
bottom return- air opening. This panel MUST be in place when
side return air inlet(s) is used without a bottom return air inlet.
FILTER ARRANGEMENT
CARBON MONOXIDE AND POISONING
HAZARD
Failure to follow this warning could result in personal
injury, or death.
Never operate a furnace without a filter or with filter access
door removed.
!
WARNING
There are no provisions for an internal filter rack in these
furnaces.
A field- supplied accessory external filter is required.
Refer to the instructions supplied with the external filter rack for
assembly and installation options.
AIR DUCTS
General Requirements
The duct system should be designed and sized according to
accepted national standards such as those published by: Air
Conditioning Contractors Association (ACCA), Sheet Metal and
Air Conditioning Contractors National Association (SMACNA)
or American Society of Heating, Refrigerating and Air
Conditioning Engineers (ASHRAE) or consult The Air Systems
Design Guidelines reference tables available from your local
distributor. The duct system should be sized to handle the
required system design CFM at the design external static pressure.
The furnace airflow rates are provided in Table 5 - AIR
DELIVERY- CFM (with filter).
When a furnace is installed so that the supply ducts carry air
circulated by the furnace to areas outside the space containing the
furnace, the return air shall also be handled by duct(s) sealed to
the furnace casing and terminating outside the space containing
the furnace.
Secure ductwork with proper fasteners for type of ductwork used.
Seal supply- and return- duct connections to furnace with code
approved tape or duct sealer.
NOTE
: Flexible connections should be used between ductwork
and furnace to prevent transmission of vibration. Ductwork
passing through unconditioned space should be insulated and
sealed to enhance system performance. When air conditioning is
used, a vapor barrier is recommended.
Maintain a 1- in. (25 mm) clearance from combustible materials
to supply air ductwork for a distance of 36 in. (914 mm)
horizontally from the furnace. See NFPA 90B or local code for
further requirements.
Ductwork Acoustical Treatment
NOTE
: Metal duct systems that do not have a 90 degree elbow
and 10 ft. (3 M) of main duct to the first branch take- off may
require internal acoustical lining. As an alternative, fibrous
ductwork may be used if constructed and installed in accordance
with the latest edition of SMACNA construction standard on
fibrous glass ducts. Both acoustical lining and fibrous ductwork
shall comply with NFPA 90B as tested by UL Standard 181 for
Class 1 Rigid air ducts.
Supply Air Connections
For a furnace not equipped with a cooling coil, the outlet duct
shall be provided with a removable access panel. This opening
shall be accessible when the furnace is installed and shall be of
such a size that the heat exchanger can be viewed for possible
openings using light assistance or a probe can be inserted for
sampling the airstream. The cover attachment shall prevent leaks.
Upflow and Horizontal Furnaces
Connect supply- air duct to flanges on furnace supply- air outlet.
Bend flange upward to 90
_
with wide duct pliers. (See Fig. 14)
The supply- air duct must be connected to ONLY the furnace
supply- outlet- air duct flanges or air conditioning coil casing
(when used). DO NOT cut main furnace casing side to attach
supply air duct, humidifier, or other accessories. All accessories
MUST be connected to duct external to furnace main casing.
NOTE
: For horizontal applications, the top- most flange may be
bent past 90 degrees to allow the evaporator coil to hang on the
flange temporarily while the remaining attachment and sealing of
the coil are performed.
Downflow Furnaces
Connect supply- air duct to supply- air outlet on furnace. Bend
flange inward past 90
_
with wide duct pliers. (See Fig. 14) The
supply- air duct must be connected to ONLY the furnace supply
outlet or air conditioning coil casing (when used). When installed
on combustible material, supply- air duct must be connected to
ONLY the factory- approved accessory subbase or a factory-
approved air conditioning coil casing. DO NOT cut main furnace
casing to attach supply side air duct, humidifier, or other
accessories. All accessories MUST be connected to duct external
to furnace casing.